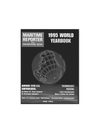
Page 67: of Maritime Reporter Magazine (June 1995)
Read this page in Pdf, Flash or Html5 edition of June 1995 Maritime Reporter Magazine
shering in ozone-friendly frigerants, R-134a
Today most reefer containers and least 20 percent of stationary dpboard systems currently use R- i as a refrigerant. Shipowners anning to retrofit these systems ust first decide on an alternative ifrigerant, because this choice dic- ites the CFC conversion decision nd process.
A professional shipboard survey f the existing system and a thor- ugh engineering evaluation should e done by a reliable marine retrofit ervice contractor before a ship- owner makes his or her decision leeds. Shipowners should make certain the contractor they choose ilso provides efficient follow-up ser- /ice and worldwide warranty pro- tection. While no single solution is ideal for all applications, most an- ticipated marine retrofits will likely involve the conversion of R-12 sys- tems to R-134a (also referred to as
HFC-134a). With its zero ozone depletion potential and low global warming potential, R-134a is con- sidered by many to be the long term marine refrigerant of choice. The ozone-friendly R-134a refrigerant is produced by many global manu- facturers and is already commonly used in commercial, industrial and marine applications, ensuring worldwide availability. Global prices of the refrigerant have also been trending lower this year.
The most time-consuming step in the process of converting a R-12 system to R-134a involves a series of oil changes. A retrofit service contractor will repeatedly drain and flush the mineral oil in the R-12 system with a POE lubricant until residual material concentrations are reduced to five percent, the generally accepted maximum level for optimum system efficiency. It has been reported that as many as four oil changes and flushes are required to reach the five percent limit. Service engineers on board the vessel check the levels of re- sidual mineral oil by conducting a simple refractometer test.
Polyolester lubricants are compatible with all refrigerants
Chlorine-free refrigerants like R- 134a are compatible with the envi- ronment, but are not compatible with mineral oil or the alkyl ben- zene synthetic oils traditionally used to lubricate R-12 systems. A compatible lubricant is critical to the system's optimum performance.
It takes a polyolester (POE) lubri- cant, such as Mobil EAL Arctic Se- ries, to lubricate compressors and system components effectively us- ing HFC-134a. Available world- wide through Drew Ameroid
Marine's global network, EAL Arc- tic Series oils are part of Mobil's family of Environmental Awareness
Lubricants (EAL). Mobil manufac- tures its own refrigeration oil basestock. The company also uses a proprietary manufacturing pro- cess to produce an ester with virtu- ally none of the metallic residuals that can cause oxidation and ad- versely affect the thermal stability of a lubricant.
The POE lubricant is made to provide properly controlled miscibil- ity with all refrigerants, and lubric- ity superior to those of mineral oils used with CFCs and HCFCs. Be- cause POEs are hygroscopic (absorb moisture), the company packages the refrigeration oils in steel containers capped with nitrogen to guarantee low moisture content.
At the end of 1995, CFC produc- tion will end around the world. Be- fore long, shipowners using R-12 will find their supplies disappear- ing in early 1996. Some shipowners may also be exposed to unscrupu- lous elements marketing so-called "recycled" R-12, refrigerants con- taining very high moisture levels, destructive noncondensables, metai fines and contaminated mineral oil lubricants. There have been cases reported of recycled R-12 adulter- ated with quantities of-propane.
Shipowners can avoid the prospect of uncertain refrigerant supplies and escalating prices by working with trustworthy suppliers and retrofit- ting experts.
The preceding commentary was submitted by Marketing Commu- nications, Inc., on behalf of Mobil
Marine and Drew Ameroid Ma- rine.
STEELING UP FOR THE 21ST CENTURY
This century has been demanding.
The shipbuilding industry and the designs of the ships being constructed, have changed and changed again. It's taken a lot to keep up with it, and even more to keep ahead of it.
As a separate, specialist company in the Fundia Group and market leaders in structural steel for the shipbuilding industry, Fundia
Profiler has recognised this. It has led the way in improving steel quality, design and innovation with the most and greater cost-effectiveness in building, operating and maintaining ships. advanced and complete programme for shipbuilding profiles in Europe. And it is now leading the way into the next century with its VISION 2000 initiative.
VISION 2000 is all about partner- ship. A partnership between the customer and Fundia Profiler to achieve the optimum solution.
Optimum in terms of: * steel qualities * best profile designs * tight tolerances * JIT delivery
VISION 2000 means lighter ships, faster ships, safer ships fundiq
Nordic steel you can rely on
Fundia Profiler AS, Nydalsveien 15, Postbox 4225 - Torshov, 0401 Oslo, Norway. Tel: +47 22 45 08 20. Fax: +47 22 18 35 69
An ISO 9002 certified company
Circle 394 on Reader Service Card
It means using the expertise of
Fundia Profiler to meet the demands of your customers and the customers of tomorrow.
It means preparing for the 21st century - because the demands will be even greater.
June, 1995 Circle 241 on Reader Service Card Circle 229 on Reader Service Card 69