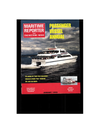
Page 16: of Maritime Reporter Magazine (January 1995)
Read this page in Pdf, Flash or Html5 edition of January 1995 Maritime Reporter Magazine
USS Mitscher (DDG 57), the third U.S. Navy Aegis guided missile destroyer to be built by Ingalls Shipbuilding Division of Litton
Industries, was commissioned in Pensacola, Fla. on December 10, 1994. The Honorable John H. Dalton, Secretary of the Navy, delivered the principal address.
DDG 57, the seventh of the Arleigh Burke (DDG 51) class guided missile destroyers, and the third to be built by Ingalls, was commis- sioned USS Mitscher and reported for Atlantic
Fleet duty during ceremonies at Pensacola Na- val Air Station in Pensacola, Fla. on Dec. 10, 1994.
The Honorable John H. Dalton, Secretary of the Navy, delivered the principal address. Com- mander Roy Balaconis accepted command of the new ship, which will be homeported in Nor- folk, Va.
For more information on Ingalls
Circle 8 on Reader Service Card
Prototype Cargo
Handling System To Be
Tested At Port Of
Gothenburg
A test port facility for a future cargo-handling system is to be built at the Port of Gothenburg's
Alvsborg Harbor. The system will reportedly be able, under favorable conditions, to load and unload 1,600 containers on a ship in less than two hours.
The test harbor is connected to the plans of a very fast shipping line between Gothenburg in
Sweden and Zeebrugge in Belgium, using the so- called FastShip concept. These plans indicated that two ships of a new design could offer daily sailings from each port.
The speed would be in excess of 30 knots, giving a sea time of 17 hours and a revolutionary 1-2 hour port time.
The test port is to be built in the eastern part of the Alvsborg RoRo harbor at Gothenburg.
Before the arrival of a ship, containers and trailers would be placed on special platforms to be used in-terminal and on-ship.
These platforms have air cushion devices fit- ted that make them lift under operation.
The platforms are tied together, a terminal locomotive is attached, and the entire train of platforms is pushed aboard the ship by the RoRo method.
The locomotive provides the power for the air- cushion devices, and rails on the terminal area guide the train of platforms, as do rails onboard the ship.
Each platform can carry two 40-ft. or four 20- ft. containers or one trailer. The ship can carry 800 TEUs. The unloading and loading operation taking between one and two hours, is, according to the port, equal to a 24-hour job on a conven- tional container ship.
The system, called Alicon (for "Air-Lift Con- tainers") was developed by Thornycroft, Giles &
Co. Inc. of Washington, D.C., the same firm that developed the FastShip design.
For more information on Thornycroft, Giles & Co.
Circle 79 on Reader Service Card
Ingalls-Built Destroyers
Christened, Commissioned Krupp Unit's Ship Unloader Transported To Operating Site
New Calculation Method
Designed To Enhance
Propeller Design
Rolla SP Propellers, through participation in a research program with the Massachusetts In- stitute of Technology, helped develop a new and sophisticated "panel method" calculation pro- gram that allows more accurate determination of a propeller design's cavitation characteristics resulting from shaft angle and varying wake.
The study, comprehension, and elimination or reduction of these unwanted characteristics, which can lead to declining propeller perfor- mance and even its rapid deterioration, is par- ticularly important in all cases of high speed boats with highly inclined shaft line and high propeller rpm — which is reportedly the condi- tion in today's most powerful and heavy fast planing boats.
The improvement and validation of the calcu- lation system is carried out by the continual experimentation of new propeller profiles and geometries tested respectively in the cavitation tunnels of the Berlin and Lausanne universities.
This enhances Rolla's ability to scientifically study the parameters that influence propeller characteristics and propose the best propeller design for each application.
For more information on Rolla
Circle 9 on Reader Service Card
More than 700 guests were on hand on November 12,1994 as the new U.S. Navy guided missile destroyer, DDG 65, was christened
Benfold at Ingalls Shipbuilding Division of Litton Industries.
DDG 65 Christened Benfold "The technology embodied in this Aegis de- stroyer is already changing our military's opera- tional strategies and tactics," the HonorablePaul
J. Kaminski, Under Secretary of Defense for
Acquisition and Technology, said at the christen- ing of the Arleigh Burke class Aegis guided missile destroyer Benfold (DDG 65) at Ingalls
Shipbuilding Division of Litton Industries in
Pascagoula, Miss. "These highly capable ships can operate in smaller numbers, with more firepower, against the entire spectrum of threats." The christening took place on Nov. 12, 1994.
DDG 65 is the seventh Aegis destroyer to be launched and christened of 14 ships contracted or allocated to Ingalls. The vessel is named in honor of Hospitalman Third Class Edward
Clyde Benfold, USN, a native of Staten Island,
N.Y., who was posthumously awarded the Medal of Honor for heroism during the Korean War.
DDG 57, Mitscher, Commissioned
In the port of El Ferrol on Spain's northwest- ern coast, a 131.2-ft. (40-m) high continuous ship unloader weighing 1,246 tons was moved from its assembly site to the pier, loaded onto a pon- toon and transported to its operating site. With this unloader Endesa Empresa Nacional de
Electridad SA can continuously unload imported coal from oceangoing vessels of up to 100,000 dwt, at a maximum hourly rate of 2,300 tons.
Commissioning is currently taking place, and a test-unload of the first ship was scheduled for early December 1994.
PWH Anlagen + Systeme GmbH, a subsidiary company of Krupp Fordertechnik GmbH, de- signed the continuous unloader. Imenosa SA, El
Ferrol, manufactured the main structural steel components and assembled the facility complete including the core units supplied by PWH of St.
Ingbert-Rohrbach, such as a bucket elevator, mechanical components and the sampling sta- tion. Assembly of the electrical plant is being handled by Isolux Watt SA, La Coruna.
From the assembly site the continuous unloader was moved approximately 490 ft. (150 m) to the shipyard pier of Astano SA, from where it was edged onto a ballastable pontoon capable of carrying up to 8,900 tons and supplied by
Dragados y Construcciones SA, Madrid.
For more information on Krupp Fordertechnik
Circle 35 on Reader Service Card 18 Maritime Reporter/Engineering News