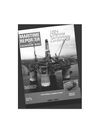
Page 57: of Maritime Reporter Magazine (April 1994)
Read this page in Pdf, Flash or Html5 edition of April 1994 Maritime Reporter Magazine
ABOVE: Kvaerner Masa-Yards Technology's future fast ferry is a triple-keel vessel.
BELOW: The ultra-slim one-keel ferry (Slender Monohull) is another future Kvaerner product.
Tank
Dome
Double bottom
Large spherical panels are welded together in three tilting jigs. The jigs are synchronized with welding towers fitted with automatic high-energy welding equipment.
Kvaerner Masa-Yards Debuts
LNG Tank Production Plant
A production plant for the manufacturing of spherical liquefied natural gas (LNG) tanks was established, and recently unveiled, at
Kvaerner's Turku New Shipyard. The three new workshops include production equipment and a personnel training program, requiring an investment of approximately $46.9 mil- lion. The new LNG tank production facility, which started in December of 1989, will allow 400 trained staff to carry out the construction of the spherical 40-meter diameter aluminum tanks. After successful testing in 1992,
Kvaerner was able to quote prices on several
LNG vessel inquiries using the new technol- ogy. The first task of the new production plant will be to manufacture the cargo tanks for the four 135,000-sq.-m. LNG carriers under con- struction for Abu Dhabi National Oil Co. (ADNOC), of the United Arab Emirates. The deliveries of the vessels are scheduled for 1996 and 1997, and the four vessel order will encompass 16 LNG tanks.
LNG TANK PRODUCTION
The LNG tanks are made of heat-die formed aluminum panels with material thicknesses ranging from 30 mm up to 60 mm. The spherical tank is supported by a 169-mm thick equatorial ring. The gas tanks for the four vessels ordered require approximately 12,000 tons of aluminum.
The new tank production plant consists of three workshops: the Manufacturing Work- shop; the Assembly Workshop no. 1; and the
Assembly Workshop no. 2—encompassing a total area of about 20,000-sq.-m.
In the Manufacturing Workshop flat alu- minum plates are welded together to a panel of nearly lOO-sq.-m. The welded panels are heat-die formed to spherical curvature at +440°
C, and cooled under controlled conditions in the adjacent cooling chamber, after which the edges are machined via a seven-axis bevelling machine. In the Assembly Workshop no. 1, the spherical panels are welded together in pairs using tilting jigs. The jigs are synchro- nized with welding towers fitted with auto- Moss Type LNG Carrier Hull Structure. matic High Energy MIG welding equipment.
In both Assembly Workshops, the multipanels are assembled into ring segments using seven assembly jigs. All welding is mechanized and automated.
The workshop roofs are sliding and the tank parts are moved using the yard's gantry crane.
The finished lower, mid and upper tank seg- ments are transferred directly onboard the vessel for final joining including the assembly of the pump tower.
The spherical LNG tanks are produced un- der Kvaerner Moss Technology license, but the manufacturing method developed at
Kvaerner Masa-Yards' Turku New Shipyard is new. By making multiplated flat panels before heat-die forming, the more difficult and expensive welding of curved parts can report- edly be reduced. Also, welding methods and equipment have been under development at the yard's Welding Laboratory. The four year development work has resulted in a number of international patents pending. For more in- formation on Kvaerner's new LNG tank pro- duction facilities and capabilities,
Circle 7 on Reader Service Card
April, 1994 43