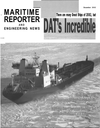
Page 22: of Maritime Reporter Magazine (December 2002)
Read this page in Pdf, Flash or Html5 edition of December 2002 Maritime Reporter Magazine
Coatings & Corrosion Control (1) the "safe" removal, treatment, and disposal of "spent" marine antifouling paints (coatings) deemed "harmful" by the Treaty to also "protect the marine environment", and (2) who is liable for the future costs of dredging and dispos- al of TBT-contaminated port and harbor sediments dredged materials.
The requirement for "safe" removal and disposal was subsequently incorpo- rated at MEPC 46 as Article 5 in the
Treaty, without it shipyards complying with existing national and local dis- charge regulations (most have none for the discharge of TBT) could inadver- tently release more TBT to ports and harbors in the five-year compliance period than has been leached from ships (hulls) in the past 40 years to the same waters. A future concern of ports and harbors may be the liability for costs associated with the treatment and dis- posal of dredged sediments that are con- taminated with TBT, which has not been addressed.
Treatment of TBT
Contaminated Waste
Over the past four years, the U.S.
Environment Protection Agency (EPA) — has funded several projects to devel- op and test wastewater treatment tech- nologies to the Center for Applied Ship
Repair and Maintenance (CASRM) and
Old Dominion University in Virginia.
These studies have found that wash- down (salt removal) and hydroblast (paint removal) wastewaters in ship- yards can contain up to six million parts per trillion TBT. In Virginia, this waste- water is treated to remove TBT from shipyard discharges. Researchers at Old
Dominion University have demonstrat- ed that off-the-shelf waste treatment technologies were not satisfactory for the treatment and removal of TBT in these wastewaters. In addition, U.S.,
Australian, U.K. and Swiss studies to remove TBT and other metals from wastewaters have found that advanced technologies not commonly utilized in normal sanitary treatment plants are required to remove TBT.
Studies conducted by EPA, U.S. Navy,
UK DOE and the Consortium of Organ- otin Manufacturers Association (ORTEPA) have recorded declining lev- els of TBT worldwide, yet documented 'hot spots' of TBT in bottom sediments in the proximity of shipyards, drydocks, marina's, ports and harbors.
Costs
An example of how contamination can increase the costs for disposal of dredged material is seen in the two alter- natives available to the Port of NY/NJ.
The Mud Dumpsite, located three miles offshore, has been operational for many decades and has been the traditional dis- posal area that can accept clean dredged materials. Contaminated "spoils" have to be disposed of at an upland hazardous waste disposal facility. From 1977 to 1991, 90 percent of all NY/NJ dredge spoils were tested and classified, as clean spoils and only one to two percent were contaminated spoils. However, in 1991 the U.S. EPA required bioassay testing. This increased the volume of contaminated spoils.
For contaminated dredged material, the currently available alternative is upland disposal at a hazardous materials storage facility and none are available in the near vicinity. Howland Hook Termi- nal in Staten Island shipped 150,000 cu. yd. of sediment via barge and rail to
Utah at a cost of $17 million or over $110/ cu. yd. Traditional fees for dump- ing dredge materials at the Mud Dump- site at this time were in the area of $10/ cu. yd.
Therefore, concern was expressed over the need to identify regulatory lan- guage within the Treaty itself for the
Provisions, Specific Requirements and the Adopted Resolutions of the Adopted Resolutions
Treaty Specific Requirements: • Under the terms of the new Convention, Parties to ihe Convention are required to prohibit and/or restrict the use of harmful anti fouling systems on ships flying their flag, as well as ships not entitled to fly their flag but which operate under their authority and all ships that enter a port, shipyard or offshore terminal of a Party. • Ships of more than 400 gt and above engaged in international voyages (excluding fixed or floating platforms, FSUs and FPSOs) will be required to under- go an initial survey before the ship is put into service or before the International
Anti-fouling System Certificate is issued for the first time; and a survey when the anti-fouling systems are changed or replaced. • Ships of 79 ft. (24 m) or more in length but less than 400 gt engaged in international voyages (excluding fixed or floating platforms, FSUs and FPSOs) will have to carry a Declaration on Anti-fouling Systems signed by the owner or autho- rized agent. The Declaration will have to be accompanied by appropriate docu- mentation such as a paint receipt or contractor invoice. • Anti-fouling systems to be prohibited or controlled will be listed in an annex (Annex 1) to the Convention, which will be updated as and when necessary. • As recommended by the 21 st session of the IMO Assembly, the Conference agreed to an effective implementation date of January 1, 2003 for a ban on the application of organotin-based systems, • In November 1999, IMO adopted an Assembly resolution that called on the
MEPC to develop an instrument, legally binding throughout the woHd, to address the harmful effects of anti-fouling systems used on ships. The resolution called for a global prohibition on the application of organotin compounds, which act as bio- cides in anti-fouling systems on ships by January 1, 2003, and a complete prohi- bition by January 1, 2008. • The new convention will enter into force 12 months after 25 States repre- senting 25 percent of the world's merchant shipping tonnage have ratified it.
Annex I attached to the Convention and adopted by the Conference states that by an effective date of January 1, 2003, all ships shall not apply or re-apply organ- otins compounds which act as biocides in anti-fouling systems.
