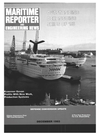
Page 51: of Maritime Reporter Magazine (December 1993)
Read this page in Pdf, Flash or Html5 edition of December 1993 Maritime Reporter Magazine
Technical, Work Innovations
Revolutionize Kvaerner's Govan Yard by Marcus Gibson, contributing editor
Queen Elizabeth visited the now-profitable Kvaerner Govan yard to name the bright orange chemical carrier Jo Selje, pictured above.
Five years ago it seemed impos- sible. Yet a British shipyard, losing nearly $60 million a year and com- mitted to restrictive practices, has turned a profit using a series of new working methods and technological enhancements.
Finally, said Kjell Mikalsen, managing director of Kvaerner's shipyard in Glasgow, Scotland,
Govan is in the black.
After pumping $26.6 million in investment and absorbing nearly $40 million in cumulative losses into the historic yard since 1988, Norwegian shipbuilder Kvaerner triumphantly expects to make a tiny profit of just $370,000 this year to December on a turnover of $118.4 million.
To coincide with the news, Queen
Elizabeth visited the yard to name a bright orange, 35,000-ton, envi- ronmentally-friendly chemical tanker at a ceremony in early Octo- ber. The orange-painted Jo Selje is the first of its type to be built with a full 6.5-foot double skin around the hull. It will comply with OPA 90 and any new IMO/Marpol regulations introduced in the wake of the Valdez disaster. The Jo Selje's 29 fully segmented tanks provide flexibility over cargoes because it can load or discharge a large variety of different cargoes for a multiplicity of locations simultaneously.
The ship is one of nine newbuilds over the past three years for
Norway's Jo Tankers line, the fourth largest chemical tanker operator.
Two are to be constructed at
Kvaerner's Floro yard in Norway for delivery this November and next
May.
Productivity = Profit
The key to Govan's turnaround has been vastly improved productiv- ity. Staff levels have fallen to around 1,500, but new working practices and technology have worked miracles. Instead of the old system in which 70-ton sections were con- structed out on the open berths — prone to all weathers — a series of indoor "tank assembly" sheds have been built, costing around $16.3 mil- lion. Huge block units up to 1,500 tons can now be welded together without interruption. The nine or more blocks can then be wheeled out to the berth on bogie machines and welded, sausage-like, into place.
The regular working makes forward planning infinitely more accurate.
The percentage of tasks utilizing automatic or semi-automatic weld- ing has increased from two percent, when the yard was taken over by
Kvaerner, to 80 percent today. Fur- thermore, says personnel director
Bobby Gordon, "We are designing ships that are easier to build."
The main improvement up to 1996 will be mainly achieved through more efficient working methods. "We want them to work smarter, not harder," said one manager.
All restrictive labor practices have been abolished. The fullest flexibil- ity between craftsmen has been in- troduced, office staff cut by 30 per- cent and union shop stewards re- duced from 90 to 30. Bell-to-bell working has helped cut absentee- ism to a minimum.
Skilled workers now service them- selves rather than being dependent on assistants. Employees have been trained in the classroom in how to work more efficiently in teams, and almost every worker has attended some type of training course. Weld- ers have been taught how to handle stainless steel, a common material used in chemical carriers.
From lessons learned when build- ing the first of the new chemical carriers, managers expect a 10 to 20 percent reduction in man-hours be- tween the first and the last vessel in each series.
Kvaerner's Govan is buoyant about the future. "Third-quarter growth in newbuild contracts are the highest since the mid-80s, at nearly 400," says Mr. Mikalsen.
Three more ships of similar size — for Norway's Storli group and Saudi
Arabia's National Chemical Carri- ers — will be built following the Jo
Selje at Govan. A $296 million or- der, it is the largest single merchant shipbuilding contract to be placed in
Britain.
In 1996 the Govan yard will also build the hull and fit out the British
Royal Navy's new helicopter carrier as a sub-contractor to the U.K. mili- tary submarine group VSEL. "Now there's a real need for new ships,"
Mr. Mikalsen added. New envi- ronmental rules may cut short the working lives of much existing ship- ping, he suggested, and rates of scrapping and trade volumes in the
Far East will rise, boosting demand. "Since the early 80s, ships have been replaced at a rate of only four per- cent each year," said Mr. Mikalsen. "We believe this may rise to five or six percent."
Kvaerner is the largest ship- builder in Europe and the fourth largest in the world in terms of com- pensated gross tonnage. Its world- wide orderbook — 40 ships totalling 2.5 billion tons — is second only to
Hyundai of Korea. With a $1.48 billion turnover and 9,500 staff in its shipping group, the company is spe- cializing in niche markets. Com- plex, high-quality chemical or LPG carriers are constructed in huge chunks using Govan's new block- unit technology capabilities.
Kvaerner's managers in Scotland believe the Govan yard will be the lowest cost shipyard in the group, outranking counterparts in Norway,
Finland, Sweden and Germany. The managers hope to squeeze a further 40 percent cut in manhours at the site in productivity improvements over the three years to 1996. Lower materials costs — a substantial por- tion of total costs — are also a prior- ity. Kvaerner was angered when
British Steel demanded 10 percent more for Jo Selje's sheet steel if she was to be built at Govan rather than
Norway. "British Steel claimed Norway was a virgin market that merited a lower price," said one of Govan's finance team. But there were other difficulties on the horizon. Russia,
Brazil and Taiwan may renew their efforts to grab a bigger slice of the world market. Korea may have taken a big chunk from Japan, which still held 39 percent of the newbuild market last year. In Japan, newbuild prices are fractionally be- low the break-even point, whereas in Korea, prices have tripled in the local currency, the won.
Kvaerner still has some grumbles over the U.K.'s clawback rules over profits made from subsidized con- tracts, but the company seems de- lighted by the accelerated efficiency at Govan. The historic shipyard, where the first ironclads were built in the 1860s, and Scottish engineer
James Elder pioneered the com- pound steam engine, brought an end to the days of sail. Kvaerner has made Govan, the last of 13 Up- per Clyde shipbuilders that once launched half the world's tonnage, a modern shipyard that can com- pete in the present. "We will never regret the step we took," Mr. Mikalsen said.
Craft America W
Production Support Services ^Turnkey Contracting - Hull, Pipe, Mechanical, and Electrical * Pre-fabrication and Installation - Weldments, Foundations, and
Piping Systems * Tiger Teams - Project Management, Supervision, Skilled Labor and
Equipment
Over one hundred (100) Welders certified under Mil-Std 248D, A WS
Dl.l, ABS, Coast Guard, and ASME Section VIII and IX
Specializing in Aluminum Fabrication/Production Welding
Engineering Support Services *Weld Engineering, Weld Metallurgy, and Naval Architecture. * Specific Engineering Tasking or Project related support. * Welding Procedures and Process Parameters developed and implemented. 1302 Ingleside Road
Norfolk, Virginia 23502
Telephone: (800)859-1213
Facsimile: (804)857-1822
December, 1993 Circle 269 on Reader Service Card 53