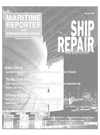
Page 53: of Maritime Reporter Magazine (March 2000)
Read this page in Pdf, Flash or Html5 edition of March 2000 Maritime Reporter Magazine
to perform the necessary changes required to implement such a system.
Prior to the purchase of Oracle ERP applications software, the company embarked on an extensive selection process designed to match the compa- ny's needs and requirements for a com- prehensive system to the functionality of individual ERP systems. Due to the time constraints involved in implement- ing an ERP package prior to the compa- ny's Y2K deadlines, the company hired
Arthur Andersen LLP as an outside con- sultant to assist in the selection and implementation process. In gathering input for the final selection process,
Bollinger gave every functional area the opportunity to prioritize their specific requirements of the new system.
The unique business environment of marine construction presents many and diverse informational needs, the collec- tive industry in the U.S. is hardly large enough to garner cost effective, industry specific solutions. In evaluating the ERP packages, however, it became apparent that Oracle's product was best suited for
Bollinger's needs. According to the company, no system was a 100 percent fit. But it noted that the Oracle system met its 80 percent matching goal.
Once the system was selected, the question of cost came next. And although the cost of implementing the
Oracle system was steep at an estimated $2.5 million, Bollinger reasoned that the cost of not having the system was even greater. According to the company, the cost of implementing the system became much more justifiable when it was realized that there will be an antici- pated annual savings (both direct and indirect) of between $750,000 and $1 million, with purchasing and material handling leading the pack at an estimat- ed annual savings of $600,000 per year.
Other anticipated savings include: administration and processing = $250k/yr.; inventory carrying cost = $100k/yr.; and "other" = $50k/yr. ous. The cost to produce and process
P.O.'s, pick lists, requisitions, invoices,
A/P checks, payroll, HR requests and other functions will decrease substan- tially. Project managers will have more accurate and timely information to make crucial real time decisions on the shop floor. Estimators will have more task level information and history to assist them in projecting the cost of building vessels. Schedulers and shop floor managers will have automated maps of material and manpower requirements, thus increasing labor efficiency. Inven- tory will be much more accurate and visible through the system. Purchasing will have the advantage of a master parts list encompassing all of the company's divisions. This will facilitate the com- pany's centralized purchasing initiative and allow Bollinger to capitalize on the buying power of its combined divisions.
All levels of management will have more accurate and detailed financial/operational information to assist in running the business as well as planning for the future.
For more information on Bollinger:
Circle 109 on Reader Service Card
For more information on Oracle:
Circle 110 on Reader Service Card "THE DESIGN OF A SHIP REQUIRES
THE HARMONIOUS EFFORTS OF NO LESS
THAN 10 DIFFERENT DISCIPLINES." "OF COURSE, IT STILL NEEDS TO FLOAT."
The integrated solution
The full suite of products installed includes Manufacturing, Projects, Pro- ject Manufacturing, Purchasing, Inven- tory, HR/Payroll, Financials and MRP.
All are designed to enable the company to have all of its information under one database/suite of products and shared throughout all of the divisions. In addi- tion, Oracle's software is browser based and designed to operate over the Inter- net, which will reduce maintenance costs of the system. All updates, upgrades, system changes, maintenance and end user changes are made locally on the centralized server.
Once fully operational (at press time the company was still tweaking the sys- tem to its own specific needs) the effi- ciencies and cost savings will be numer-
Only FlagShip'," the most complete, integrated suite of ship design and construction software, allows you to evaluate the impact of every design decision on the performance and cost of the ship. FlagShip modules for hull design, resistance and powering, stability and hydrostatics, structural design, seakeeping and maneuvering performance, weight estimating, cost estimating, and detailed structures and piping design work together to give you the complete picture, from concept design through manufacturing. Call +1-410-643-7496, fax +1-410-643-7535, log onto our interactive website at www.proteusengineering.com or e-mail us at [email protected].
PROTEUS
March, 2000 Circle 249 on Reader Service Card 53