By January 1, 2008 (effective date), ships either: • Shall not bear such compounds on their hulls or external parts or surfaces; or • Shall bear a coating that forms a barrier to such compounds leaching from the underlying non-compliant anti-fouling systems.
This applies to all ships (including fixed and floating platforms, floating storage units (FSUs), and Floating Production Storage and Offtake units (FPSOs).
The Convention includes a clause in Article 12, which states that a ship shall be entitled to compensation if it is unduly detained or delayed while undergoing inspection for possible violations of the Convention.
The Convention provides for the establishment of a "technical group," to include people with relevant expertise, to review proposals for other substances used in anti-fouling systems to be prohibited or restricted. Article 6 on Process for Propos- ing Amendments to controls on Anti-fouling systems sets out how the evaluation of an anti-fouling system should be carried out.
The Diplomatic Conference Adopted Four Resolutions:
Resolution 1: Early and Effective Application of the Convention — The resolution invites Member States of the Organization to do its utmost to prepare for imple- menting the Convention as a matter of urgency. It also urges the relevant indus- tries to refrain from marketing, sale and application of the substances controlled by the Convention.
Resolution 2: Future work of the Organization pertaining to the Convention — The resolution invites IMO to develop guidelines for brief sampling of anti-fouling sys- tems; guidelines for inspection of ships; and guidelines for surveys of ships. The guidelines are needed in order to ensure global and uniform application of the articles of the Convention, which require sampling, inspection and surveys.
Resolution 3: Approval and Test Methodologies for Anti-Fouling Systems on Ships — This resolution invites States to approve, register or license anti-fouling systems applied in their territories. It also urges States to continue the work, in appropri- ate international fora, for the harmonization of test methods and performance standards for anti-fouling systems containing biocides.
Resolution 4: Promotion of Technical Co-operation — The resolution requests
IMO Member States, in co-operation with IMO, other interested States, competent international or regional organizations and industry programs, to promote and provide directly, or through IMO, support to States in particular developing States that request technical assistance for: • the assessment of the implications of ratifying, accepting, approving, or acceding to, and complying with, the Convention; • the development of national legislation to give effect to the Convention; and • the introduction of other measures, including the training of personnel, for the effective implementation and enforcement of the Convention.
It also requests Member States, in co-operation with IMO, other interested States, competent international and regional organization and industry programs, to pro- mote co-operation for scientific and technical research on the effects of anti-foul- ing systems as well as monitoring these effects. "safe" removal, treatment and disposal of TBT from ships, and clarification on the issue of liability of future dredging and disposal of TBT-contaminated port and harbor sediments. Under current regulatory practices for most of the world, TBT in washdown wastewaters can be discharged directly into local waters.
It is quite possible that the "regulated" nations can quickly implement new requirements to correct this situation.
This implementation will result in the transfer TBT contamination to the "unregulated" countries, which are least able to deal with it. However, at IMO, there is a concern that unregulated coun- tries may unknowingly accept the envi- ronmental and human health risks to gain economic benefits from removing
TBT from ship's hulls. Market forces are selective for low-cost labor and weak environmental regulation. Unfortunate- ly, most of these developing countries do not have the funding or environmen- tal expertise available for the monitor- ing, research and technology develop- ment essential to treat and dispose TBT washdown wastewaters safely. These
New Antifouling Tech
Spurs Uncertainty
Registering a growing market uncertainty toward the ability of new TBT-free antifouling to offer the same range of benefits as TBT-based antifouling, Jotun
Marine Coatings is now advising shipowners and operators to seek the recommendations of coating manufacturers prior to applying TBT-free antifouling treatment to ship hulls. "Determining the correct antifouling and the appro- priate pre-paint procedure is becoming a very com- plicated issue. Jotun Marine Coatings is being approached by an increasing number of shipowners and operators seeking advice on new products now flooding the market and how these new technologies will affect the treatment of underwater hulls," says
Frank Mohn, Director of Jotun Marine Coatings. "This requires a detailed understanding of the various types of antifouling technologies being supplied by all manufacturers of anti-fouling."
Jotun advises owners to expect following perfor- mance: Self-smoothing; Self-polishing; No build up of leached layers; Predictability; and Tailor-made solu- tions
Since 1999, when the IMO adopted the resolution to phase out organotins used in marine coatings, paint suppliers have been scrambling to develop and intro- duce alternative anti-fouling paints in time to meet the
January 1, 2003 deadline, something that has proved far from easy. The result, according to Jotun Marine
Coatings, has been a "divergence in technology offered for sale."
Along with the divergence of technology has come questions about the mechanism and properties of new
TBT-free products and now many end-users, rightfully so, are concerned about making wrong decisions and having to live with less than good results, says Mohn.
From now until 2008, thousands of vessels with TBT- based antifoulings will drydock. The way these are handled, prior to application of new antifouling, will remain uncomplicated and offer no more challenge than it does today.
The real challenge for end-users is the wading through the wide choice-range of new TBT-free coat- ings.
Circle 43 on Reader Service Card www.maritimereporterinfo.com 22 Maritime Reporter & Engineering News