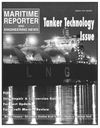
Page 57: of Maritime Reporter Magazine (March 1997)
Read this page in Pdf, Flash or Html5 edition of March 1997 Maritime Reporter Magazine
Frequently, the expected service life of a coatings system is not reached due to coatings failures.
Various parties involved (shipown- er, yard contractor, paint manufac- turer) often request TNO Institute of Industrial Technology to investi- gate the cause of such failures. An investigation begins with inspec- I tion of the damage and collection of sample materials.
Epoxy or coaltar epoxy coatings are mainly used for the conserva- | tion of water ballast tanks. High- build and solvent-free epoxies have increasingly been used to reduce health risks and for compliance with government regulations. The presence of carcinogenic tar com- j pounds in coaltar epoxies has resulted in a ban on these products in several countries. Coatings are mostly applied in one or two layers on top of a shop primer. Some important properties of coatings systems and causes of premature failing are mentioned below.
Shop primer
The shop primer is intended for a temporary protection of steel against corrosion during newbuild- ing. After primary blast cleaning of the steel, which should remove all dirt and mill scale, the shop primer is applied automatically.
Thickness control is a key factor of these automatic installations. Too low a thickness results in prema- ture rusting and extra costs for secondary pretreatment. Too high a thickness increases the risk of formation of pinholes in topcoats due to the escape of entrapped air in some porous shop primers, slows down welding operations, as well as increases the number of pores in welding seams.
Secondary pretreatment
Prior to application of the water edges. Weld spatter and steel lam- inations must be removed and welding seams made continuous to guarantee proper coverage.
Dry film thickness
Coatings systems are to be applied in closed films in the cor- ballast tank coatings, the ship primer must be cleaned properly.
Oil, fat, dirt, dust, rust, alkali weld deposits and salts must be removed. Oil and fat prevent a proper adhesion; salts attract moisture which initiates blister- ing. i^age coverage
Frequently, corrosion in ballast tanks is first observed on sharp edges. To achieve a proper coat- ings film on sharp edges, applica- tion of a stripe coat using brushes is often used. Alternative methods are chamfering or rounding of
March, 1997 rect film thickness. Coatings applied too thin give insufficient protection and will show rust and adhesion blisters more quickly. A two-coat application decreases the risk of areas with too low a thick- ness. Solvent entrapment in coat- ings layers applied too thickly can result in blistering. Excessive thickness can result in sagging of the coatings.
Ventilation
During and after application of solvent-containing coatings sys- tems, tanks need to be ventilated in order to prevent the presence of excessive amounts of solvents.
After evaporation of entrapped sol- vents in a cured coatings system, porosity may occur. Both situa- tions result in a higher water vapor permeability.
Porosity
Coatings layers should be free of pinholes. The entrapment of air in the coatings layer should be pre- vented as much as possible. In addition, the coatings system must be of such a quality that exudation of components from the coatings, i.e. tar, oils and hardener, does not occur.
Application conditions
The application conditions must be in accordance with the mini- mum requirements given in the product information sheets of the coatings. Generally, this implies that the steel surface temperature be at least three degrees above dew point. Under-roof application decreases the risk of a too-low sur- face temperature. The overcoating intervals must be complied with to ensure a good intercoat.
The application of coatings sys- tems has become an extremely specialized task. Various causes can be responsible for premature failing, requiring the execution of costly repairs. In the worst case, a completely new coatings system is necessary, at tremendous cost.
Inventories made by TNO have shown that the majority of coat- ings breakdowns are caused by 65 « I ir IvllCllllUCll uai -LICX V/l^UUV/U KJJ I Xivuuj