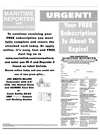
Page 25: of Maritime Reporter Magazine (February 2004)
The Tanker Yearbook: ATB Edition
Read this page in Pdf, Flash or Html5 edition of February 2004 Maritime Reporter Magazine
Tanker Technology
Rebuilding Single Hull Tan
We first visited Maritrans' double hull rebuild program in 1998 ("Great Ships of 199,S- Maritrans is Making
Waves") as the company delivered its first rebuilt dou- ble hull barge- the 23,000 DWT "Maritrans 192" (See
Figure /. opposite page).
Since then Maritrans has successfully rebuilt three similar size barges and is currently working on a fifth that includes a 60-ft. lengthening. Maritrans patented barge process was described in detail in our earlier arti- cle. As is shown in Figure 2. an inner bottom and dou- ble side is built upon the existing single hull structure. (Red is new and blue is existing.) New lower bulk- heads are also constructed. The existing deck and upper bulkheads are returned in such a fashion as to create a raised trunk to retain the original cargo vol- ume. Maritrans learned a great deal from its barge rebuild program in terms of pre-measurement. modu- larization. assembly process, and efficient detailing.
Now the company is ready to apply these lessons to an even greater challenge: rebuilding tankers.
Maritrans has completed the contract design for dou- ble hull rebuild of its two diesel tankers. M/V
Allegiance & M/V Perseverance. There are many sim- ilarities to the barge rebuild program, but also some important differences. The new inner bottom structure can be laid directly on top of the existing structure. The tanker internal structure is already high enough to meet the required spacing between hulls. On the barges, it is necessary to build up to get the necessary spacing between the hulls. The double sides are built on the outside (Figures 3 & 4 - See Illustrations on page 24).
For newer single hull MARPOL tankers (which are the most likely to be rebuilt), the cargo volume lost in
The cost of the tanker rebuild process is a quarter to a third of the price of newbuilding that includes a generous allowance for upgrades the new inner bottom ballast tanks is more than offset by the gain in cargo volume by converting the existing segregated ballast tanks back to cargo (Figure 5).
Let's look in more detail at the tanker rebuild process for which a patent is pending:
In Figure 6, brackets and portions of bulkhead are cut free. The brown colored parts will be modified and re- used. The red colored parts can be discarded. For this study, access is from the side, but top access is a design option. Next, the new inner bottom plate is laid on top of the existing transverses. The panel stiffening is inside the cargo tank that eases assembly, but still results in far less obstructions in way of cargo than a single hull. In Figure 8. the inner bottom plating is completed, the modified brackets are re-installed, and a new corner piece is placed where the previous turn of the bilge was. Finally, the original turn of the bilge including the stiffening and bilge keel, is installed exactly two meters further outboard from its old posi- tion. The double side module is then installed above the relocated turn of the bilge. Figure 9 shows the side module installation and Figure 10 shows the complet- ed newly double hull tanker midship section.
The cost of the tanker rebuild process is a quarter to a third of the price of newbuilding that includes a gen- erous allowance for upgrades. Both OPA-90 and IMO
Let's Double Hull a Tanker, Easy as 1 2 3 • • • mm • • • m m •
Figure 8 - Continuing the process Figure 6 - Pieces removed from single hull
Figure 7 - New inner bottom plate is installed
Figure 9 - Side module assembly 22 Maritime Reporter & Engineering News