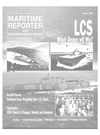
Page 18: of Maritime Reporter Magazine (August 2003)
Read this page in Pdf, Flash or Html5 edition of August 2003 Maritime Reporter Magazine
Coatings & Corrosion Control
New coatings safer, last longer
Bottom Line: It's Not Just A Paint Job
By Edward Lundquist,
Anteon Corporation
On the surface, the subject of paint seems simple. After all, it's just a paint job, right? For maritime applications, however, beauty is much more than skin deep. The coating of surfaces on ships is a complex combination of materials, chemicals and preparation to combat corrosion and maintain a sharp appear- ance. The coatings must wear well in the worst of weather and withstand the most extreme environments. They must last with little maintenance, must be earth friendly and safe for people and other living things, and last but certainly not least, they must be affordable.
The paint job found on a contempo- rary ship may look the same as that of a ship of several decades ago, when in fact very little is the same.
Combating Corrosion
Progress in coatings has been driven as much by environmental concerns as any other factor. Many traditional coat- ings are no longer acceptable for safety, health and environmental reasons, whether in manufacture, application or the resulting finished surface. Paints and coatings have traditionally been made with solid materials suspended in a solvent (which aids in the application), and leave the solid to bond with the sur- face when the solvent evaporates. Many chemicals used previously as solvents in paints, such as ketones, xylene, or toluene, are hazardous and no longer used. Lead based paints are also prohib- ited.
Chromium, a formerly prevalent ingredient in paints such as zinc chro- mate, is a cancer-causing agent.
Coatings with zinc pollute the water.
Lead, as stated, is poison and leads to serious permanent health problems.
Heavy metals used in coatings are high- ly toxic. Materials have been used as coatings, such as copper sheathing on ship bottoms. Until recently, copper was thought to be safe, but when many cop- per clad bottoms are in a harbor, the cop- per kills the marine life and a sterile marine environment results.
Some new paints are "100 percent solids," which means there is a part A and a part B that must be mixed as a resin and catalyst are mixed to make epoxy. These epoxies are non-volatile, do not cause air pollution and are non- carcinogenic. Their drawback is that the mixed epoxy is very thick, difficult to apply, and must be used right away.
Another approach is the use of water- soluble paints, similar to latex paints used in homes. The obvious drawback is that these coatings are susceptible to being worn away by water, and the mar- itime application provides ample oppor- tunity for attack by water. Like the epoxies, the water-soluble paints are not a toxicity problem or an environmental hazard. They are safe to store and use.
Teflon has proven to be an effective non-sticking surface for cooking, and it turns out that barnacles and other marine life don't like to stick to it as much as they do on other surfaces. Teflon coated hulls became an effective way to keep bottoms from fouling, keeping speeds and operating efficacies and economies up and maintenance costs down. But
Teflon by itself is not the best anti-foul- ing coating. Teflon in combination with silicone has proven to be even better, actually repelling water to reduce drag. "This is an expensive combination," says A1 Daech. a research engineer at the Gulf Coast Region Maritime
Technology Center, affiliated with the
University of New Orleans. "It costs $35 per sq. ft., and there's a lot of square feet to cover on the hull of a ship. Cost becomes a limitation."
Daech sees great promise for lithium as a key ingredient in ship coatings. "It's one of the most common elements. It's the lightest metal, almost a gas," he says. "Lithium can replace chromium and lead. It's plentiful, and it's environmen- tally acceptable.
Another new method, Daech says, is electrostatic spraying of paint, involving the spraying of charged particles of plas- tic onto a negatively charged surface.
The metal surface is then heated to fuse the paint. "The materials are reasonable.
There's a capital investment, but once you've invested in this equipment you can use it for a number of years and amortize it."
Daech says electrostatic coating is being used now on components. It cre- ates a tough coating, not unlike baked enamel on cookware.
Teflon, which is being used in some applications on bottoms, repels water.
The water actually beads up. But Daech says that an even better way to reduce friction is to introduce a stream of air between the Teflon and the water. The ship is actually riding on a stream of compressed air, which has less resist- ance than water.
He also points to alloys that have been upgraded. Stainless steel, and now cor- rosion resistant steel (CRES), doesn't need to be painted. "You pay an extra capital expense. But it's care free for a long time once it is in place."
Ballast Tanks Pose a Challenge
All large ships have voids and tanks that are difficult to access and may not be visually inspected for many years, if at all. These closed spaces require coat- ings that can last for decades without repair.
Ballast tanks can account for up to 45 percent of total painted area on a vessel and are subjected to an "aggressive cargo, namely seawater, as well as
Hempel Extends Range
Hempel's range of IMO 2003 compliant antifouling products consist of three products: GLOBIC,
OCEANIC and OLYMPIC, each designed to fulfill different needs in terms of price and quality.
Globic: Designed as a highly efficient, TBT-free, self-polishing and self-smoothening antifouling with very high volume solids, which can be specified for up to 60 months. Globic is available in four different polishing rates ensuring optimum specification.
Oceanic: Designed to be a cost-effective, TBT-free, self-polishing antifouling with high volume solids, which can be specified for up to 36 months on vertical bottoms and 60 months on flat bottoms. Oceanic is available in two different polishing rates.
Olympic: Designed as an economical, TBT-free, self-polishing antifouling, which can be speci- fied for up to 36 months.
Development of the new products began with Globic in 1990 and was already then based on more than a decade of research into TBT-free antifoulings. The Globic brand was launched as a commercial product line in the beginning of 2000, and the portfolio incorporates a unique use of fibers in the paint. According to the manufacturer, it is the first time micro fibers have been incorporated successfully in self-polishing paints. In combination with the binder system, the fibers form a three-dimensional structure that provides an extremely strong and flexible paint film while maintaining the polishing and smoothening properties of a self-polishing, antifouling paint.
Based on the expertise obtained during the development of Globic, Hempel has successfully for- mulated Oceanic and Olympic with ingredients that are relatively inexpensive. Together, with
Globic, these products cover all requirements in terms of price and performance.
Our share of the bulk carrier market is increasing as we see more and owners realize the value of having an effective antifouling. Paints for the future is expected to be silicone Fouling Release products i.e. like Hempasil. These coatings are biocide-free and release the fouling organisms due to an extreme smooth surface. It is at this stage hard to see if this type of paint will be suit- ed for the majority of the bulk carrier market since a certain speed (normally min. 15 knots) and activity (normally min. 75 percent) is required.
Circle 196 on Reader Service Card 18 Maritime Reporter & Engineering News