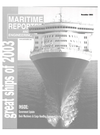
Page 36: of Maritime Reporter Magazine (December 2003)
Grear Ships of 20003
Read this page in Pdf, Flash or Html5 edition of December 2003 Maritime Reporter Magazine
Deck Machinery & Cargo Handling Equipment
Techcrane Designs, Builds 125-ton Crane for Midnight Wrangler
Techcrane Global Corporation is a
Covington, La.-based marine crane manufacturer/distributor who recently installed Techcrane Model F250-100 onboard Torch Offshore L.L.C.'s
Midnight Wrangler. This was a crane custom-designed for Torch with a maxi- mum capacity of 125 tons at 30-ft. reach. Time lapse between design con- ceptions to fabrication in Covington,
La., was less than six months.
The bid was awarded to Techcrane in
December of 2002 for delivery in mid 2003 and is a part of the project to con- vert the Midnight Wrangler into a deep- water pipelaying vessel. In order to accommodate these deepwater arenas, a winch was specially designed by Lantec on behalf of Techcrane for the F250 to handle 8,000 ft. of two-in. wire rope.
This winch is reeved with a single part line and lifts 60 metric tons on the top layer of the winch.
Other custom features include a state- of-the-art load sensing and payout meas- uring device retrofitted on the large hoist and electric motors powering the crane fitted with "Constant Tension" tugger system. "The crane was successfully load tested by using water weight of 88,000 lbs. at 90 ft. reach meeting the requirements of Torch," said Farhad
Shad, president of Techcrane Global
Corporation. The F250 has been in operation onboard the "Midnight
Wrangler" in the Gulf of Mexico.
In other recent projects, Techcrane was awarded the bid to install crane model F200-100 and EBI model C30- 60 onboard the lift boat designed by
A.K. Suda for C.S. Liftboats in Erath,
La. This crane has a boom length of 100 ft., capacity of 100 tons at 30 ft. reach and 23 tons at 100 ft. reach.
Working on the Caballo de Trabajo in the Bay of Campeci is Techcrane's T200 telescopic crane. This crane, construct- ed for Oceanographia and serving the oil company Pemex, "was the first of its kind in capacity," Shad said. 100 tons at 30 ft. reach telescopic crane using EBI's unique rack and pinion telescoping mechanism. Techcrane is currently in the midst of a design for a container han- dling crane to be used aboard ships.
Circle 14 on Reader Service Card
Global Materials Services Venezuela Takes Two
There is a growing 24/7 attitude in Venezuela, partic- ularly aboard a certain floating platform at mile 182 on the Orinoco River in Puerto Ordaz Venezuela. The
Bauxilum Company mines Bauxite from their mines in central Venezuela, and the Bauxite is loaded onto barges and shipped 350 miles downstream to Puerto
Ordaz, where the material is offloaded by 2 E-Cranes.
The Bauxilum Company uses the raw material and processes it into alumina, which is the first step in
Aluminum making. Sounds simple, but there is more to it. It takes five tons of bauxite to make two tons of alu- minum oxide trihydrate (alumina). Two tons of alumi- na is melted into one ton of aluminum. It takes about 157,000 kWh to make one ton of Aluminum under very low current, but approx. 150.000 volts. In short, it takes enormous amounts of material and energy to pro- duce aluminum. The Bauxilum Company contracted with Global Material Services, LLC (GMSV) of
Memphis, Tenn.. to handle 5.3 million tons of bauxite annually for the company. Making the project more interesting was the fact that this has to be done in seven months, since during the dry season the Orinoco is too shallow to allow barges to pass downriver.
To this end, a total fleet of 161 barges — each tow consisting of 25 barges (5x5), each barge is 195 ft. long, 35 ft. wide, 12 ft. deep, holding approx 1.830 metric tons of bauxite, move 210 days a year, seven days a week, 24 hours a day continuously between the mine and Puerto Ordaz where they are unloaded to 34 feed the plant.
GMSV was looking for a more efficient unloading solution, since the existing cranes required high main- tenance and were unable to fulfill the increased pro- duction requirements.
GMSV contacted E-Crane USA for a solution. E-
Crane together with their Belgian partner, Indusign NV delivered a solution in record time: • Two 1500 series, model 11264 E-Cranes mounted on a 100 ft. wide by 400 ft.' long floating plat- form. Each E-Crane feeds a floating hopper that is con- nected with the plant's conveying system and material is put directly into the 2 million ton plant storage area.
One hitch encountered, through no fault of GMSV or
E-Crane, was the conveying system. Due to the mate- rial characteristics, the conveying system could not keep up with the production capabilities of the E-
Cranes and the plant requirements. GMSV opted to replace one 1500 Series E-Crane with the next larger model to offload a larger amount of "buffer" material and compensate for frequent unplanned conveying out- ages. There was a small window of opportunity to make this switch, since the plant operates 210 days continuously, but Indusign manufactured and installed a 2000 Series Model 18264 E-Crane in record time.
The combined production of a 1500 and a 2000 series
E-Crane is now more than sufficient to compensate for the unforeseen conveying "issues".
Circle 15 on Reader Service Card
Maritime Reporter & Engineering News
MIDNIGHT
VIR&NCLER ran «m