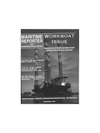
Page 66: of Maritime Reporter Magazine (November 1995)
Read this page in Pdf, Flash or Html5 edition of November 1995 Maritime Reporter Magazine
WORKBOATS effecting positive advancements in tug capability. "We are focusing on
Z-drive tugs, rather than standard screw-prop tugs," said Jim Cole, director of business development and design at Elliott Bay Design
Group, Seattle, Wash. "The prima- ry thrust is that boats have gotten more powerful due to engines with higher output." The use of high capability synthetic line is another technological advancement in the tug design area. "Now it is possi- ble to get up to 400,000 pounds breaking strength in a line han- dled by crew people," he added.
A relatively new trend in work- boat propulsion is the incorpora- tion of waterjets. Pilot boats seem destined to play the testbed role for applications of this technology in the workboat sector, due to their need for increased speed and effi- ciency in transit. According to
Captain Ward Pearce, chief port pilot for Worldport LA, the three most important characteristics of a pilot boat are speed, efficiency, and seaworthiness. Ultimately, a pilot boat "has to be designed to operate in all weather for the port intend- ed. The boat has to be designed to be seaworthy in the worst pre- dictable conditions," said Capt.
Pearce. Logically, the speed increase offered by waterjet tech- nology will add to ease of service, extending the overall performance by effecting a positive change in the level of seaworthiness.
Expressing support for another trend in the workboat sector, Jack
Hochadel, vice chairman of
Willard Marine, predicted that construction of workboats will revert back to use of composite materials for hulls. "I think that's more accepted, and a bigger factor than it used to be because of better maintenance, as well as better thermal and acoustical properties."
Mr. Cole also pointed out that improved fendering systems are being introduced to further reduce maintenance costs by preventing damage to customers' ships.
In terms of predicting market trends in the workboat sector, the technology being made available could significantly alter newbuild production. Undoubtedly, the inclusion of recent innovations in workboat newbuilds — namely, advanced electronic charting, cleaner burning engines with fail- safe mechanisms, and higher wattage lighting for patrol crafts — will contribute to the increased demand for workboats being demonstrated in the current mar- ket.
Overall, owners have to decide between contracting newbuildings, and benefiting from technological enhancements, or being content with older, yet less expensive ves- sels. According to Mr. Cole, some owners prefer the latter strategy: "Some will not take big risks, but will accept equipment that is less than what is best (for a desired function)." However, if owners
November, 1995 have specific ideas about what they need, said Mr. Hochadel, "or want some of the new technology, they'll have to have a new vessel built." As succintly put by Capt.
Ward, "When it gets to the point where costs of maintenance get too expensive ... you buy a new boat."
Another potential boost to work- boat production is the increased concerns experienced by owners over compliance with environmen- tal regulations. "Obviously, it will have the effect of creating new aspects to the workboat market," said Mr. Hochadel. Workboats not only perform oil spill response duties, but due to their high man- zeuverability, provide key ship (Continued on page 69) • AMFELS VALUE • RELIABLE SERVICE • QUALITY WORK • COST COMPETITIVENESS • AMFELS VALUE • a m --r.
OFFSHORE & PETROLEUM SPECIALISTS
Established in 1987,
AMFELS is a combination of the M !i\ii H proven and the new.
An independent subsidiary of the world's foremost builder of mobile and floating offshore exploration and production units, Far East Levingston
Shipbuilding Limited (FELS), AMFELS has the design and construction capabilities to take on the most sophisticated marine, shipbuilding and ship repair projects.
The Leader in
Shipbuilding and
Ship Repair
Located in the Port of Brownsville, the facility has a total land area of more than 150 acres, and is equipped with modern fabrication and deep water facilities, as well as two 150-ton floating cranes and several units of heavy lift equipment of up to 300 tons capacity.
AMFELS operates an ASME and
API certified facility for building process packages for onshore and offshore applications.
KMAI/AMFELS Houston Office:
Texas Commerce Bank Building 5177 Richmond Avenue, Suite 1065
Houston, Texas 77056, USA
Phone: 713/840-8811
Fax: 713/840-1198
U.S. Representative
Keppel Marine Agencies Inc.
Head Office:
Port of Brownsville
Highway 48
Brownsville, Texas 78523, USA
Phone: 210/831-8220
Fax: 210/831-6220 • aniVA S13JWV • SS3N3Allli3dWOD ISO) • MUOM AlllVflO • 3 31A d 3 S 31SVI13H • 3I11VA SUdWV •
Circle 205 on Reader Service Card 67