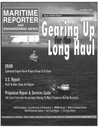
Page 54: of Maritime Reporter Magazine (October 1998)
Read this page in Pdf, Flash or Html5 edition of October 1998 Maritime Reporter Magazine
Software Solutions: CAD/CAM/CAE mined that a high level of con- struction accuracy was possible without a dramatic increase in costs.
The development of some stan- dard primary and secondary struc- tures minimized design time and increased producibility and also significantly affected another important area, the CAD model.
By having the primary structure identical for all units, the structur- al CAD modeler was able to rapid- ly create all of the structural mod- els.
Also after review of the equip- ment arrangements for several of the units the structural engineer- ing sub-team was able to recom- mend 3 basic arrangements for the secondary structure.
Safer Communications clt SCci
Computer based GMDSS and Maritime English training on CD-ROM • Individual on-board education and training + * * • Perfect refresher tool to maintain your skills * * • Tests and individual log-book included lVL3.ri.LimC -DQtlCBLlOn
P.O. Box 24135, SE-104 51 Stockholm, Sweden, Phone: +46 8-671 09 60, Fax: +46 8-783 04 00, E-Mail: [email protected]
Circle 296 on Reader Service Card
The design of the machinery units can proceed independent of the ship's structure and somewhat independent of the other machin- ery units.
The space below the secondary structure was utilized for piping.
The walkway secondary structure provided the support for the cable- ways and through unit piping.
The electrical cabling is simply laid in the trays and when the run- ning of all cables is complete the walkway plates are secured in place over the cables. The units were designed to enable the mechanic to install the majority of the equipment and piping on the secondary structure (forming a
Level 2 unit) on their workbench.
The Level 2 unit is then installed onto the Level 4 primary structure and the remaining interconnecting and through piping is installed on the Level 4 machinery unit and the unit is tested. As the majority of connections to the primary and secondary structure are mechani- cal, final painting can occur prior to Level 2 and Level 4 outfitting.
Once the level units are outfit- ted and tested, they are assembled as a grand unit and all wiring and testing that is practical is complet- ed. Since the control and monitor- ing and power distribution sys- tems are based on the distributive concept much of the local wiring is installed and tested at the inde- pendent Level 4 machinery units.
Once the grand unit is assembled the majority of testing can be com- pleted.
On SSD#3 the build strategy plan was to install the main engine, shafting, and generators during a one week period once the engine compartment was complet- ed and then loadout the Level 4 units in three lifts.
The interconnecting piping is disconnected and the electrical and control cabling is coiled back to the most convenient unit.
The forward lift is an athwartship configuration consist- ing of units 56C101, 56C201, 56P101, 56P201, 61C101, 61C201, 61P101, 61P201, and 61C001.
As the distributive electrical and control and monitoring sys- tems are designed with this con- struction step considered, the amount of such cabling is minimal.
The yellow cabinets are the three primary power supply centers for the forward ten units.
Hence there are only three 03824
Tel: 603-868-3344
Fax: 603-868-3366
IMSA
FlagShip from Proteus Engineering
FlagShip is a complete ship design system, including hullform design (FastSbip), structural design and opti- mization (MAESTRO), stabili- ty, powering, maneuvering, seakeeping, ship- yard cost estimating and interfaces to CAD and ship production programs. FlagShip is based on Ume-tested, best-in-class applications, which are in use by more than 1,000 designers in over 30 countries around the world.
General Hydrostatics (GHS) from Creative Systems, Inc.
Widely recognized as the most advanced and produc- tive trim/stability/strength software. Specialized ver- sions are available for ship operators, for salvage engineers and for small craft designers. Includes efficient modeling for all types of complex vessels, and the abili- ty to analyze them both afloat and aground.
NavCad from HydroComp, Inc.
NavCad offers an integrated platform to predict resistance and power, and to determine optimum propeller parame- ters. With NavCad each aspect of a ship's performance can be evalu- ated for virtually every type of displacement hull, semi-displacement and planing craft, river barge train, catamaran and auxiliary- powered sailboat.
ShipCAM97 / CAD-Link97
NC-Pyros97 from Albacore Research Ltd.
Integrated ship production for Win95/NT. ShipCAM97:
Fairing and lofting including frames with cutouts, plate expansion, shell expansion and inv. bending. CAD-Link97: AutoCAD 13 based 3D structural modeling as easy as 2D drafting plus weight & CG. NC-Pyros97: NC- code generation from CAD drawings.
A cooperative association of software developers with complementary marine design products. 13 J
Circle 264 on Reader Service Card