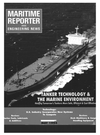
Page 31: of Maritime Reporter Magazine (May 1994)
Read this page in Pdf, Flash or Html5 edition of May 1994 Maritime Reporter Magazine
T
The wind's blowing in the right direction for Cegelec partners
For a long time, we have been optimizing the solutions for marine electrical systems, electrical drives and ship automation.
In particular, in the field of diesel electrical propulsion, our highly regarded international reputation and the skills and willingness of our team make us your first choice partner - a partner who understands your needs and how to fulfill them.
The cruiseliners Star Princess, Crown Princess, Regal Princess and Club Med 2 are powered by Cegelec AC electrical propulsion, and at present five other ships are being built using the same concept. Cegelec's innovative solutions mean that ships will set sail more efficiently, safely and comfortably.
This is surely a mandate for success.
Cegelec : Electrical Engineering of the Alcatel Asthom Group
Industrial Equipment Division. 3, avenue des Trois Chenes. 9001 8 Belfort Cedex France - Tel. (33) 84.55.30.30 - Fax : (33) 84.55.20.65.
Circle 284 on Reader Service Card
Chantiers To Start Delivering Tankers
Yard develops a number of automated processes arid machines for the construction of LNG tankers
Chantiers de l'Atlantique, a sub- sidiary of GEC Alsthom, is building five methane carriers for Petronas
Marine of Malaysia. The keel for the first of the five tankers was laid in September 1992. This tanker will be delivered in July 1994; deliv- ery of the remaining four ships will be staggered between July 1994 and
July 1997. The 130,000-cu.-m. liq- uefied natural gas (LNG) carriers have been constructed using auto- mated manufacturing and assem- bly processes. Each LNG carrier has four tanks which are incorpo- rated in the ship's metal structure.
Thermal insulation for the liquid methane cargo is provided by a double layer of plywood boxes filled with perlite, an insulating powder made of volcanic materials.
Gastightness is ensured by a 0.7- mm-thick membrane made of Invar, a steel and nickel alloy which has an extremely low coefficient of ther- mal expansion. For safety reasons, a second, identical membrane is placed between the two layers of boxes to ensure tightness in the event of a leak in the first mem- brane. To minimize the cost of assembly operations aboard the ships, components have been ex- tensively standardized and wide- spread use has been made of prefab- rication techniques. The construc- tion of a carrier requires 50,000 plywood boxes, each measuring 1 m (3.3 ft.) by 1.2 m (3.9 ft.), which are produced in a fully automated, pur- pose-built workshop on site. In addition, the special Invar parts forming the tank corner structures are made in completely pre-fabri- cated 10 foot (3 m) long elements.
Special attention has been given to optimizing the supply of the many components installed aboard the ship. Materials are delivered by the erectors themselves using the "just- in-time" method with the aid of a computer system.
One of the first operations to be carried out inside the tanks is to weld metal elements called coupler studs to the ship's double hull, work- ing from data provided by a preci- sion topographical survey. The studs anchor the first layer of boxes.
Chantiers de l'Atlantique has de- veloped a special device for this purpose. The Dromadec system comprises a viewing unit, an on- board computer, a stud positioning arm and a welding torch. Using the topographical data provided by a laser and a distance measuring de- vice, the computer places each cou- pler at the desired position before welding it automatically to the double hull. Dromadec reportedly makes it possible to achieve the precision specifications set for as- sembling the tank's insulation ele- ments, namely a +/- 0.9 mm posi- tioning accuracy for the studs rela- tive to the topographical data.
Chantiers de l'Atlantique and a number of specialist firms have worked together to develop ma- chines to automate the welding of
May, 1994 33 the membranes and achieve maxi- mum quality. A single ship requires 90,000 m of resistance seam weld- ing and 21,000 m of TIG welding.
For more information on Chantiers de l'Atlantique,
Circle 39 on Reader Service Card
Cegelec: a long-term vision for electrical propulsion