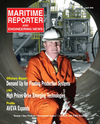
Page 26: of Maritime Reporter Magazine (April 2006)
The Offshore Industry Annual
Read this page in Pdf, Flash or Html5 edition of April 2006 Maritime Reporter Magazine
26 Maritime Reporter & Engineering News gas processing capacity. The past five years have seen seven production semis placed in service, including two large gas condensate production semis,
Asgard B and Kristin for the North Sea, and the NaKika production semi in the
Gulf of Mexico, which at 1920 meters holds the current water depth record for floating production systems. Nine TLPs have been installed since the beginning of the decade, including two wellhead units off West Africa and a unit in
Southeast Asia. There has also been sig- nificant growth in use of production spars during the first half of the decade.
Twelve units have been delivered since 2000, all for placement in the Gulf of
Mexico. By end 2006, counting the units to be installed during this year, there will be 194 floating production systems of all types in operation.
Advantages/disadvantages of various floating systems
FPSOs are the most common type of floating production system. They repre- sent 61 percent of the production units now in operation and 70 percent of the production units on order. They are located in all major offshore areas, except the Gulf of Mexico. FPSOs have the advantage of providing field storage, which enables them to be utilized inde- pendent of pipeline infrastructure. They are also less weight sensitive than other types of floating production systems and the extensive deck area of a large tanker provides flexibility in process plant lay- out. Another advantage is the ability to utilize surplus or aging tanker hulls for conversion to an FPSO vessel, a solu- tion which can be relatively inexpensive compared to building a new hull. The disadvantage is that the subsea tiebacks associated with FPSOs generally bring higher well maintenance costs.
Production semis comprise the second largest segment of floating production systems. They represent 21 percent of all production floaters in operation and 13 percent of the current floater order backlog. This type production system was a popular solution during the early years of floating production. A large number of surplus drill rig hulls were available that could be fitted with process plants and converted relatively cheaply into production units. But when the availability of surplus hulls dried up in the 1990s, the semi as a production facility became less attractive than
FPSOs. However, their popularity has rebounded over the past several years as development has moved to ultra-deep- water, dispersed fields. Production semis have the advantage of being able to operate on complex deepwater fields involving a large number of wells over a disbursed area. Recent orders have included very expensive purpose-built units such as Thunder Horse, P 51,
Kristin and Atlantis. But a new range of significantly less expensive light deck- load production semis capable of operat- ing in ultra-deepwater are attracting considerable industry interest. There has also been a recent project, Gomez, where the operator converted an old drill semi hull to a small production semi.
TLPs are the third most common type of production system. The 18 TLPs now in operation represent 10 percent of all floating production units and the 3 TLPs on order account for 7 percent of the order backlog. All TLPs have been pur- pose-built for the field on which they operate. Full size TLPs had been a pop- ular production option in the Gulf of
Mexico and North Sea. But Shell's
Brutus in the Gulf of Mexico marked the end of the full size TLP period. These types of production floaters are not suit- ed for use on ultra-deepwater fields.
Tendon weight grows exponentially with increasingly deeper water and the potential use of full size TLPs is gener- ally considered to be no more than 1800 meters. Mini-TLPs however remain very popular in the Gulf of Mexico.
Like full size TLPs, minis have the abil- ity to support dry trees, which is a par- ticularly desirable feature in the Gulf of
Mexico. The disadvantage is they lack storage and though they can operate in deeper water than the full size unit, they still appear to have depth limitations.
The deepest to date is the Moses TLP now on Marco Polo, which is in water depth of 1310 meters. Conceptually, there are designs for mini-TLPs to oper- ate in water depth to 2700 meters, but no unit has yet been ordered for such an application. Wellhead TLPs work in conjunction with an FPSO or production barge. They are positioned directly over the well and enable the trees to be at the surface. Production facilities are on an accompanying FPSO, barge or platform.
They range significantly in size, com- plexity and cost.
Spars are relative newcomers to float- ing production. Production spars have the ability to accommodate dry trees, a feature liked by operators in the Gulf of
Mexico where well maintenance is a particularly important issue. Water depth does not seem to be a limitation.
Spars have been utilized in water depth to 1710 meters (Devil's Tower) and the- oretically can be employed in water depths to 3000 meters and beyond. A spar is currently earmarked for the Great
White field, which at 2260 meters would be the deepest application yet for this type production system. The origi- nal classic spar design based on a full length cylinder has been superceded by the truss spar, comprised of an upper hard tank and lower truss structure.
Hoover/Diana, the largest classic spar, supports a 26,500 ton payload.
Holstein, the largest truss spar, is able to support almost the same payload on a hull that is half the weight of
Hoover/Diana. Payload up to 40,000 tons can theoretically be provided on a spar, but only with substantial increase in hull diameter. Spars can provide stor- age but to date no spar has been used in this capacity. A smaller version known as a cell spar has been used as a produc- tion system on gas fields. The Red
Hawk cell spar in the Gulf of Mexico has a bundled hull with an overall diam- eter of 19.5 meters and is able to support 4,700 tons topsides payload. A spar design was recently selected as a float- ing wellhead facility for offshore
Malaysia. It will work with an accom- panying FPSO. This is the first applica- tion of a spar as a wellhead facility and the first contract for a spar outside the
Gulf of Mexico.
Outlook for floating production
Underlying market drivers for floating production are very strong. World ener- gy demand is growing at a rate of 1.6 percent annually, driving the need to find and develop new oil and gas sources. Deepwater fields are one of the few remaining untapped sources for new production. The futures market is fore- casting crude prices in the $60+/bbl area and natural gas in the $8-9/MMbtu range at the end of the decade, providing incentive for undertaking new capital expenditures. It's not surprising that most oil companies are planning to sig- nificantly increase capex budgets for
E&P activity over the next several years.
Further evidence of the strong underly- ing market is provided by drill rig demand. Rig utilization is extremely high, pushing 100 percent in some areas, and rig rates are going through the roof as field operators try to secure equip- ment for exploration and development drilling.
We believe this market has a long way to run before losing steam. In our recent study of the floating production market, we forecast orders for 103 to 130 pro- duction floaters over the next five years.
This figure includes 75 to 95 additional units that will be purpose-built or con- verted from existing hulls and 28 to 35 redeployments of existing units. These orders are expected to generate capital expenditures of $35 to 44 billion over the five year period. In addition, orders for 25 to 35 floating storage units will generate another $1.5 billion in capital expenditures for conversion or construc- tion.
International Maritime Associates (IMA) was formed in 1973 to provide strategic planning, business development and project implementation support to clients in the marine and offshore sectors. IMA has com- pleted over 300 business consulting assign- ments for more than 130 clients in 38 coun- tries. In addition to consulting assignments,
IMA prepares multi-client studies of specific business sectors that have general industry- wide interest. These studies size and profile the business sector, evaluate underlying market drivers and forecast the available market. Among our multi-client projects have been more than 25 studies of floating production systems. The floater reports have become a popular industry reference docu- ment and most major players in the floater sector are among our clients. Further infor- mation about IMA and our multi-client stud- ies is available on our website: www.imastudies.com
Offshore Annual
Past 10 Years + 203%
Number of Installed Units 1978 1980 1982 1984 1986 1988 1990 1992 1994 1996 1998 2000 2002 2004 2006 0 50 100 150 200
FPSO
Semi
TLP
Spar 30-Year Growth of Production Floaters
MR APRIL2006 #4 (25-32).qxd 4/3/2006 12:07 PM Page 26