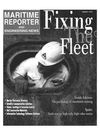
Page 44: of Maritime Reporter Magazine (March 1999)
Read this page in Pdf, Flash or Html5 edition of March 1999 Maritime Reporter Magazine
HULL CONSTRUCTION MATERIALS
One USCG inspector noted in his log that "every weld defect known was common- place and rampant"
A Avondale
Shipyards Division
Caveat Emptor
Boat buyers in the current depressed uation was well-known Alaska excur- market need to be aware of shady oper- sion vessel operator Brad Phillips, ators that might not be able to deliver all At the start of 1997, Phillips contract- they claim. One recent victim of this sit- ed for a new $4.2 million all-aluminum catamaran, hoping to have the boat ready by the Alaska summer season. The man Phillips approached to build the boat, Dan Johnston, appeared to have the right qualifications and a new trick for aluminum welding that might save some money. In the end, Phillips lost his money and saw his boat cut up for scrap because the welding failed.
According to Phillips, Dan Johnston headed up a company called Falcon
Marine at Port Townsend, Wash.
Johnston claimed to have a "patented high-speed welding process" that could be used to build aluminum vessels "faster, better, and cheaper than any other boatbuilder."
The boast seemed plausible. Johnston had already turned out a 52-ft. alu- minum speedboat for Florida owners and had a large building hall available for new construction. Caught up by
Johnston's claims, Phillips signed on the dotted line and in early 1997, construc- tion began on what was to be called
Klondike Express, a 420-passenger, 38- knot catamaran.
Johnston told Phillips the boat would be in the water by May — a remarkably short construction time. The vessel started to come together quickly, with the twin hulls fabricated in an upside down position, but even in the early stages of construction it suffered from welding problems.
Circle 243 on Reader Service Card
Buckled deck plating was easily noticeable by visitors, and Johnston's "patented welding process" never seemed to come together. Most of the welding — in fact — was being per- formed by unqualified and uncertified welders, said Phillips.
Later, it was even disclosed the fore- man of Falcon's fabrication department had little to no knowledge of either welding or boatbuilding. When U.S.
Coast Guard (USCG) teams began certi- fication inspections, they were shocked by the boat's condition and the manner in which it was being assembled.
There were no approved plans on site and construction apparently started without even minimal plan approval.
One USCG inspector noted in his log that "every weld defect known was commonplace and rampant; longitudi- nal and crater cracks, inadequate pene- tration, undercuts, incorrect weld size and shape, poor fit-up, and generally sloppy workmanship."
As time progressed, the USCG found inspection of the project increasingly difficult because there was never a set of approved construction plans available, nor had Johnston established a quality 46 Maritime Reporter/Engineering News
Avondale Industries, Inc. Shipyards Division
Repair Services
Repair Services that are available at
Avondale Include: • Shafting, Propellers and Rudders • Rubber Lining and Fiberglassing • Offshore Vessels • Structural Replacement/Repairs • Machinery Overhaul and Repairs • Pollution Control Devices • Inert Gas Installations • Ship Conversions and Jumboizing • Thruster Installations • Electronics Upgrading • Quarters Modification • Voyage Repairs; Barge Repairs • Re-Powering • Gas Freeing; Re-Coating
Drydocks Available Are: • One 82,300 MT Dock - can lift ships up to 379M long and 61.9M wide • One 20,000 MT Panamax Dock - can lift ships up to 235M long and 32.2M wide
Heavy Lift Services: • A 200-ton Gantry Crane • A 628-ton Floating Crane Barge
Fully-Staffed Engineering Department
AVONDALE INDUSTRIES, INC.
SHIPYARDS DIVISION
POST OFFICE BOX 50280
NEW ORLEANS, LA. 70150-0280 •
PHONE: (504) 436-5274
FAX: (504) 436-5280
Avondale's 82,300 MT Drydock
Avondale's 20,000 MT Drydock