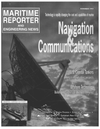
Page 76: of Maritime Reporter Magazine (November 1997)
Read this page in Pdf, Flash or Html5 edition of November 1997 Maritime Reporter Magazine
Kvaerner To Take Over Philadelphia Shipyard
Kvaerner — the international engineering and construction group — signed an agreement to develop the former U.S. Navy yard in Philadelphia, Pa., into a state- of-the-art shipbuilding facility.
The agreement is a 99-year deal under which Kvaerner would build container vessels and tanker ships at two dry docks on the Delaware River. The first ves- sel to be produced by the venture would set sail in 2000. The agree- ment was signed at Kvaerner's
Warnow shipyard near Rostock,
Germany, as Tom Ridge,
Governor of the State of
Pennsylvania, and other mem- bers of the U.S. delegation were at Kvaerner's German yard recently, to see the facilities devel- oped by the group since its acqui- sition of the former state-owned shipyard in 1992.
It is proposed that the parties will jointly develop a modern shipyard on part of the former naval facility. Extensive training programs will be implemented for the yard workforce based on
Kvaerner's technology and experi- ence.
Under the terms of a draft agreement, the Commonwealth of
Pennsylvania, the Philadelphia
Industrial Development
Corporation, the Delaware River
Port Authority and others will contribute a total of more than $400 million of investment fund- ing in the yard, of which about half will be for training.
Extensive skills training and additional on-the-job training will be funded through various U.S. programs.
For its part, Kvaerner will pro- vide capital infrastructure invest-
Bender To Build Two For
GulfMark
GulfMark Offshore has made agreements that will add six ves- sels to the company's fleet and signed charters for two vessels, including one of the new vessels.
Bender Shipbuilding & Repair
Inc. in Mobile, Ala., agreed to build two offshore support ves- sels at a cost of about $22 million, for delivery in January and June 1999. GulfMark has an option to build two additional vessels under this contract. ment of some $45 million over a five year period. Approximately $30 million of this will be provided through a loan from the
Pennsylvania parties at preferen- tial rates of interest.
The naval yard, which now serves as a mothball facility for out-of-service Navy battleships and frigates, closed as a working shipyard in 1995 with the loss of about 7,500 jobs. Kvaerner will also provide ship designs, software applications and access to its extensive R&D programs. As a measure of its commitment,
Kvaerner will purchase, at cost, the first 3 ships to be built at the new facility (totaling some $80 mil- lion). These vessels will be offered for sale to the market.
Westfalia Separator Introduces
Advanced Separator Line
Desludging System Utilizes Hydrostop System Design
Last month MR/EN provided news of the introduc- tion of the new Westfalia C-Generation product line.
The company recently released additional technical details, presented here.
Westfalia Separator has introduced a new eco- logically advanced line of separators. The key characteristic to the advancements made to the C-
Generation separators lies within the patented
Hydrostop process, which is designed to provide a more precise desludging system. In a typical marine and power application, the Westfalia sepa- rator reportedly can reduce sludge up to 50 percent during fuel oil and lube oil purification, and up to 90 percent during sludge treatment.
Hydrostop works in conjunction with redesigned discharge ports in a new bowl architecture for more efficient sludge removal, and the Softstream sys- tem, a unique process which allows liquids to enter the bowl in a super calm state. Keeping liquids in this state as they enter the bowl contributes to the increased flow rates of the new separator, as well as overall separating efficiency and reduced com- ponent wear. There are four separators in the C-
Generation product line: OSC 5, with a capacity of 4,000 1/h; OSC 15, with a capacity of 11,500 1/h;
OSC 30, rated at 24,000 1/h; and OSC 50, rated at 43,100 1/h.
Designed For Oily Water Treatment
The Softstream system of the Westfalia separa- tor is particularly important in oily water treat- ment situations found in tanker slop water, bilge water, drain water, produced water and engineer- ing liquids, according to Dierk Homborg, manag- ing director of Westfalia Separator. "Slop water, for example, is collected and taken to port where it is transferred to a specialized treatment plant, or it is dumped at sea in the few areas where this is still a legal activity," Mr. Homborg said. "The new C-
Generation separators will allow ships to efficient- ly treat onboard the slop water as well as other oily water, allowing oil-free water to be returned to the ocean." All four new models of the C-Generation are available in Unitrol design, a proprietary
Westfalia Separator development which uses a patented sludge space monitoring system (SMS) and a water content monitoring system (WMS) for optimum separation.
Solids or water that accumulates in the sludge space causes interruptions in the flow of a sens- ing liquid. These interruptions are detected by the SMS and alert the system.
The WMS monitors water content in the bowl, allowing the centrifuge to operate as a purifier and clarifier.
Low-Maintenance
In addition to the higher flow rates — including the OSC 50, a high capacity separator — and eco- logical benefits, the new C-Generation is being touted for its long maintenance intervals and low maintenance requirements.
Main service intervals are increased to every 8,000 to 16,000 hours — in line with diesel engine over- haul intervals — and bowl cleaning intervals also are extended, due to the Hydrostop system.
Tracking Separators
A new central service center in Hamburg stores data on separator operation which will be used to reference real-world situations onboard ships. In the future, Westfalia Separator centrifuges will be able to communicate directly with the software center. The center can also monitor spare parts consumption and separator water.
For more information
Circle 85 on Reader Service Card
Marine Application • Used onboard ships for the treatment of fuel oil, lube oil, sludge containing oil and water and bilge water; • Works with Unitrol, a proprietary Westfalia
Separator process that provides a water content monitoring system (WMS) and a sludge space monitoring system (SMS) for optimum separa- tion efficiency; • Designed for unsupervised operation; • Conforms to classification regulations and environmental laws.
Offshore Oil Application • Used to remove oil from produced and drain water; • Used to remove water from crude oils; • Purifies and treats fuel oil, lube oil and hydraulic oil; • User friendly, low weight and smaller size. 72-B Maritime Reporter/Engineering w-