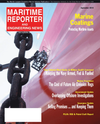
Page 30: of Maritime Reporter Magazine (September 2010)
Marine Propulsion Edition
Read this page in Pdf, Flash or Html5 edition of September 2010 Maritime Reporter Magazine
30 Maritime Reporter & Engineering News
FEATURE MARINE PROPULSION through which the demanding new emission levels can be met efficiently. Maritime Re- porter talked to the two largest, MAN Diesel & Turbo SE, on their two-stroke low speed engine developments, and with Wärtsilä Cor- poration, on their developments on the four- stroke medium speed engine side.
Developments with
Low Speed Engines
Mr. Lars Bryndum at MAN Diesel &
Turbo SE is Director of Customer Supports,
Marine Low Speed, Sales & Promotion. He has a long career within MAN, having worked at the company since 1979 in man- agement positions for R&D, on vibrations, and later design of large bore engines. Bryn- dum holds degrees in Mechanical Engineer- ing and Naval Architecture.
When asked about how MAN is approach- ing upcoming air emission regulations for their low speed engines, he goes directly to the point: "We have prepared for Tier II by means of internal adjustments of the engine.
There is higher scavenging air pressure, an- other timing of the fuel injection, introduc- tion of rate shaping in the fuel injection profile, and exhaust valve timing," he tells
Maritime Reporter. "With all these things we are ready to meet Tier II but it has cost some increase in fuel oil consumption." He points out though that the increase is not that big on the engines where the fuel injection is elec- tronically controlled. "We are all the time getting new information from testing the en- gines. We have 53 different models of stroke- bore ratio, rpm, loadings etc. so we are still learning things. We call it the Tier II evolu- tion." MAN is currently actively testing its engines to adjust the parameters further to cut fuel consumption but to still meet the emission levels required. "We do not come back to Tier I level but we will cut back somewhat," Bryndum points out.
How is your development going on for Tier
III, entering into force in 2016? "For Tier III we have to reduce the NOx by 80 percent from the Tier I level. Only in ECA areas you need this drastic reduction. Out- side ECA areas Tier II will apply." Bryndum notes that this will require shifting between modes of the engine or requiring engine ad- justments. "NOx formation is a combustion feature resulting from high temperature and high pressure, where the nitrogen and the oxygen in the air react and create NOx, which is NO or NO2. In order to reduce this chemical process you need to lower the tem- perature." Bryndum mentions that there are several methods to do this. MAN has not tested spraying water directly in the com- bustion chamber, as some other engine builders, but has instead mixed water into the fuel, which then evaporates during the burn- ing process resulting in a cooling of the gases. Bryndum points out that with this technology, called WIF, an 80 percent NOx reduction could not be reached. MAN has also tested another method, scavening air moistening, called SAM for two stroke en- gines (and HAM for four stroke) where water is sprayed into the hot air after the compressor on the turbocharger. Bryndum describes the process: You can spray in salt water which will immediately evaporate and cool down the scavening air. You then take out some droplets from that and spay in fresh water once more. Then you wash out any salt droplets after which a third spraying with fresh water takes place. The air goes through the cooler without any salt content and when the intake air enters the cylinder the temper- ature will be around 70-80 deg.C.. and com- pletely humid, saturated with water vapor.
This results in relatively less atmospheric air which reduces the amount of oxygen. Com- bined with the higher specific heat capacity of the water vapor and less oxygen with a lower partial pressure, the formation of NOx is lower. "That was one technology we tested some years back. We could reach a 60-70 percent NOx reduction but an 80 percent re- duction seemed to be out of range, so we looked for a third technology." The technol- ogy Bryndum refers to is EGR, exhaust gas re-circulation. The principle is the same as with SAM, to use another gas which has less oxygen than the atmosphere in the combus- tion process. The engine's re-circulated ex- haust gas has an oxygen level which is reduced. It is first cleaned from soot and for sulfur dioxide, components in engines burn- ing heavy fuel oil. After this it passes through a cooler and to the scavenging air receiver. "The reduced oxygen level, from 21 percent, which is in the atmosphere, down to maybe 16 percent in the intake air, gives a tremen- dous lowering of the combustion tempera- ture and therefore also in the formation of
NOx." MAN has made lots of tests with
EGR on their research engine proving that this technology works. With a recirculation of about 40 percent of the exhaust gas an 80 percent reduction of the NOx is reached. The cleaning process from soot and sulfur diox- ide, needed to avoid corrosion of the engine air cooler, is done using a scrubber, devel- oped and patented by MAN. The water in the scrubber will over time become acid and is neutralized with sodium hydroxide, or caus- tic soda, transforming into harmless natrium sulfide or natrium hydrosulfide, which can be discharged into the sea. A filter in the water loop takes out the soot. "I should add that with the EGR the fuel penalty, when you reduce NOx by 80 percent, is small, less than one percent." The pressure of the exhaust gas is approximately 0.3 bar lower than the scav- enging air pressure. When the exhaust gas is cleaned in the scrubber, its pressure has to be "For Tier III we have to reduce the NOx by 80 percent from the Tier I level. Only in ECA areas you need this drastic reduction.
Outside ECA areas Tier II will apply."
Lars Bryndum, MAN
MAN EGR engine: Graph of a Tier III compliant MAN 7S50ME-B9 low speed diesel engine with integrated EGR.