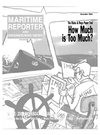
Page 45: of Maritime Reporter Magazine (November 2003)
Read this page in Pdf, Flash or Html5 edition of November 2003 Maritime Reporter Magazine
Successfully implementing Lean prin- ciples in any manufacturing process is a daunting task. Given the current slump of the U.S. shipbuilding industry, the potential benefits of Lean Shipbuilding should be given serious consideration by managers, designers, and members of the workforce. Implementing Lean
Shipbuilding constitutes an investment for the future of shipbuilding. With this in mind, the overarching goal of Lean
Shipbuilding is 100 percent customer satisfaction through the elimination of waste. The five elements of the Lean
Shipbuilding model are outlined as fol- lows.
Just In Time
The first of the five Lean Shipbuilding components, Just-In-Time (JIT), is defined as the right quantity and part, at the right time and place. JIT is essential to three areas of lean manufacturing, which will be discussed below: One- piece or continuous flow, takt time, and the pull system.
One-piece/Continuous Flow
One-piece flow involves identifying subassembly, unit, and part families that move through the same set of processes and creating assembly procedures for their production. Japanese shipbuilders who implemented lean principles such as this increased their productivity by 150 percent from 1965 to 1995 .
First, planners define hull divisions, then subdivide them into parts or blocks. which in turn are divided into sub- blocks or subassemblies and so on.
Defining zones that are one-piece pro- ducible completes the zoning processes.
Intricate detail design simplifies one- piece construction along the production line. One-piece flow requires master scheduling execution for complete sub- assembly integration, as shown per
Figures 2 and 3.
Takt Time
Lean Shipbuilding processes introduce a pacing mechanism, called takt time, to help regulate production flow. "Customer Demand Rate" essentially defines this takt time. The concept of takt time can be expressed as follows:
Where: = Available time = Customer Demand Rate = Takt time
Ship production requires a six-month to one-year duration. Although integrat- ing takt time may be difficult, once in place, takt time simplifies monitoring of production-flow uniformity and fore- casting of work packages. It also serves the planning department as a tool to evaluate how well the production process is going.
The Pull System
Although Lean Shipbuilding discour- ages it. certain aspects of shipbuilding find large batch processing applicable.
When such an applicable occasion aris- es. Lean Shipbuilding utilizes The Pull
System as described above.
Utilizing the pull system, the accessi- bility and organization of "stamped" parts are increased. Periodically, a sig- nal will indicate that personnel need to re-supply the parts in order to keep up with the production line demand. This way the production line "pulls" parts versus receiving "pushed" and unwanted parts.
Built In Quality
Built-in quality represents the second component of the Lean Shipbuilding model. Built-in quality in a one-piece flow or continuous flow shipbuilding system is achieved through closely con- trolled accuracy. Each piece is inspected as it is passed to the next process, so inaccurate interim products will not flaw downstream processes.
Operational Stability
Operational stability is vital to achieve a continuous-flow system such as Lean
Shipbuilding. Standardized work and the 5Ss are two approaches that help to achieve this operational stability.
Standardized Work
According to Storch (Storch. 1995), "Standardization is the principle of design-for-production that is likely to lead to significant improvements in pro- ductivity." This is also true in Lean
Shipbuilding. Standardization occurs in a manufacturing process as well as design. Standardization in shipbuilding can be applied in several stages, from elementary components and assembled units to a complete ship design. Since the shipbuilding market is likely to con- tinue to be characterized by varying and individual product requirements, a stan- dard ship series may not be feasible.
Consequently, efforts at design stan- dardization should be concentrated at the component, subassembly, block, and outfit unit levels. Standardization, as described here, is what will most likely lead to significant improvements for productivity. Standards achieve repeata- bility, and repeatability, along with con- tinuous improvement, achieves higher efficiency.
Five Ss
The 5Ss aim to achieve organization in
Lean Shipbuilding. The 5Ss are: 1. Sort — Identify value added and non-value added procedures. Non-value added proce- dures should be eliminated. 2. Stabilize (orderliness) - "A place for every- thing and everything in its place." 3. Shine (cleanliness) - Inspection, which exposes abnormal and pre-failure conditions. 4. Standardize (create rules) - Maintain and monitor the first three Ss. 5. Sustain (self-discipline) - Maintaining a sta- bilized workplace is an ongoing process of con- tinuous improvement.
Conclusion
The American Shipbuilding industry is in need of change to become competi- tive in the international shipbuilding market. While some shipyards in the international market are able to domi- nate through relatively low labor rates, other yards can develop competitive niches through implementation of new methods such as Lean Shipbuilding.
Implementing modern manufacturing processes as well as management sys- tems can help to shrink the competitive gap between the U.S. shipbuilders and the rest of the world. Lean shipbuilding offers both of these improvement oppor- tunities.
References • Liker J, Lamb T. Lean Shipbuilding. Paper presented at the 21)01 Ship Production Swnposium: SNAME. 2001
June 11-15. 24 p. • Liker J, Lamb T. Lean Manufacturing Principles Guide.
Version 0.5. Deliverable 2.2, Maritecli AS/ project #10:
NSRI'. 2000 June 25. 46 p. • Lant! S. Dutta N. Hellesoy A. Daniels T. Liess I). Chew
S. ( anlietti A. Shipbuilding and Lean Manufacturing - A
Case Study. Paper presented at the 2001 Ship Production
Symposium: SNAME. 2001 June 13-15. IS p. • Storch KL. Hamilton CP. Bunch HM. Moore RC. Ship
Production 2nd Edition. Centervillc, Maryland: Cornell
Maritime Press. 1995 • Hirano H. 5 Pillars of the Visual Workplace:
Productivity Press. 1990 • Munro & Associates. Inc. Design Profit, course note- book: Munro & Associates. Ini . 19X9 ' Standard C. Davis I). Running today's Factory. A
Proven Strategy Inr Lean Manufacturing. Cincinnati.
Ohio: Hanser Gardner Publications. 1999 • Womack JP. Jones DT. Lean Thinking. New York:
Simon & Schuster. 1996 • The University of Michigan. Shipbuilding Pictures
Database. http://mvw.Nsnet.com. I99X-2000.
INTRODUCING THE
AUTOMATED
MARINE COATING SYSTEM mB* -M ; -"if ; "I
Has your proi ilication evolved?
PATENTED TECHNOLOGY
Please visit us at:
The International WorkBoat Show
Booth #2821, New Orleans, Dec. 3,d -51t1
VISIONS EAS
ROBOTIC MARINE SOLUTION )
US Office European Office
Fort Lauderdale, Florida Helsinki. Finland
P 954 522 1445 P • 158 40 564 3284
F 954.522 1665 F t 358.9.541 4490
InfoUS^visionseast net infoEUROPEfa>visionseast.net www visionseast. net
Circle 263 on Reader Service Card 44 Maritime Reporter & Engineering News