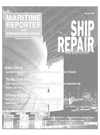
Page 63: of Maritime Reporter Magazine (March 2000)
Read this page in Pdf, Flash or Html5 edition of March 2000 Maritime Reporter Magazine
Ship Repair & Conversion (continued)
USN Reduces Shipboard
Planned Maintenance (continued from page 20)
NAVSEA implemented SURFMER across the entire Navy surface fleet.
Beginning in October 1996,
SURFMER engineers began a systemat- ic review of all scheduled maintenance requirements. Instead of performing reviews on a ship-by-ship basis as was done with the Yorktown pilot project,
NAVSEA implemented SURFMER sys- tem-by-system, applying the resulting revamped maintenance procedures fleet-wide. Typically, SURFMER reviews are conducted on site, at Navy in-service engineering activities such as the Naval Surface Warfare Center detachment in Philadelphia.
In addition to application of a repeat- able engineered process, SURFMER's success depends upon close teamwork between NAVSEA and AMS RCM
Backfit trainers and mentors, Navy in- service engineers, and fleet sailors with current deckplate operating experience.
These three groups work together dur- ing an intensive week-long SURFMER cycle to gain proficiency in the RCM
Backfit methodology. Two days of
RCM Backfit training is followed by three days of analysis of specific main- tenance requirements for systems under review. At the end of the week, Navy engineers submit their changes to the
Navy's PMS system for implementation in the fleet. Revisions are entered into the PMS management information sys- tem and distributed periodically to fleet units via CD-ROM by Fleet Technical
Support Centers in Norfolk, Va. and San
Diego Calif.
To date, 27 SURFMER Cycles have been completed. The most recent being
Cycle 27, which occurred the week of
February 7, at the Naval Surface War- fare Center detachment in Philadelphia.
Systems reviewed during Cycle 27 included distilling plants (flash type), mooring and towing gear, electrical gear, shop equipment, SONAR domes, waste heat boilers, and boat handling gear.
SURFMER has allowed sailors more time to perform truly necessary mainte- nance, and while having more free time to spend on liberty while deployed and with loved ones while in homeport.
MR1 Margaret Buffa, an MR (machinery repair petty officer) from
USS Gunston Hall (LSD-44), a Cycle 27 participant said, "I'm the only MR on my ship right now and have to do a lot of maintenance. I love the maintenance workload reduction I've seen from
SURFMER. It has made my life easier, and the equipment still works just as
March, 2000 well." Time savings achieved by
SURFMER to date exceed 2.3 million man-hours per year, (see chart on page 20) In addition to the time savings, asso- ciated maintenance-related consumable (e.g., oils, greases, solvents, rags, etc.) and HAZMAT disposal costs have been significantly reduced as well.
The bottom line: SURFMER achieves real, measurable results, with tangible benefits to fleet sailors. SURFMER, by its nature, is a continuous improvement process — systems originally reviewed in 1996-1997 are being revisited in cur- rent cycles. The revisits sometimes yield more reductions, by percentage, than the first time around as Navy engi- neers become more proficient in the process and more confident in the results. The next step is to institutional- ize the SURFMER methodology across the Navy's engineering community, so that it becomes the everyday way of conducting business.
Ariana Baseman is a freelance writer based in Silver Spring, MD
Circle 287 on Reader Service Card 63
ISO 9 O O 1 CERT!, g^yfe, Q « .. ^ I
Tranter, inc. Texas Division P.O. Box 2989 Wichita Falls, Texas 76307 (040) 723-7125 Fax: (940) 723-5131 http://www.tranter.com/rn A E-mail: [email protected]
Tranters On Board...
In PHE Applications From
Bow To Stern!
You find Tranters plate heat exchangers everywhere on the high seas and inland waterways—on Naval and Coast Guard ships, fleet oilers, commercial containerships, tankers, oceangoing tugs, buoy tenders and offshore drilling vessels.
We've never been high on blowing our own bosun's whistle about our unsurpassed plate-type heat exchanger technology, but plenty of ship owners, builders and opera- tors can signal you how they have lowered costs and increased the productivity of their vessels with our
SUPERCHANGER® plate and frame, PLATECOIL® prime surface and MAXCHANGER® all-welded plate heat exchangers.
For over 20 years, we've been supplying marine heat exchangers in full compliance with codes and specifications as required by the ABS; the
U.S. Coast Guard; shock testing per MIL-S- 901D; vibration testing per MIL-STD-167-1; dynamic load calculations for ship motion; and ASME U stamp per Sec. VIII Div. 1.
Discover how efficient your on board heat transfer can be. Call, fax or e-mail us today, or visit our website. Ask for our TIS-108A technical bulletin of marine annlirannns. or arrange a