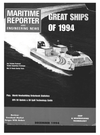
Page 36: of Maritime Reporter Magazine (December 1994)
Read this page in Pdf, Flash or Html5 edition of December 1994 Maritime Reporter Magazine
Hanne Knutsen (Continued from page 32) as well as for the main alternators, auxiliary systems and electric mo- tors of the thrusters. Sea water cooling circuit pipes are made of copper-nickel.
The loading System
In addition to the conventional loading systems, the vessel is equipped with two "offshore" load- ing systems: one for articulated load- ing turrets (APC) and buoys (OLS); and a submerged turret loading sys- tem (STL). The Hanne Knutsen is reportedly the first newbuilding in- corporating both systems.
The loading systems and tank arrangements are designed to handle crude oils with low vapor tensions in two segregations.
Four transversal collectors have been installed in the cargo manifold for crude oil and two others to send the cargo vapors to shore. Inert gas is generated and purified in a
Flexinert plant with the vapors com- ing from the main diesel genera- tors.
The ship features a sophisticated integrated control system redun- dantly computerized with process stations and a local area network (LAN) with control stations in the engine room, cargo control and wheelhouse.
The automation system in the engine room is designed to be oper- ated without personnel, and the automation in the wheelhouse is designed to be operated by one per- son.
Hanne Knutsen Equipment List
Main generators driving engines Sulzer
Auxiliary generator engine Bergen
Main propulsion electric motor ABB
Electric generators AB
Sterntube bearing Rolla
Propeller NavaLips
Emergency generating set Caterpillar
F.W. generating plant Alfa Laval
Coolers Alfa Laval
Centrifugal pumps Kvaerner Eureka
Screw pumps Kvaerner Eureka
F.O. & L.O. Purifiers Alfa Laval
Foam F.F. system Unitor
Air compressors Roweco
Sewage treatment plant Aries
Steering gear Porsgrunn
Transverse bow & stern thrusters Ulstein
Active rudder Willi Becker
Steel pipes Almesa/Cunado
GRP pipes Sarplast
Main switchboard & Cycloconverters ABB
Electric cables (automation) Ericsson
Fire detection Salwico
DPS Simrad
Radio communications S.R.M.
Radars Atlas-Krupp
Gyropilots Anschutz
Doppler log Atlas-Krupp
Echosounding Simrad
Satellite navigator Saturn-ABB
Bridge integration Kvaerner Eureka
Integrated control system Simrad
Deck machinery Ulstein
Service crane Navacel
Access hatches Faro
Doors & Windows Aux. Naval
Coatings Sigma
Lifeboats & Davits Harding
Modular cabins A.E.S.A.
Air conditioning Novenco
Pumps Kvaerner Eureka
Oil monitoring system Seres
Tank cleaning equipment Consilium
Inert gas generating plant Maritime Protection
Pressure & Vacuum valves Pres-Vac
Cargo valves & Control system.... Kvaerner Eureka
Cargo tanks level indicators Saab
Gas detection equipment Omicron
Yard: Chantiers de I'Atlantique
Ship: Petronas Tanker
Type: LNG Tanker
Owner: Petronas Marine
Length: 889 ft. (271.1 m)
Breadth: 142 ft. (43.3 m)
Depth (to upper deck): 103 ft. (31.4 m)
Draft: 36 ft. (11 m)
Total cargo volume: 130,300-cu.-m.
Speed: 21 knots
For more information on Chantiers de I'Atlantique
Circle 49 on Reader Service Card
Chantiers de I'Atlantique, a sub- sidiary of GEC Alsthom, delivered in July the first of five methane carriers for Petronas Marine of
Malaysia. The keel for the first vessel was laid in September 1992, and the production schedule for the series of five will run through July of 1997. The 130,000-cu.-m. lique- fied natural gas (LNG) carriers have been constructed using automated manufacturing and assembly pro- cesses. Each ship has four tanks which are incorporated in the ship's metal structure.
Liquefied natural gas is stored in four tanks, and the Petronas vessel is the first which combines the Gaz
Transport Membrane system with a reduction in the number of tanks: four-cargo-tank design, as opposed to a design incorporating five or six cargo tanks, which was previously associated with the system.
Thermal insulation for the liquid methane cargo is provided by a double layer of plywood boxes filled with perlite, an insulating powder made of volcanic materials.
Gastightness is ensured by a ,7-mm thick membrane made of Invar, a steel and nickel alloy which has an extremely low coefficient of thermal expansion. For safety reasons, a second, identical membrane is placed between the two layers of boxes to ensure tightness in the event of a leak in the first mem- brane. To minimize the cost of as- sembly operation aboard the ships, components have been extensively standardized and widespread use has been made of prefabrication techniques. The construction of a carrier requires 50,000 plywood boxes, each measuring 3.3 ft. (1 m) by 3.9 ft. (1.2 m), which are pro- duced in a fully automated, pur- pose-built workshop on site. In ad- dition, the special Invar parts form- ing the tank corner structures are made in completely pre-fabricated 10-ft. (3-m) long elements.
Special attention has been given to optimizing the supply of the many components installed aboard the ship. Materials are delivered by the erectors themselves using the just- in-time method with the aid of a computer system.
One of the first operations car- ried out inside the tanks is to weld metal elements called coupler studs to the ship's double hull, working from data provided by a precision topographical survey. The studs anchor the first layer of boxes.
Chantiers de I'Atlantique has devel- oped a special device for this pur- pose.
The Dromadec system comprises a viewing unit, an on-board com- puter, a stud positioning arm and a welding torch. Using the topographi- cal data provided by a laser and a distance measuring device, the com- puter places each coupler at the desired position before welding it automatically to the double hull.
Dromadec reportedly makes it pos- sible to achieve the precision speci- fications set for assembling the tank's insulation elements, namely a +/- .9-mm positioning accuracy for the studs relative to the topographi- cal data. Chantiers de I'Atlantique and a number of specialist firms worked to develop machines to au- tomate the welding of the mem- branes and achieve maximum qual- ity. A single ship requires 90,000 m ; of resistance seam welding and r 21,000 m of TIG welding. The ship is powered to a speed of 21 knots at 100 percent MCR (26,720 kW) at 93 ; rpm. The ship is designed to be 3 operated with the LR mark Unat- tended Machinery Space (UMS). 26D Maritime Reporter/Engineering News