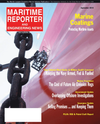
Page 35: of Maritime Reporter Magazine (September 2010)
Marine Propulsion Edition
Read this page in Pdf, Flash or Html5 edition of September 2010 Maritime Reporter Magazine
fore being resealed. The entire bulwark steel around the aft deck and stern was replaced and the Western
Machine Works towing pins refurbished with new parts. The tug’s original Burrard single drum tow- ing winch was taken back to the Burrard shop for a complete rebuild and minor updates. “”I’ve got nothing but good to say about Burrard and their winches,” said Kruse.
The accommodation areas were not neglected in the rebuilt with some bunk rooms gutted and refur- bished. The galley got a total rebuild with fine new woodwork done in house at Island Tug’s own main- tenance facility. The original concrete layer on the deck was taken up and replaced with a sound-damp- ing system that includes layers of a cork- concrete mix and perforated aluminum all topped with an acrylic flake finish.
The bridge as well as two outside control positions received updating including a new set of Cummins engine monitoring and control panels in the main wheelhouse. Additional winch controls including air- assisted power brakes were added on the flying bridge as well as the control station on the aft cabin top. Even the stack got the company’s new color scheme.
The engine room is the heart of a tug and it was here that the most significant changes took place for the Island Defender. With old main and auxiliary en- gines removed as well as the piping, it was possible to clean the interior and apply the new acrylic paints.
The existing ZF 5.037:1 gears were sent out to the
Seattle shop to be refurbished and adapted from the direct link that they had to the old engines to the new flexible link that they would have to the new Cum- mins mains. While the old engines were 1100 HP each the new will be only 500 HP each it was de- cided to keep the original gears which were hard mounted to the hull while the engines are soft mounted to reduce noise levels in the boat.
When in dry-dock at Allied Shipyards, the old
Kort 19A nozzles and their five-blade Kaplan props were removed. New Rice nozzles and three blade props were installed with the trailing edge of the nozzles cut away to allow the placement of the rud- ders within six or seven inches of the wheels for im- proved handling. In spite of the reduction from 2200
HP to just under 1000 HP total, The ownsers are ex- pecting improved performance. Bob Shields ex- plained, “According to the RAL predictive graphs, the Rice nozzles will produce a static bollard pull of 34,000 pounds and, with a 5500 ton barge, we will see seven knots loaded and nine knots empty which is an increase in efficiency of 8% over the previous setup.”
Canadian crewing regulations require a full time engineer in tugs with over 1000 HP. The reduced crewing and significantly reduced fuel consumption will contribute to increased profitability for the re- built tug. Todd Barber of Robert Allan Ltd. devel- oped re-power scenarios for three different engine manufactures taking into account capital and oper- ating costs to come up with this re-power. As the new engines are significantly lighter, the existing ballast that had been mounted inside the hull on ei- ther side of the centerline was removed and replaced with a 5.5-ton steel bar on the bottom of the keel.
The boat’s primary work will be coastal towing of 25,000 barrel fuel barges and 5500 tonne deck barges As the installation and fittings of the engine room were being finished up the high quality of workmanship became apparent as did the pride that the fitters took in the project. One of the shipyard crew protested that a photographer should wait until the job was finished “And we have all the ‘bling’ in place”. He went on to explain that there would be a good bit of bright finished metal in the immaculate engine room. The owners are well aware that their commitment to careful study prior to such a job will ultimately bring savings in capital costs (this rebuild costs are about 60% of a new build) and savings in operation with lower fuel costs and less down time.
But they also recognize the value of the pride gen- erated in the installation crew and the boat’s future crews in having superior equipment to operate.
September2010 www.marinelink.com 35 (Photo: Alan Haig-Br own cour tesy of Cummins Marine)