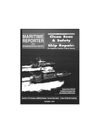
Page 28: of Maritime Reporter Magazine (October 1995)
Read this page in Pdf, Flash or Html5 edition of October 1995 Maritime Reporter Magazine
FOCUS ON CLEAN SEAS
Technology, R&D:
Charting A Steady Course For Cleaner Seas by Bridget A. Murphy, assistant editor Co., Baltimore, Md., with final ma-chinery assembly to be completed at the Westinghouse Marine Division in Sunnyvale, Calif.; and a contract for 21 systems was awarded to Uni- versal Technologies Inc. in Tennes- see. Extendable options include pro- visions for the construction of more than 200 additional PWP systems.
Tech Developments Lend
A Practical Spin To
Waste Management
The PWP equipment is designed for three-step operation, although the process is adaptable depending on the needs of specific vessel appli- cations. After plastic garbage collec- tion, the primary step is insertion of the waste into a shredder, which measures approximately 6-ft. by 2- ft. by 2.5-ft. (1.82 m x .6 m x .76 m), and is equipped with a bin with teeth on the inside. The teeth grind the plastic, and the byproducts descend to a recycling bin at the bottom of the unit. The shredded materials then proceed to the compressed-melt unit —a circular chamber, about two feet deep. "Shredded up plastic put here electrically heats up to over 300 de- grees, emitting no noxious fumes, yet melting plastic," said Mr .Wright.
A piston compresses the plastic as it melts into a 20-in. diameter disk, and shuts off when the process is completed. And disk storage? "They're (naval engineers) just stack- ing them up. Where they had a problem was when they had thirty times the amount. Once you're got
As the buzz concerning MARPOL regulatory compliance continues to gather energy, an issue surfacing is that of design-related compliance.
Advancements in technological re- search and development, along with the implementation of subsequent equipment applications, could, in effect, serve to facilitate dual ac- countability, with environmental responsibility being placed not only with shipowners and operators, but also with vessel designers and build- ers. This would remove some of the burden of enforcement that has be- fallen the U.S. Coast Guard and other regulatory agencies, effectively elimating one of the greatest ob- stacles to the success of MARPOL.
Waste management system improve- ments have dominated the spotlight thus far, most likely due to the fact that vessels with garbage that is efficiently stowed, incinerated, or otherwise compressed are not sub- ject to a high frequency of offloading procedures, which are costly and cumbersome; and are less likely to participate in the potentially more expensive alternative practice of il- legal dumping.
A report — Clean Ships, Clean
Ports, Clean Seas — released on
September 5, 1995, by the U.S. Na- tional Research Council (NRC), the principle operating agency of the
National Academy of Sciences and the National Academy of Engi- neering, includes a discussion of shipboard technologies and practices as related to solid waste management. The re- port lauds ship designs that incorporate waste manage- ment equipment into techni- cal arrangements, stating that they "...provide the best pos- sible means of complying with
Annex V. This approach el- evates the mundane task of garbage handling to the same level of importance as all the other auxiliary systems con- sidered during ship construc- tion." Navy officials and ex- ecutives at Newport News
Shipbuilding (NNS) are among influential maritime agents in agreement with this conclu- sion, as evidenced by the
Westinghouse Electric Corp./
Naval Sea Systems Command $7.3 million contract for plas- tic waste processing (PWP) systems, and by an R&D pro- gram begun in early 1995 at
Newport News — Environ- mentally Compatible Product
Lines — that is assessing how ships' systems, on both commercial and military vessels, can be devel- oped for compliance with marine pollution standards.
MARPOL-lnspired Solutions Surface
According to Phil Wright, man- ager of special product sales for
Westinghouse Marine Division's
Business Development department,
Westinghouse Electric Corp.'s Au- gust 9th contract with Naval Sea
Systems Command is the culmina- tion of a four to five-year-old Navy project aimed at effectively reducing the volume of plastics on all its ves- sels. "They recognized they had a problem with waste building up on ships, and knew they had to address it," said Mr. Wright.
After examining the commercial shipping industry, Navy engineers devised plans for adapting a plastic waste processing system for instal- lation on military vessels, and then contracted with Westinghouse Ma- chinery Technology Division in Pitts- burgh, Pa., to build prototypes con- sisting of three system components: shredders; compressed-melt units; and closed loop cooling units.
Following the successful construc- tion of prototype PWP systems, the
Navy awarded two contracts for building and supplying the systems; a contract for 22 systems was given to Westinghouse Electric Systems 1) Insertion of plastic waste. 2) Shredded plastic in re- cycling bin. 3) Compres- sed-melt unit. 4) View of
PWP equipment.
Maritime Reporter/Engineering News them reduced, they take up a tre- mendously less amount of space, and (you) no longer have the prob- lem of offloading," said the
Westinghouse representative. Re- portedly, the Navy has plans for reusing the disks in different appli- cations, including in the construc- tion of pier pilings.
Equipment Design
Emphasizes Easy Adaptability
For Vessel Applications
The PWP equipment requires that only minimal retrofitting be per- formed on recipient vessels, a char- acteristic which adds to the ease of installation already incorporated in the design. Provisions for convenient maintenance of the waste manage- ment system are also inherent in the design scheme. Since the PWP equipment fits easily in a small room, and accepts every kind of plastic, including food-contaminated waste, the next important factor is cost assessment. In terms of mainte- nance costs, according to project engineers, once the equipment in- stallations are completed, which will be in two years' time, the Navy will perform all maintenance. "Sailors onboard will be able to maintain the equipment," said Mr. Wright. "The complexity was designing it and building it to fit in a small space."
Peter McGraw, plastics pro- grams engineer in the Environmen- tal Dept. of the Naval Surface War- fare Center's Carderock Division at
Annapolis, pointed out that in con- sidering expenses, space preparation costs over- ran equipment costs, although the extent of necessary retrofitting work will vary consider- ably according to the vessel or class of vessels on which the PWP sys- tems are installed. "We've designed it (PWP equipment) to fit through standard pas- sageways for easy instal- lation, without burning holes. Depending on the ship and class of ships, some will require space preps, putting up