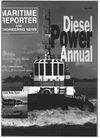
Page 52: of Maritime Reporter Magazine (July 1999)
Read this page in Pdf, Flash or Html5 edition of July 1999 Maritime Reporter Magazine
CAD/CAM/CAE
Mapping The Future Of Design
The advent of software solutions has infiltrated nearly every sector of the maritime market — from propul- sion performance monitoring pack- ages to personnel. It arguably has had no greater impact, though, than in the design and construction of new vessels.
CAD/CAM/CAE programs are invaluable assets to the designer, builder and operator of vessels of all sizes and dimensions. Not only do advanced programs allow for the cre- ation of an efficient and cost effective ship structure and outfitting, they pro- vide for enhanced manufacturing practices and techniques, and increas- ingly help devise a life-cycle mainte- nance and care plan which can tack profitable years onto a vessel's life. f 1» >»
While major providers of CAD/CAM/CAE solutions and users have struggled to arrive at common ground regard- ing interaction among different maker's sys- tems, there is today a greater cooperation to ensure that one particu- lar brand or another can interact. This mandate for commonality should surely pick up momen- tum as shipyards of all sizes in all geographic regions continue to merge with, or purchase one another. The driving force behind the consolidations is of course profitability, which in the manufac- turing arena — particularly ship- building, where prices have generally been stagnant — equates to greater manufacturing efficiency. Thus, it would be reasonable to assume that shipyards would want one of their greatest efficiency tools —
CAD/CAM/CAE systems — to be somewhat compatible.
While CAD/CAM products are par- ticularly effective in designing every- thing from components to systems to entire vessels, the trends is toward comprehensive systems that allows ship designers, builders and owners to integrate design, trial and "cost crunch" a vessel before steel is even purchased. According to Markku
Kanerva, director of marketing, pro- jects and R&D at Finnish Delta- marin, the ship design and building process is in front of revolutionary era of development. 3-D computer aided modeling techniques has been utilized to produce the production drawings and documents. Kanerva says that Deltamarin developed the first 3-D engine room model already in 1987 and since that time, close to fifty design models have been devel- oped.
Deltamarin today — via strategic alliances such as that with which
IBM and Dassault Systems in the use of its innovative CATIA program — the 3-D design models are changed into 4-D Product Models.
Complete model of the ship is already developed at the first outline project stage. This model contains all neces- sary data to visualize the product, to produce exact drawings and docu- ments, all decks and spaces fit, to simulate important functions aboard — cargo handling, passenger flow, services, etc. — to produce exact data for cost estimations and for supplier inquiries, to navigate inside the ship, and at the end of the process to pro- duce exact contract model which is directly suitable for further develop- ment without time consuming basic design.
The 4-D Product Model is designed to be used by the owner for market- ing, for simulations, for training, for safety purposes, etc. already at pro- ject stage. Navigation and ship han- dling simulations can be carried out with the actual ship model already at the project stage.
Building procedures, block subdivi- sion, subcontracting, all can be simu- lated, visualized and tested with the 4-D Product Model even before the shipbuilding contract is signed.
Building process can be verified with a virtual shipyard model, i.e. combin- ing 4-D Product Model of the ship with a simulation model of the ship- yard. Complete design work is, of course, carried out in the same Prod- uct Model continuing from the con- tract model directly with all systems, arrangements, structures and other essential features in 3-D and getting approvals directly in/with the model.
This means that the product, the ship, is already defined and coordi- nated up to a high level of details at the project stage, before the shipbuilding con- tract, and without any extra costs. But the basic design phase, i.e. classification doc- uments, layouts, pur- chase specifications and similar, is devel- oped three to five months quicker and a lot of coordination man-hours are saved.
Kanerva contends that the Product
Model technique will push the standardiza- tion forward and will introduce a major cost saving impact in shipbuilding.
Recent Introductions
There have been many recent advances in the field of
CAD/CAM/CAE systems this year alone, including the introduction by
Korea's Hyundai of its "Hyundai
Integrated Ship Performance Evalua- tion & Design System." The shipyard reasons that initial design is crucial in maintaining a shipyard's technologi- cal and competitive edges. Particu- larly, hull form and propeller design technology are of interest to shipown- ers and operators, two groups which continually seek advantages in fuel efficiency. The Hyundai "Hi Speeds" system — under development for two years — is designed to integrate all of the process of hull form and pro-
Germanischer Lloyd is leading a charge regarding structural stability of Passenger ships.
Pictured above are 3-D finite element computer mod- els, used to calculate the global strength and vibration response.
Pictured below are samples from the load computa- tions with instantaneous positions of a ship advancing at a give speed in regular headwaves.
TIME STEP 18 OF 30
TIME STEP 5 Of 30 TIME STEP 20 OF 30
TIME STEP 8 OF 30
TIME STEP 'OOF 30
TIME STEP 33 OF 30
TIME STEP 25 Of 30
TIW STEP 13 OF 30
Time step i sof x
TME STEP 28 OF 30
TIME STEP 30 OF 30 •BggSSIMI^^
Hyundai's new high-speed "Hyundai Integrated Ship Per- formance Evaluation & Design System." 52 Maritime Reporter/Engineering News
Finite Element Model .NORWEGIAN SKY' - NCI. built at Llovd Werft