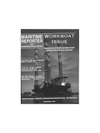
Page 61: of Maritime Reporter Magazine (November 1995)
Read this page in Pdf, Flash or Html5 edition of November 1995 Maritime Reporter Magazine
an umbilical cable into the plat- form's service center assuming direct control of all functions including the fire/water system, an important and necessary safety function while the vessel and crew are in close proximity to the drill rig. The crew reviews and moni- tors all functions, performing rou- tine maintenance and repairs before unplugging and continuing on its scheduled rounds. Both approach and deployment are accomplished without disrupting platform production activities.
Electric Drives Replace
Hydraulics
Among its many innovative fea- tures, the new vessel has all elec- tric drives, unlike the more tradi- tional hydraulic systems utilized on smaller workboats. The deci- sion to employ electric lift drives came after engineering analyses revealed a need for more than 20 tons of hydraulic fluid to operate a comparable hydraulic system, a quantity unacceptable in the envi- ronmentally-sensitive coastal waters.
The electrical system proved to be less expensive than a hydraulic system of equal performance. The 92 percent overall efficiency rating of the electrical also meant a reduction in actual installed power alloted for jacking. Finally, the built-in redundancy of the electri- cal system guarantees uninter- rupted performance in spite of multiples. The variable speed elec- tro-mechanical jacking system includes the legs, jacking gear, and control system as an integrated package supplied by Siemens and
LeTourneau. The package consists of 48 drive/motor combinations with 12 drives per leg, four on each side of the leg. The motors are con- nected via a rack and pinion sys- tem, and are equipped with fail- safe disc brakes. According to
Mike Oser, engineer for
Halliburton, over 500,000 ft. of electrical cable were installed on the Irish Sea.
Propulsion & Control
The propulsion system consists of four Aquamaster Z-drive units located near the corners of the ves- sel. The aft thrusters each deliver approximately 1,500 hp; the for- ward thrusters deliver 1,200 hp.
An integrated approach shares power between the thrusters and the jacking system. While under- way, full power is given to the thrusters. During positioning, the thrusters and jacking system run simultaneously. The jacking sys- tem, which is only lowering the legs at this point, requires only five to 10 percent of available jacking power. Sufficient power remains to operate the thrusters at full power.
Once all four legs are securely anchored in position, power is diverted from the thrusters to the jacking system to raise the hull out of the water.
In addition to the space savings, economic benefits, and system redundancy for crew safety, the all- electric system offers a measure of environmental safety not possible with hydraulic units. With the rigs positioned off of some of England's most valuable and fragile coast- line, a spill of hydraulic fluid in the volumes needed to service a vessel of this size would spell disaster for the local tourism and fishing industries, as well as Britain's highly-prized marine and nature reserves.
Deck Layout
The superstructure is located far forward to maximize the separa- tion between the wellhead and the crew's quarters. The vessel pro- vides a helideck, firefighting equip- ment, operations control and utili- ties support, as well as two heavy- lift cranes, and deck space for maintenance equipment. It fea- tures comfortable living quarters for a crew of 42 — 10 vessel opera- tors and a maximum of 32 mainte- nance specialists.
The unique leg structures and the jacking/braking system were built at LeTourneau's facility in
Longview, Texas. Siemens'plant in
Alpharetta, Ga., built the variable- speed electric drive units. The company also supplied the control panels, brake resistors, level sen- sors, switchover circuits and phase-shifting transformers. The majority of the construction work took place at Bollinger's shipyard in Louisiana, with final outfitting accomplished in Corpus Christi,
Texas. The Irish Sea Pioneer is classed and certified by the
American Bureau of Shipping (ABS). It was shipped to the U.K. in early October for final commis- sioning. The vessel will be operat- ed by Seaforth Maritime, Liverpool
Bay, England.
