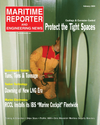
Page 20: of Maritime Reporter Magazine (February 2, 2005)
Read this page in Pdf, Flash or Html5 edition of February 2, 2005 Maritime Reporter Magazine
20 Maritime Reporter & Engineering News
LNG carriers have leapt in size to break the 200,000 cu. m. barrier - what are the primary technical factors involved in making this jump?
Qatargas' recently contracted 209,000 cu. m. and 216,000 cu. m. LNG carriers from three Korean yards have seen gas ships take a major step forward in size.
The increasing demand for LNG, espe- cially in the U.S. and Europe, and the need to reduce long haul transport costs from the Middle East to the U.S. is driv- ing the increase in ship size, although whether we will see a trend of ever larg- er ships for general trades is question- able, as LNG carriers are restricted to an upper limit of around 155,000 cu. m. by existing port facilities. The bigger sizes are therefore limited to specific projects which involve either the construction of new terminals specially designed to han- dle these carriers, or the construction of cargo tanks for LNG offshore floating units.
Tank Size and Configuration
There are several technical factors to be considered during the design, con- struction and operation of large LNG carriers, primarily impacting tank size and configuration and propulsion.
Tank size becomes important in light of the increased beam for larger ships and overall tank length needs to be con- sidered from the point of view of pres- sure loads due to fluid motion in a laden tank. There are two options for a larger ship - five tanks of conventional size, or four larger tanks. The fivetank configu- ration is inherently less 'risky', as knowl- edge of the ability of a containment membrane to withstand sloshing loads is based on tanks of conventional size.
Further, model testing demonstrates that the highest fluid pressures are associated with diagonal tank motion - lengthening the tank and hence the diagonal could result in more pressure on the tank mem- brane. However, shipyards have been looking into the issue of tank configura- tion for a number of years in anticipation of the ordering of large LNG carriers.
Daewoo Shipbuilding and Marine
Engineering (DSME), for instance, has carried out a number of studies to vali- date bigger tanks, including: • LNG tank sloshing studies at MAR-
INTEK in Norway as part of a joint development project with Lloyd's
Register cargo containment system capability testing by dry-drop tests carried out at the Korea Institute of Metals and
Machinery dynamic hydro-elasticity properties of cargo containment systems by both numerical analysis and experiments at the University of Illinois in the U.S.
New Propulsion Options
For the larger ship sizes, propulsion has become a major issue. The sheer size of the vessels has led to the devel- opment of a twin-skeg, twin-screw arrangement as a means of maintaining normal trading speeds. Further, the draft limitation imposed on the new genera- tion of LNG tankers makes it difficult to design an efficient propeller or hull form for a single-screw vessel.
This in turn has prompted the industry to turn away from the traditional steam turbine propulsion utilised by the vast majority of the world's LNG fleet. The overall complexity and cost of a twin- screw steam turbine arrangement would involve a multi-input gearbox and very large steam-raising plants, making twin- screw steam turbine propulsion cumber- some and expensive.
The industry has therefore turned towards a number of new propulsion options. These are: dual-fuel diesel electric twin slow speed diesel with relique- faction gas turbine.
The recently ordered Qatargas ships, for instance, will use slow speed diesel propulsion with reliquefaction. These advances in propulsion have implica- tions for conventional size ships as well, as all of the new options provide the main advantage of a shorter engine room and therefore more cargo carrying capacity. The 155,000 cu. m. LNG carri- ers recently ordered by BP Shipping, for instance, achieved this capacity increase by opting for dual-fuel diesel electric propulsion.
Validating the Technology
As with any new technology, the risks need to be assessed. Lloyd's Register, in its work with DSME during the process of the yard's development of a workable large LNG carrier design, carried out a number of assessments using a typical 'safety case' methodology. This method involves two key elements: a hazard identification study (HAZID), which identifies critical issues and looks at engine room arrangements and layout, and a hazard operability study (HAZOP), which looks at detailed pip- ing and instrumentation diagrams from a safety and operability point of view.
Lloyd's Register Asia's Busan Office faciliated a number of safety cases for
DSME, with input from other Lloyd's
Register Group offices around the world. "Both types of studies were car- ried out using a prescribed format of capturing data in a workshop environ- ment with the designers, engine manu- facturers, component suppliers, classifi- cation and the intended operator," says
Thanos Koliopulos, Special Projects
Manager for Lloyds Register's Oil and
Gas Division. "The key benefits of this approach are that it gives the necessary confidence to all parties involved and deals with all the technical issues on the table." One of the first HAZIDs Lloyd's
Register Asia carried out for DSME assessed the safety, operability and maintainability of dual-fuel propulsion.
A key output of this first HAZID, says
Koliopulos, was the adoption of double- wall gas supply pipework instead of the conventional single-wall arrangement.
This finding made dual-fuel a more viable arrangement from the safety and operability point of view and enormous- ly improved the engine room layout. "Using the safety case methodology, we were able to arrive at a workable technical solution which addressed all the identified risks," says Koliopulos. "This method of validating new technol- ogy has proved to be invaluable, both for Lloyd's Register and for DSME, which has now decided to apply this approach to qualify other propulsion options."
Source: Lloyd's Register, Horizons,
Issue 10, December 2004. For more information contact Thanos Koliopulos,
Special Projects Manager, Lloyd's
Register Oil and Gas at thanos.koliopu- [email protected]
Tanker Technology
The Birth of the Large LNG Carrier
Tanker Market Snapshot • Suezmax
Newbuilding & Secondhand Sales
The Suezmax newbuilding market has seen an impressive jump in prices this year. The average newbuilding price for 2003 was $48M, this year the average price was $63M, the highest average price over the last 10 years. Top
Tankers lead the buyers market for
Suezmaxes this quarter, purchasing five tankers from Essar Shipping for $256.5M. All the vessels are early 1990's built and scheduled to be deliv- ered to Top Tankers during the first quarter of 2005. Thenamaris sold the 1988 built Seavoyager (148,349 Dwt) to Mercator for $37.5M. Thenamaris also sold the 1989 built Matilda (147,500 Dwt) to Berlian Laju Tankers for $31M. Nordic American Tanker
Shipping purchased the 1996 built
Wilma Yangtze (149,000 Dwt) from
Wilhelmsen Marine for $66M. Wah
Kwong purchased a Geden Lines new- building (159,000 Dwt) scheduled to deliver in 2007 for $70.5M. There were no new confirmed orders for
Suezmaxes during the fourth quarter.
Fleet Additions & Deletions
The demolition market was quiet this quarter for Suezmaxes, owners were taking advantage of the spot market instead of selling their vessels for scrap.
Scrappings for 2004 stayed consistent with the number of vessels scrapped in 2003 with 14 vessels deleted from the trading fleet. According to the new EU phase-out schedule, over the next three years the numbers of vessels set to exit the fleet gradually decreases with very little activity expected in the demolition market. Suezmaxes ended the year with the second highest number of deliveries in 10 years, second only to last year.
The next four years show little change with about 30 vessels expected each year. Only five vessels were delivered during the fourth quarter bringing the total number of Suezmaxes delivered to 25. BP took delivery of the second ship scheduled to deliver in 2004, the
Alaskan Explorer (185,000 Dwt). The
Aegean Dignity (159,200 Dwt) was delivered to Arcadia, the second of two sisterships scheduled to deliver from
Hyundai Shipyard. Naviara Tapias took delivery of the Teide Spirit (159,000
Dwt), the first of three expected over the next year. The trading inventory ended the year with 320 vessels.
MR FEBRUARY 2005 #3 (17-24).qxd 2/2/2005 9:34 AM Page 4