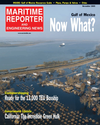
Page 67: of Maritime Reporter Magazine (November 2005)
The Workboat Annual Edition
Read this page in Pdf, Flash or Html5 edition of November 2005 Maritime Reporter Magazine
November 2005 67 we have explored many options and found that existing solutions typically do not live up to what they prom- ise," he said. "Pressure drop and the clogging of tradi- tional filters, for example, can lead to difficulties with crankcase pressure level, stability and control."
PureVent, which has been developed by Alfa Laval and tested by Wärtsilä, represents a new approach to crankcase gas cleaning in high-capacity situations.
Developed specifically for marine and power plant applications, it uses centrifugal separation to remove oil mist and other particles.
As Carlberg explains, centrifugal separation offers great advantages over filters and other cleaning tech- niques. "Centrifugal separation achieves a cleaning level filters cannot hope to match, and they do so with- out the oily waste associated with filter systems."
From an engine builder's perspective, PureVent is advantageous, as the compact separator has a size of just 30 l for any size of engine, and it weighs less than filter alternatives. Recovered oil can even be recircu- lated and used for engine lubrication.
PureVent uses high-speed centrifugation to clean oil, soot and unburned fuel from crankcase gas. The prin- ciple is similar to that of Alfa Laval's Alfdex, which has been used since 2002 to clean crankcase gas in trucks and buses on land.
PureVent consists of a disc stack made from a special composite material, which is enclosed in an aluminium housing. Connected to this is an electric motor that drives the disc stack.
Uncleaned crankcase gas enters at the bottom of the separator, then it passes into the disc stack. Centrifugal force presses the oil and soot out between the discs, allowing it to collect on the inside of the disc stack housing. This leaves virtually oil-free air, which can be released into the atmosphere.
For greater environmental benefit, the collected oil can be recirculated through the separator and used again as engine lubrication. Alternatively, it can be drained off for use in the incinerator or stored and sent for deposit.
In a diesel installation or a standard gas-engine installation, the cleaned air is released from PureVent into the atmosphere. However, in a gas engine it is also possible to route PureVent's output into the engine's turbocharger. Such a closed system enhances and safe- guards engine performance, since it eliminates the risk of turbocharger fouling or oil accumulation in the intercooler. Most importantly, a closed crankcase ven- tilation system eliminates all emissions of crankcase gas.
Circle 15 on Reader Service Card
SeaProtect from Westfalia
Westfalia Separator offers separating solutions to deal with recent laws and directives emanating from the International Maritime Organization (IMO) to pro- tect the ecosystem in the oceans. The new BilgeMaster,
SludgeMaster and
CombiMaster systems from Westfalia are designed to secure the oceans' sensitive ecosystems effectively and also provide pro- tection for the value of the ship owner's investment. The main features of the systems are: high separating efficiency, continuous unmanned operation, combined with service friendliness, and reduced dis- posal costs. The systems meet the prevailing statutory regulations of the IMO with a residual oil content sub- stantially lower than 15 ppm. With an additional facil- ity, the BilgeMaster can achieve a residual oil content of even less than 5 ppm.
BilgeMaster: Performance up to 6000 l/h
The BilgeMaster system is designed for ships that use high-density residual fuel oils. The system is sup- plied and installed as a self-contained Centripack unit incorporating all auxiliaries necessary for operation.
The four available performance classes (BilgeMaster 200, 1500, 3000 and 6000) operate in capacity ranges of 200 to 6,000 l/h. The centrifuge used in the
BilgeMaster operates with the HydroStop system
Circle 231 on Reader Service Card
Circle 269 on Reader Service Card
Pipes, Pumps & Valves
MR NOVEMBER 2005 #9 (65-72).qxd 10/28/2005 11:26 AM Page 67