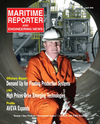
Page 34: of Maritime Reporter Magazine (April 2006)
The Offshore Industry Annual
Read this page in Pdf, Flash or Html5 edition of April 2006 Maritime Reporter Magazine
developing nations gives us some very interesting opportunities. Calculations completed for potential clients show that the Golar terminal can be available approximately three years ahead of a conventional land based terminal and that the annual savings in overall energy production cost can be more than $50 million."
Keppel Shipyard has a record of repairing 71 vessels of
Moss Rosenberg type LNG vessel. The largest LNG repair yard outside Japan, Keppel has also completed 54 FPSO/ FSO conversion projects to date. The pro- posed LNG terminal is a steel mono hull with Moss
LNG tanks arranged in the middle, with the re-gasifi- cation plant in the forward section and crew facilities with control room and utility machinery in the aft sec- tion. The LNG offloading tankers will be moored in a side-by-side configuration with the FSRU for efficient replenishment of the terminal. The FSRU will be sta- tioned offshore and, through a subsea pipeline, will be capable of a throughput of 2.75 BSCM per annum at variable gas send out pressures up to 85 bar. The
FSRU is to be permanently moored offshore with a 20- year life expectancy, and will export gas to shore through a sub sea pipeline. The proposed terminal is a steel monohull with six Moss LNG tanks arranged in the middle — with an LNG storage capacity of 129,000 cu. m. — regasification plant in the forward end and crew facilities, control room and utility machinery in the aft end. The terminal will be perma- nently moored to the seabed with a turret mooring arrangement, and the gas send-out line is arranged through the turret down to the seabed and to shore via a seabed pipeline. The LNG tankers offloading to the floating terminal will be moored in a side-by-side con- figuration. Berthing, loading and unberthing will take approximately 24 hours.
The turret is to be connected in the forward part of the ship resulting in the need for modification of the bow area. The turret will be configured to provide an essential non-rotating platform for supporting the anchor lines, flexible risers and associated control/service lines. The turret will be equipped with a turntable which allows 360 degrees continuous rota- tion of the FSRU.
The terminal will allow safe berthing of standard
LNG carriers, and there will be no need for modifica- tion of the LNG carriers discharging at the terminal.
Assuming that the terminal is being serviced by LNG carriers ranging in size from 125,000 to 137,000 cu. m., the arrival schedule will be about every nine days.
The side-by-side mooring system shall consist of: pri- mary and secondary fenders; nylon mooring lines, con- nected to the wire part of the LNG carrier line by spe- cial mooring shackles; roller fairleads, for guiding the nylon lines as required; and hydraulic quick release hooks with integrated capstan and adjustable release load.
The terminal will be fitted with an azimuth thruster, for control of the terminal during LNG carrier berthing/unberthing. The approach and berthing opera- tion on the LNG carrier will take place in a way very similar to that currently being used for onshore termi- nals. During berthing the cargo tanker will need the assistance from two tugs with minimum 50 tons bol- lard pull. After berthing a combination of transverse mooring lines and spring lines will be used to limit horizontal relative motions.
The FSRU will be provided with standard loading arms to allow side-by-side transfer of LNG and vapor return. The FSRU shall be equipped with three 16-in. loading arms; two for LNG and one for vapor return.
Operation with two LNG arms will ensure a loading time of 16 hours. Berthing, loading and unberthing will take approximately 24 hours. The loading arms will be quite similar to the type that is used on onshore termi- nals however modified to account of relative motions between carrier and FSRU.
The FSRU will also be fitted with equipment for guiding the arms onto the carrier's connection flanges.
This pre-coupling guide operation will be necessary to compensate for relative motion during coupling when the relative motion exceeds +/- 0.5m. 34 Maritime Reporter & Engineering News
LNG
INDUSTRY LEADER IN QUALITY & SERVICE
MARINE
FABRICATION & DRYDOCK • • • •
Three Full Service Shipyards
New Construction
Drydocks
Full Service Machine Shop - VISIT US AT -
WWW.RRMARINE.COM
View our newly expanded 19,000 sq. ft. fabrication shop & state of the art plasma cutting machine.
NORTH YARD: 7200 Highway 87 East
Port Arthur, Texas 77642 • 1.888.484.0860
R & R's Central, North and Sabine Pass facilities provide one-stop, service repair, conversion and construction for tankers, tugs, OSV's barges and offshore drilling rigs.
R & R Marine's three facilities are equipped to offer wide-ranging repair and conversion servic- es. From routine drydocking and inspection of
OSV's, tugs, barges and tankers, to the construc- tion and fitting of the most complex offshore drill rig conversions and upgrades.
SABINE PASS YARD: 7266 S. 1st Ave
Sabine Pass, TX 77655 • 409.963.0035
CENTRAL YARD: 5700 Procter St. Extension
Port Arthur, Texas 77642 • 409.963.0035
Circle 290 on Reader Service Card
MR APRIL2006 #5 (33-40).qxd 4/5/2006 12:43 PM Page 34