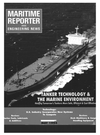
Page 42: of Maritime Reporter Magazine (May 1994)
Read this page in Pdf, Flash or Html5 edition of May 1994 Maritime Reporter Magazine
Tanker Technology
Emphasis is now on life extension. The Chevron-owned David Packard was sold to new Greek owners.
Tanker Technology: Its Effect On Shipyards by
Alan Thorpe, International Editor
The main advance seen re-cently in the construction of tankers is the use of double hull designs. Yards building such ships have had to change not only the design factors but also, in many cases, the produc- tion facilities and methods to en- able suitable ships to be built. In the case of the VLCC market there has also been a change of steel utilized in the construction process, to enable longer service life.
The subsequent OPA '90 rulings governing tanker operation has led to many '70s-built ships being able to trade well after their "sell by" dates, thus reducing the expect- ancy of a major boom in the large tanker building market. In some owners' minds the emphasis has shifted from newbuilding to life extension of existing tonnage.
The large tanker market (above 200,000 dwt) has been an interest- ing aspect of the shipbuilding in- dustry for the past few years, when many "players" have suddenly real- ized that new tonnage is still re- quired.
Owners have been reluctant to scrap older tonnage, which still manages to obtain charters despite the posturing of the classification societies and various major oil com- panies, which claim to fix only high standard vessels.
It is therefore unlikely that a major scrapping boom will develop.
What is more likely is that new tonnage coming onto the market, especially with South Korea con- tinuing its efforts to expand ship- yard facilities, will keep freight rates down.
There has been a shift in owner- ship of the large tanker fleets, the major oil companies making it no secret that they feel shipowning should be for the independents and the oil companies should remain as charterers.
Meanwhile, the Middle East ex- porting countries, such as Saudi
Arabia, Iran and Kuwait, are all involved in the process of building up tanker fleets.
As the current low freight rates continue, the shipyards have to look very closely at construction programs to lower the overall cost of the newbuilding.
One obvious method is by "series" building, a popular method in Japan and South Korea.
The Japanese have been success- ful in the first session of building such vessels; virtually all yards hav- ing single and double skin designs available.
The most popular size of vessel in the '90s has been the 280,000-dwt "USmax" vessel, many of the inde- pendent owners and U.S. majors looking to this size of ship. The
Middle East owners, such as Saudi
Arabia's Vela and Kuwait's KOTC, have looked at other sizes.
The one problem arising in the
Japanese shipyards has been one of productivity to meet certain quotas of ship deliveries laid down by the
Japanese government.
During various cutbacks in the '80s, Japan's shipbuilding industry was reduced to various specific quo- tas.
For example, the Kure yard of
IHI has a quota of five VLCC deliv- eries each year, this quota likely to be retained even though double- skinned ships involve another 25% steel content.
The majority of Japanese yards therefore have embarked on vari- ous methods by which production can be increased without the banned method of increasing physical ca- pacity.
The main methods chosen have been larger module building proce- dures, which has led to an increase of cranage and yard transportation units, increased automation and, in some cases, included robotics.
NEW REQUIREMENTS; NEW
COATINGS CHALLENGES
One of the main problems facing the yards is that of coating opera- tions in the double hull spaces. The physical limitations of carrying out such work is time consuming and not assisting the yard's battle to reduce construction times.
The necessity to coat the spaces with suitable long-life products is expensive and again, not conducive to the yard's attempts to reduce costs. Many yards therefore look to the cheaper option, which may be a major worry later in the vessels' service life.
Traditionally, coatings for bal- last spaces were specified by the shipbuilder with the owner usually having little input.
Often the shipyard had a pre- ferred manufacturer who supplied the coatings, year in and year out.
However, the massive increase in ballast tank areas as a result of the double hull designs is now changing traditional attitudes, fast.
The prospect of having to inspect and maintain these areas means that shipowners are now looking for long-life systems, which will reduce maintenance to the minimum. This is leading to the selection of high performance coatings and prepar- 44 Maritime Reporter/Engineering News