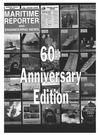
Page 70: of Maritime Reporter Magazine (October 1999)
Read this page in Pdf, Flash or Html5 edition of October 1999 Maritime Reporter Magazine
L.F. GAUBERT & CO. INC. 50 Years In Business!
P.O. BOX 50500 • NEW ORLEANS, LA • 70150
Phone: (504)822-7272 Fax: (504)821 -9309 1 -800-831 -7534 Call Us For Your FREE Newsletter
DISTRIBUTE & MANUFACTURE ELECTRICAL SHIPBOARD CABLES
NAVY-COMMERCIAL-CONTROL
ELECTRONIC-PORTABLE
COMMUNICATION-SIGNAL-MINING
WELDING-COAXIAL & POWER
CABLES-FABRICATE ELECTRICAL CABLES
TO YOUR SPECIFICATIONS
Quality Is Our MOST Important Feature!
Circle 259 on Reader Service Card
The l. t: in Maritime
Communications
Maritime
Telecommumcations
Network
The Leading Provider of
Passenger and Crew
Telecommunications.
On 9 Major Cruise Lines and Over 50 Ships.
Provider of Both Voice & the
High Data Kate Required for
Offshore Drilling Operations.
The Leading Provider of
OBand Networks for
U.S. Navy Vessels.
MARITIME TELECOMMUNICATIONS NETWORK 305.599.9434 • 800.799.2411
Vessel Maintenance Products & Systems
Getting To Where The Gouges Reside nance projects as Kaye E. Barker pulled into its dock in Duluth. In anticipation of the cylinder problem, Interlake got together with Metal Surgery, a world- wide repair specialist to discuss strategy for re-plating the cylinder. "We went into this project thinking we would need to pull the cylinder off the ship to do the re-plating," recalls Barker. "After all, these cylinders are 60 ft. above the main deck."
Running the numbers on detaching the cylinder, Metal Surgery concluded they could cut costs by setting up at the site of the cylinder. And based upon their experience with past brush plating pro- jects, they felt no problem. Exposing a repair crew to a typical Duluth winter presented a major challenge. Consider- ing the need to pre-heat the cylinder for plating and the working location, the repair crew was facing finger-numbing sub-zero weather and high velocity winds accelerated by the height of the work. So instead of taking the cylinder into the shop, Metal Surgery built a shop around the cylinder. In about a week the
The Pitting lufting cylinder used for off-loading
Kaye E. Barker, a Great Lake ore carrier need- ed repair, but was located 60 ft. (18.2 m) above the deck.
The crew of the Great Lakes ore carri- er Kaye E. Barker had enough. They had just finished up another season of deal- ing with leaks from the heavy-duty luft- ing cylinder that powered the ship's off- loading boom. So far, they were only able to bandage the problem. Each pass- ing year meant another set of replace- ment seals. Yet several months into the new season, hydraulic oil drips dotted the deck beneath the cylinder. Manage- ment at Interlake Steamship Company, the owner of Kaye E. Barker, wanted the next fix to be the last one for some time. "You add up the problems we had with this cylinder," notes Mark Barker, Fleet
Engineer with Interlake, "and you get an on-going repair nuisance." "Top it off, the leading hydraulic oil is a safety and environmental hazard."
The job of this massive one-foot diam- eter cylinder is to elevate the 250-ft. (76.2 m) boom so that the vessel may self-discharge its cargo to shore. Stress- es created by the load and the unforgiv- ing environment took its toll on the ram.
Gradually the chrome was flaking away from the surface of the ram — the visi- ble flaking and deterioration evidencing the chrome breakdown. Within time, gouges as deep as .5-in. formed along the surface, chewing up every set of seals applied to the ram and leading to the annoying leaking problem. "In addition to the other hassles," points out Barker, "the progressive leak- ing made our ability to hold pressure in the cylinder difficult." "During off-loading we had to careful- ly watch the cylinder to make sure that it did not extend causing the unloading boom to drop and inch or two."
Like all ships during winter lay-up, plans were made for a variety of mainte-
Copper areas are hand finished and then flashed with nickel tungsten.
The cylinder is restored to factory specs with no disassembly from its mountings required. crew set to work erecting scaffolding and building a heated house to enclose the cylinder and shelter the crew while providing sufficient working room.
The crew spent roughly another week applying copper plating to the damaged areas of the cylinder. Brush plating builds up worn parts to their original specifications by bonding applied metal to the parent metal at the molecular level. Based upon their involvement with a number of critical specialty pro- jects, Metal Surgery has developed tech- niques to bring this process into the field. Metal Surgery developed water cooled anodes for controlled applicatioi of the plating. This approach stops over heating of the deposited material to pre vent its degradation.
The brush plating process progressive ly restored the plating on the cylind( ram, and once plating was complete the copper areas were hand finished contour. Finally, the surface was flash( with nickel tungsten to acquire hardne and corrosion resistance to its origin specifications.
The following week was spent dis< sembling the housing and scaffold.
L J Circle 274 on Reader Service Card
Circle 245 on Reader Service Card