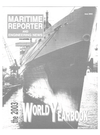
Page 77: of Maritime Reporter Magazine (June 2003)
Read this page in Pdf, Flash or Html5 edition of June 2003 Maritime Reporter Magazine
LASOX Cutting Technology
A Step Forward For Thick Section Plate Cutting
By Dr. Bill O'Neill, Institute for
Manufacturing, University of
Cambridge, U.K.
For years, general manufacturing com- panies have enjoyed the benefit of laser cutting systems for producing complex or simple parts in batch volumes as low as one, and as high as tens of thousands.
The laser is an incredibly powerful tool that remains unsurpassed in manufactur- ing activities across the world. As flex- ible and reconfigurable production tool that provides welding, cutting and machining capabilities in a single device, lasers are readily automated and have demonstrated that they can easily operate in "lights-out" mode for even greater productivity. With all this said, why aren't there any laser shipyards?
Why hasn't one of the worlds largest and most important transportation industries rushed to implement laser cutting and welding technology? The answer is that the development of the state-of-the-art laser manufacturing technology has been a long and grueling process. Early lasers were just not powerful or reliable enough to attract an industry that had the capability to process heavy section met- als using low cost and reliable technolo- gies such as oxy-fuel and plasma cut- ting, with MIG and TIG and submerged arc techniques being the process of choice for welding. Even the Lloyds approval for laser welding of ship plates has yet to see lasers become common- place in shipyards. The situation today is rather different. Lasers are now being employed commercially in thick plate cutting and welding and the industry has witnessed a quiet and rather successful processing revolution.
A new, and unexpected, breakthrough in the laser industry occurred in
November 2002 at Bender Shipbuilding & Repair in Mobile, Ala. It was there that the first commercial use of the
LASOX process cut through two in. of steel using a new cutting principle industrialized by Wayne Penn and his team from Alabama Laser. Co-devel- oped by BOC Gases Ltd. and Dr. Bill
O'Neill while working at the University of Liverpool, the LASOX process requires approximately 1 kW of laser power and uses oxygen to provide the cutting energy while the laser is used to maintain and stabilize a pre-heat - simi- lar to the gas flame in oxy-fuel cutting.
With O'Neill and his team working on the thick section problem for more than a decade, commercial laser cutting has pushed the section limit from around 15 mm in 1990, to around 30 mm in 2003, with a subsequent increase in laser power from 2kW to 6kW. The process
June 2003 remains the same except the size of the process window is inversely proportion- al to the plate thickness. Prior to the invention of LASOX, it was a daunting process to cut pieces of high thickness.
As a result, there is always the tempta- tion of turning up the power and the gas and just "letting it rip. While the
LASOX process, however, will report- edly have the ability to produce the fastest scrap metal production system in the world, it will not, however, solve the problem of producing laser cuts up from 50-75 mm. "A year ago, cutting steel thicker than two inches would have been unheard of with a 2kW laser - one in. being the maximum cutting depth undertaken commercially." said Pat
Cahill, research and development man- ager for Bender Shipbuilding. "This process has the potential to cut steel plates as thick as four in. Currently high- powered plasma cutting is limited to three in. This development opens up the possibility of a new generation of steel ships that are stronger and cheaper to build." v
With BOC Gases \ and the University of
Liverpool providing the basic technology and process ^ license for LASOX, Alabama ^
Laser Systems carried out pre-pro- duction development of the lab based process and the integration into the existing laser cutting system at Bender
Shipbuilding. The installation has been so successful that full installations at
Caterpillar, for their heavy duty mining
A firm grip, a gentle nudge, and a state-of- the-art computer keeping everything under control. Our steering and propulsion systems are made from long-lasting bronze and stainless steel.
Add our microprocessor, and you've got a flexible, integrated system that will take you anywhere you want to go. Kobelt
Manufacturing has been producing high quality marine controls and steering for over 35 years. We back every one of our products with a 5 year warranty, along with worldwide sales and support.
Contact us today!
Quality Control 8238 129th Street. Surrey, British Columbia. Canada V3W OAh
E-mail: .sales®kobelt.eom Website www .kobelt.com
Sales: bO-i.590.7313 Fax: MM:590.8313
Circle 278 on Reader Service Card 77