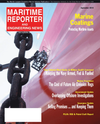
Page 32: of Maritime Reporter Magazine (September 2010)
Marine Propulsion Edition
Read this page in Pdf, Flash or Html5 edition of September 2010 Maritime Reporter Magazine
32 Maritime Reporter & Engineering News
Developments with
Medium Speed Engines
Maritime Reporter talked with Mr.
Mikael Troberg, Director, Testing and
Performance, R&D, at Wärtsilä Corpora- tion, who has worked at the company since year 1993. He started his carer at
Wärtsilä's diesel engine plant in Turku and then worked at the Vasa Engine Lab- oratory for four year. For the last eleven years, he has been located in Trieste, in charge of the Testing and Performance activates within Wärtsilä covering both two-stroke and four-stroke diesel and gas engines. "We have twenty-one test en- gines in our engine laboratories two of which are located in Finland, and one in
Italy, Switzerland and in Spain. The per- formance development is related to the output, emissions and efficiency of our products," Troberg notes.
Tier II enters into force quite soon.
How are your engines prepared to cope with these rules? "Our engines are Tier II compliant. We have further developed the Tier II per- formance package for all our engines which we are implementing. These have an improved performance regarding fuel consumption. Normally when you want to decrease NOx emissions fuel con- sumption increases. We have done some developments to optimize the engine for
Tier II, and are to improve the fuel con- sumption near to that of Tier I, although we have Tier II." Troberg points out that with the latest development “package” the Tier II engines of Wärtsilä will re- main competitive "as they are". "We are not going to do much upgrading on these.
We focus instead very much on Tier III.
This is a big step. Most of our product de- velopment aims at having competitive engines that fulfill the Tier III require- ments."
Wärtsilä looks at three different tech- nologies for Tier III, Troberg describes.
First there is the technology called "after treatment", which is a completely stan- dard Selective Catalytic Reactor, SCR. "Anyone can buy a standard SCR and place it after the engine. The problem with SCR is that if it is not delivered to- gether with the engine one does not re- ceive a fully optimized package. We can optimize the engine if we also supply the
SCR." Secondly Wärtsilä is looking into the engine technology. "This is perhaps the area where the main focus is within our engine R&D." The third technology promoted by the company is to use en- gines driven by natural gas, which pro- duce very low emissions. Troberg notes that there is further development taking place also on these engines. "These are the three main technologies we believe in." "The most demanding work is naturally on the engine technology side, where we have the goal to work between both Tier
II and Tier III. The engines operate some- times in a Tier II area and sometimes in a
Tier III area. A quite intelligent engine is needed to get it to function well, both on the fuel injection side and regarding the valve mechanism. This double require- ment comes from the fact that Tier III ap- plies only in ECA areas, and some ships operate in ECA areas only occasionally.
The shipowner wants an engine opti- mized for Tier III when operating in a
Tier III area and for Tier II when operat- ing in a Tier II area, as there is a definite difference in the engine efficiency. Prob- ably some day in the future all coastal areas will be governed by the Tier III reg- ulation," Troberg estimates.
Troberg presents various NOx reduc- tion technologies under development by the company, and their current ability to reduce NOx emissions. The list com- prises High Pressure 2-stage turbo charg- ing reducing NOx by some 40 percent,
Low NOx combustion tuning achieving a reduction of about 10 percent, an EGR
Exhaust Gas Recirculation system achieving a 60 percent reduction in NOx,
Charge air humidification -40 percent,
Water fuel emulsion -25 percent, Direct water injection -50 percent and an SCR system achieving a NOx reduction in the exhaust gases of some 80 percent. By using a Wärtsilä Gas engine with fuel conversion, i.e. using a dual fuel engine, a NOx reduction of some -85% can be achieved. Currently only Gas engine technologies and an SCR system fulfil
Tier III. Wärtsilä is currently develping also the following technologies to meet
Tier III, alone, or in combination: two- stage turbocharging, Exhaust Gas Recir- culation, Water Fuel Emulsion, and
Direct Water Injection. "Operational flex- ibility between different emission areas will be a success factor for the future en- gine concepts," Troberg states.
When looking at the other engine tech- nologies, apart from the SCR and gas en- gines, there is the High Pressure two-stage turbocharging where the changed combustion results in reduced
NOx gas emissions by some 40%. "Through this we have reached halfway of the Tier III requirements. In addition to this we need something else," Troberg describes. Wärtsilä is looking at various alternatives here, an SCR on the engine, an EGR system where exhaust, or as a third solution, various ways of humidifi- cation, where DWI, Direct Water Injec- tion, is one possibility, or to inject water behind the compressor. A third method is
FEATURE MARINE PROPULSION "For the client lifetime cost is what is interesting, and it is very unclear yet what these technologies will cost and which will have the lowest operating costs. Two-stage tur- bocharging gives a benefit both for NOx and in fuel consump- tion. That is why we see it as very attractive.“
Mikael Troberg, Wärtsilä
NOx reduction technologies tested by Wärtsilä. Gas engine technologies and using an SCR system enables a 80% reduction in NOx. To fulfill Tier III,
Wärtsilä is further develping two-stage turbocharging, Exhaust gas recircu- lation, Water fuel emulsion and Direct water injection.