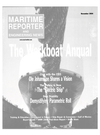
Page 37: of Maritime Reporter Magazine (November 2004)
The Workboat Annual
Read this page in Pdf, Flash or Html5 edition of November 2004 Maritime Reporter Magazine
The Workboat Annual
Caterpillar
If indeed there is strength in numbers, then
Caterpillar's propulsion prowess is of Herculean pro- portion. The international company serves a diversity of power needs around the globe, giving it an unri- valled engine installation base from which it can con- tinuously tweak and improve current models while grooming the next generation of powerplants.
The companies Advanced Combustion Emissions
Reduction Technology — or more simply ACERT — is the result of an initiative started with R&D funding in 1999, an estimated half billion effort to: meet the most stringent current emission rules: enhance true customer value; minimize pollutants where they are generated, i.e. in the combustion space; and, to serve as a stepping-stone for meeting future regulations apply- ing evolutionary steps. The effort continues today, aim- ing to meet the high standards of "Near Zero
Emissions".
Emissions have been the primary driver of engine development during the last decade, said Dr. George
Lustgarten, Director Power Systems Engineering,
Caterpillar Inc., at a presentation on the matter at the
SMM 2004 exhibition in Hamburg, Germany. The most restrictive on-highway limits precede only by 2-4 years the land based application. NOx and particulate emissions have been dramatically reduced and will be reduced by an additional 95 percent until 2010.
Eventually all emissions will converge towards a "Near
Zero Emission" situation. Engine makers of all shape and size are increasingly being pressed by internation- al, national and regional authorities to minimize engine emissions, while simultaneously being squeezed by vessel owners to improve fuel efficiency and engine reliability. In essence, engine makers must be all things to all people. "Increasingly it is going to take more and more money to compete," said Dra Wiersema, Business
Development, Caterpillar Marine Power Systems.
When asked about competition and consolidation, he said "If you are marginal and don't have the R&D money, you won't be able to compete in the future.
Increasingly, we will see the number of engine makers drop." For Caterpillar, the R&D initiative is massive and ongoing. Including the effort to bring ACERT to market. Caterpillar's Research & Development (R&D) activity is supported by its Technical Research Center located at Caterpillar's headquarters in Peoria, 111. It supports the company's engineers with fundamental research on combustion, emissions, noise, structures, advanced materials and complete power systems.
Engines are tested in over 100 cells capable to accom- modate units up to 9,000 hp.
Getting ACERT-ive
ACERT is Caterpillar's solution to the ever-increas- ing environmental and performance demands put on engine makers, and is indeed a systems approach to reducing NOx and particulate matter while providing attractive in-service performance numbers. ACERT is designed to allow the combustion process to be shaped and managed with an extremely high degree of preci- sion, meaning that emission requirements are met more quietly and with less smoke. The ACERT solution is, in fact, the combination of several separate systems, which collaborate to produce desired results in marine and other applications. The components include: • Electronic Controls: The Cat ADEM electronic controller acts as the brains of ACERT. Pioneered by the company nearly 20 years ago, the ADEM controller coordinates and enhances fuel delivery, air supply and other engine functions to maximize performance. • The Fuel System - the Injector in particular:
Multiple injection fuel delivery introduces fuel into the combustion chamber in a series of precisely timed "microbursts", allowing control over many more vari- ables during the combustion process. • The Air Handling Components: Cat engines with ACERT use a variety of refined air management technologies, and benefit from innovations such as variable valve timing; series turbocharging and MaK
Flex Cam technology. • Variable Inlet Valve Timing: Uses electronically controlled hydraulic actuators to govern when valves open and close to let air in and exhaust out of the com- bustion chamber. • Exhaust After Treatment "When we talk about ACERT. we're talking about a lot of technologies that address many different areas: emissions, durability and reliability." said Wiersema. "ACERT is the combination of these technologies that get us there." "ACERT is scalable, flexible and adaptable," said
James Weber, Applied Technology Development
Manager.
ACERT debuted in Caterpillar truck engines, a stan- dard progression to market as this sector has environ- mental emission laws were more strict and implement- ed sooner. The development of the technology on the truck side, which obviously is a much higher volume market for the engine maker than marine, is an impor- tant point for the marine market as the magnitude of the truck engine market allowed much of the R&D cost to be passed off here.
While holding the line on costs is critical for the marine market, equally important is the fact that the
ACERT solution is a combustion technology — an internal solution - meaning that as environmental reg- ulations get even tighter, the engine maker has the capability to optimize performance without the use of add-on equipment.
ACERT provides performance, fuel economy and durability without the addition of external solutions, which would require more maintenance and add
November 2004 37