For more information on the compa- nies detailed in this article please ar- cle the appropriate number on the
Reader Service Card in this issue
ABS 47
Aquamaster-Rauma .48
Bollinger Shipyard 46
LeTourneau 49
Siemens ...SO
THE ARTICULAI r* I M MUM m \m0Ml
More and more, owners are moving toward pushing barges at sea — a transi-tion made possible by the applica- tion of the Articulated Tug/Barge (ATB). The ATB has provided the tug and barge industry with a ves- sel that can effectively compete with ships in two areas: speed and weather reliability. The ATB is designed to shine in both areas, and it does so without sacrificing the economic benefits of tug and barge construction and operation.
The modern ATB tug is a fully functional ocean tug, capable of towing on a hawser if required.
The ATB barge is designed so that it can work with other tugs and be towed. The difference is the con- nection between the tug and barge.
Towed barges are often weather- bound when sea states or weather along their trade route are project- ed to be risky to operation. This has been particularly true along the U.S. East Coast, where tank barges often gathered at the approach of bad weather. Delays of two to three days are not unheard of.
A firm at the forefront of ATB design has been Ocean Tug &
Barge Engineering (OT&BE).
Centra] to OT&BE's ATB concept is the use of the proprietary
Intercon connection system, of which OT&BE's principal was a co-patentor. In continuous opera- tion for more than nine years now, this system has reportedly operat- ed without need of a single discon- nection at sea due to weather. The six vessels now working with the system have operated in seas that match conditions simulated dur- ing the extensive model testing program Intercon undertook prior to construction of the first system.
Robert P. Hill, president of
OT&BE, filed this report on the progress of the ATB.
The ATB design is not a compro- mise between pushing and towing, but is touted as the most efficient design possible in pushing the barge. ATB speeds are now at more than 12 knots service speed, and with the new generation cur- rently being designed, speeds of more than 13 knots are possible.
Here are some possible benefits of the ATB, particularly with an
Intercon ATB.
Reduced bow damage to barges because the tug crew can feel excess pounding.
Reduced fender replacement (virtually none in 7 years) and tow wire replacement costs.
As much as 25 percent fuel sav- ings vs. towing.
Reduced engineering and con- struction costs vs. a tanker of equal deadweight.
More control over barge and less dock damage, emergency maneu- vers without fear of breaking wires or tripping the tug.
Higher average speeds, light and loaded.
Ship-reliable ETAs.
Ability to sail through a wider range of weather conditions.
Reduced port time/elimination of transfer time from pushing to tow- ing gear and back.
Availability of a large, high horsepower ocean tug for emer- gency and salvage work, and a means to deploy a spill boom in an accident.
All functions controlled from pilothouse.
Presently, OT&BE is providing the contract design for a 33,000- dwt ATB for Penn Maritime of
Stamford, Conn., including the design of the barge and the con- tract design of the tug based on an adaptation of OT&BE's new
Voyager class ATB tug. Penn built the first totally new Intercon ATBs in 1994-5.
OT&BE is also participating in the Crowley Maritime ATB project by providing subcontracted ATB consultation for the barge design undertaken by Elliott Bay Design
Group (Seattle). In addition,
OT&BE is providing the design for the 12,000-bhp tugs that will push the barges, with a second adapta- tion of the Voyager class tug, along with conversion engineering for a group of existing tugs. This unit is also an Intercon ATB.
OT&BE client Maritrans Inc. (Philadelphia) was the first
Intercon ATB customer and has a total of four units in service. The first, the Intrepid I Ocean 250, went into service in 1986. The lat- est, the Liberty I Maritrans 300, has a new type of Intercon system specially designed for use in ligh- tering service. It was delivered in
October.
OT&BE engineered both the barge and tug modifications to this unit, and is working with two shipyards, providing conceptual design services for Maritrans.
River/Ocean Systems has begun design of a 10,000-lt. dwt ATB bulk carrier using a contra-rotat- ing Aquamaster Z-Drive propul- sion system. The first is to be built in 1996, with major design respon- sibilities for the ATB-related engi- neering and barge hull design 62 Maritime Reporter/Engineering News