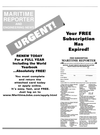
Page 51: of Maritime Reporter Magazine (December 2000)
Read this page in Pdf, Flash or Html5 edition of December 2000 Maritime Reporter Magazine
on a project in a small yard.
CAD Tools in the Small Shipyard
Small shipyards in the U.S. typically implement computer-aided technology on an incremental basis. From the authors' experience, these yards are far behind their European and Far Eastern competitors in the extent to which such technology (and associated production processes) are put into use. Typically, small yards may have some or all of the following computer tools: Word pro- cessing (Word); Spreadsheet (Excel);
CAD (usually 2D)(AutoCAD); NC cut- ting machine software; Engineering pro- grams (FastShip for hull design, HecS-
DS). Sometimes, data can be transferred between programs. However, each pro- gram is usually a separate, self-con- tained entity with its own database, graphical user interface, software code, and operating procedures.
Unlike 3-D product modeling systems, the above example programs support traditional shipyard processes. The 3-D product model systems can support tra- ditional processes, but their real value comes only when they are used in con- junction with modern shipbuilding
The rules have changed. Today's shipbuilders must respond, collaborate, and launch products faster than ever before. That means engineers need tools to help them create innovative designs faster, work more closely with partners, and manage data throughout the full product life cycle.
To meet these challenges, PTC has created
Pro/ENGINEER' Shipbuilding Solutions | a suite of new design and engineering tools focused on the unique needs of the shipbuilding industry. These solutions are brought to you by PTC, the company that developed |CADDS' 5i and Windchiil - the leading Internet-based collaborative product commerce (CPC) solution. Pro/ENGINEER®
Shipbuilding Solutions enable engineers to create more innovative designs and be more productive. With PTC, playing by the new rules is easier than ever.
To learn more about PTC's solutions for shipbuilding call 1- 888-PTC-3776 (within North America) or
PTC*
Shaping Innovation
Circle 255 on Reader Service Card processes. Three example shipyards pro- vide compelling evidence of the great advantages that can come from upgrad- ing to 3-D product modeling. All three yards are privately owned and are locat- ed in the north of Spain. Table 1 pro- vides information describing the yards, and all tables (on page 47), present overviews of the facilities. All the yards design a wide range of vessels, typically including merchant ships, fishing ves- sels, tugs, and offshore supply vessels.
Prior to adopting 3-D product modeling, the yards used CAD or manual drafting and full scale or 1:10 scale lofting. Lit- tle design information flowed to the workshops, and outfitting was carried out on board the ship. The yards adopt- ed 3-D product modeling, along with improved production processes and upgraded facilities, in steps, as shown in
Table 2. The savings in materials and production labor costs, and reduction in schedule are quite astounding, ranging from a savings of 20 to 25 percent in terms of material cost; 30 to 35 percent in terms of production/labor cost; and a 30 to 50 percent savings in hours spent on design. The results are presented in
Table 3.
In addition to the savings shown in this table, all yards reported improve- ment in the quality of production work.
The main reasons for these improve- ments were more and better information provided to the shops, a drastic reduc- tion of design errors during production, just-in-time information to the shops, pre-outfitting of steel blocks, improved accuracy of materials estimates, earlier availability of bill of materials, automat- ic generation of information for NC cut- ting and pipe bending machines, and information available to the planning department. Materials cost savings were realized because of less production rework, less material wastage in steel lofting, less need for piping margin, and shorter piping routes.
It is relatively clear that small ship- yards using 3-D product modeling have improved production quality and have realized significant savings in materials cost, labor cost, construction time, and labor hours. While design staff training is straightforward, it may be problemat- ic if the entire staff is trained simultane- ously. The end result, however, is design staff proficiency in product modeling is attained by the end of the design of the first vessel (a modest level of technical assistance by the 3-D product modeling supplier is helpful during this first design).
About the Author
Jonathan M. Ross, P.E., is Director of Engi- neering at Proteus Engineering in
Stevensville, MD. He is the North American representative of SENER, Ingenieria y Sis- temas, S.A., the developers of the FORAN
CAD/CAE/CAM system.
New Rules
New Tools 48 Maritime Reporter/Engineering News