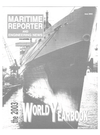
Page 79: of Maritime Reporter Magazine (June 2003)
Read this page in Pdf, Flash or Html5 edition of June 2003 Maritime Reporter Magazine
problem by examining the dynamic effects of melt and gas flow through deep section kerfs and became con- vinced that the problem could be solved by forgetting the conventional laser cut- ting approach. "In 1990 the Holy Grail at that time was the ability to cut thick plate steel. In the early 1990s, laser cut- ting was very much limited to about 12 o 15 mm (0.48 to 0.6 in.). That's when we started looking at ways in which we could assist the thickness capability of laser cutting materials. We were quite convinced that the gas played a signifi- cant role," said Gabzdyl. So we turned the basic principles of laser cutting on its head, and looked to our expertise in oxy-fuel cutting where we realised hat the oxygen is really the process work- horse," he said.
He continued: "In traditional laser beam cutting, the laser is the workhorse while the oxygen assists in the process.
The oxygen just helps. We inverted that philosophy in laser cutting and made the oxygen jet the workhorse and the laser beam the assist."
The LASOX cutting process is an exothermic burning reaction in which the heat of the laser beam is only used to bring the steel to ignition temperature at approximately 1,832°F (1,000° C). A specially designed nozzle is used to deliver a supersonic stream of oxygen to the heated spot, resulting in ignition and
Bender Pioneers LASOX
Cutting in Production
At the end of 2002, following 10 months' worth of research and development via a National
Shipbuilding Research Program (NSRP)-funded project, the team of Bender Shipbuilding (includ- ing Cutting Edge Metal Processing), Alabama
Laser Systems and BOC Gases, successfully installed and tested the only production LASOX system. Test cuts, which were performed on
November 12, 2003 using 1.5-in. mild steel demonstrated excellent results.
According to Pat Cahill, R&D manager at
Bender Shipbuilding & Repair Co., the compa- ny's existing equipment can "achieve laser quali- ty cuts through at least 2-in. steel." Cahill added that further R&D work has a goal of 4-in. steel.
Additional team members on the project include
General Dynamics Electric Boat and Caterpillar,
Inc., both of which will receive the next install- ment of the LASOX system. All have already implemented new laser technologies currently in production with other NSRP projects. This new technology was developed to meet the needs of cutting thick steel (from 50 mm min. up to 100 mm), using a relatively low laser power of less than 2 kW. LASOX is an exothermic burning reac- tion where the heat of the laser beam is utilized to bring the steel to ignition temperature. A spe- cially-designed nozzle is then used to deliver a stream of oxygen to the heated spot - resulting in ignition and sustained burning.
Bob Lewis, general manager of Bender's metal processing facility, Cutting Edge Metal
Processing, was equally impressed by the process, which allowed the piercing of 50 mm plate steel in less than two seconds.
Circle 97 on Reader Service Card then sustained burning. LASOX com- bines the benefits of lasers and oxyfuel cutting by using a very modest amount of laser energy by conventional stan- dards, about lkW, so the process can be operated with relatively small low cost lasers. This laser beam in effect replaces the fuel gas in oxy-fuel cutting. The laser beam is then combined with a high pressure supersonic oxygen gas jet, which provides the cutting energy.
Thicker material has traditionally been cut with oxyfuel and more recently with plasma torches but both processes suffer from quality issues. "When we started in the early 1990s, we would have been happy to cut one-in. steel plate. But as it happens, we've been able to cut increas- ingly thicker plate. By careful manipula- tion of the nozzle geometry and the beam char- acteristics, we can cut very thick material - up to about four in. plate," said Gabzdyl.
Another advantage of
LASOX is that it is instanta- neous. "There is no preheating ele- ment required to start the piercing \
At Catalina Express, we're considered part of the family
With their busv ferrv service between The Mainland and Catalina Isl y y Island in
California, USA, Catalina Express demand the best in reliability and performance from their vessels. That's why they chose Hamilton waterjets for the largest fast passenger ferry in their family, 'Jet Cat Express'.
No other waterjet propulsion system is as widely used and supported around the world. So, if you want a new family member you can trust, trust Hamilton
Jet to deliver.
Head Office C.W.F Hamilton & Co. Ltd. P0 Box 709, Christchurch, New Zealand. Phone: +64 3 348 4179,
Fax: +64 3 348 6969, Email: [email protected]
U.K. Office HamiltonJet (U.K.) Ltd. Unit 4a,The Birches Industrial Estate, East Grinstead, West Sussex RH19 1XZ,
United Kingdom. Phone: +44 1342 313 437, Fax: +44 1342 313 438, Email: [email protected]
U.S.A. Office HamiltonJet Inc. 1111 N.W. Ballard Way, Seattle WA 98107, United States of America.
Phone: +1 206 784 8400, Fax: +1 206 783 7323, Email: marketing8hamiltonjet.com, Website: www.hamiltonjet.com
Hamilton www.hamjet.co.nz
Circle 286 on Reader Service Card 81