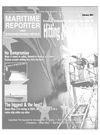
Page 17: of Maritime Reporter Magazine (February 2001)
Read this page in Pdf, Flash or Html5 edition of February 2001 Maritime Reporter Magazine
News
Cummins and learned of the company's commitment to lowered emissions under the year 2000 IMO regulations.
He met with Cummins West's territory sales manager Tom O'Conner and decided to replace the exiting 600 hp engines with a pair of Cummins KTA19
M3 with continuous duty ratings of 600 hp. Doing all of the work at their own dock, the eight month project saw the engine room completely stripped of plumbing and wiring, sandblasted and repainted. The old engines and gear came out to be replaced with the new
Cummins coupled to Twin Disc 5202 deep case gears with 5:1 ratios and turn- ing Sound Propeller's 60 x 47-in. work wheels. At the same time, gensets and steering were replaced, although the original four flanking and two steering rudders were retained. The galley and wheel house were completely redone.
Even the lazarette got sandblasted and coated with 90 gallons of new paint. "People can't believe the difference when they see the engine room, they want to know what we are going to do with all the space," says Aaron, "The old engines, which we will destroy under the program, weighed 12,000 lbs. each.
The new engines weigh only 4,000 lbs. each. We gained 10 in. of freeboard which helps coming up the river as we have to work the tides."
Aaron is equally enthused by the per- formance of the virtually new boat. "The old engines took 85 gallons of lube oil in the crank case and burned 10 gal- lons on a 24 hour round trip to the south bay with 14 hours at max and the rest idling and jockeying.
The new engines have 10 gallons of lube oil in the base and burn no oil on the same trip. The old engines each burned 35 gallons per hour while the new ones burn only about 29 gallons per hour."
The people who oversee the Carl
Moyer Program are equally impressed and have declared the boat to be the most successful project in the Bay Area
Air Quality District. While the program didn't cover all of the costs of the refit, their grant contribution equaled the cost of the engines excluding the gears.
Aaron, who at 28 years of age and has had his masters ticket for eight years, explains that he took a special and per- sonal interest in the project to honor his younger brother Trig, who died in an automobile accident just over a year ago.
In a further recognition the boat, for- merly named Jerico Spirit will be renamed the Trig Lind at a rededication ceremony, once the boat has completed all of the sea trials.
Circle 41 on Reader Service Card
February, 2001
Bender Shipbuilding To
Construct Oil Barge
Bender Shipbuilding & Repair of
Mobile, Ala., has been selected to build a 150 x 60 ft. (45.7 x 18.2 m), 10,000
BBL capacity Well Test Barge for The
Hanover Company of Houston, Texas.
The barge, which will be built accord- ing to ABS class standards for interna- tional service, is scheduled to be com- plete in four months.
It will be equipped with pumping, generator and separation systems to per- form its well test mission.
Circle 26 on Reader Service Card
A b DOVER) DIVERSIFIED COMPANY
Alabama Shipyard Signs
Another Tug/Barge Contract
Alabama Shipyard has signed a con- tract to build an articulated tug and barge (ATB) vessel for Allied Trans- portation Company of Norfolk, Va. Both vessels will be designed and built to
Tranter PHE, Inc. • RO. Box 2289 • Wichita Falls, TX 76307 a (940) 723-7125 a Fax: [940) 723-5131 http://www.tranter.com/rn • E-mail: [email protected] 650437 ©2001 Tranter, inc.
WWW.maritimetOday.com Circle 272 on Reader Service Card 17
PLATE E X C H A N G E R S
Got Any Ideas
For Better
Heat Transfer
Efficiency?
A
It-
Y_
WE DO!
If you haven't been asked this question lately, it's a certainty you will be, and soon. •n virtually every marine vessel, there are opportunities to improve effi- ciency through more effective heat transfer, if you know how and where to look. Tranter's application engineers have looked for over 20 years, and have engineered a variety of solutions which have enabled ship owners, builders and operators to lower costs and to increase the productivity of their vessels. They've done it with plate-type heat exchangers. •ur SUPERCHANGER® plate and frame heat exchangers operate at a 1-2°F temperature approach, compared with a shell and tube's 8- 10°, and with 3 to 5 times greater U values! •ur PLATECOIL® prime surface units can be engineered and designed in any way, shape or form to improve heat transfer efficiency, while our MAX-
CHANGER® all-welded plate heat exchangers are especially effective where space is at a premium or gasket limitations prevent the use of a SUPER-
CHANGER.
From heating main engine jacket water to cooling water/glycol solutions for electronic gear cooling, to plastic waste disposal and numerous other suc- cessful heating and cooling applications, Tranter heat exchangers are pro- viding optimum efficiency in heat transfer.
Need better ideas for efficiency in your on board heat transfer? We've got 'em!
Contact us. We'll send you our latest Marine Applications Bulletin chock full of heating and cooling details, along with our company CD. Next time some- one asks if you have any ideas for greater efficiency, you'll be able to say, "I certainly do!"
TRANTER