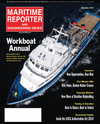
Page 38: of Maritime Reporter Magazine (November 2010)
Workboat Annual
Read this page in Pdf, Flash or Html5 edition of November 2010 Maritime Reporter Magazine
38 Maritime Reporter & Engineering News
An excellent example of how BMT Fleet Technology’s holistic approach has paid dividends is through its work with the US National Ship Research for Production (NSRP) program which is funded by the US Navy and ship building industry. These projects are focused on resolving industry specific issues and helping improve efficiency. In this case, specifically to improve the integrity of welding in both naval and commercial shipbuilding, as well as im- proving productivity rates and reducing construction costs by establishing an optimal electrode/flux combination along with single-sided submerged arc welding (SAW) pro- cedures. A combination of welding technologies were in- vestigated including the use of equipment with variable balance alternating current (AC) waveform control and tu- bular (metal cored) electrodes. Focusing on ship construc- tion panel lines that use the SAW process, welds were deposited using a tandem arc configuration, completing welds onto a flux-filled copper backing bar in steel as much as 25mm thick in a single pass. Electrode compositions were developed in conjunction with a consumable manu- facturer for welding HSLA-100, HSLA-65, and DH36 steels with select commercially available fluxes. Through manipulation of the variable balance waveform and the use of metal cored electrodes, weld metal deposition rates were significantly increased, thus improving productivity. In ad- dition, heat transfer was lower compared to conventional direct or alternating current welding, resulting in improved heat affected zone impact toughness. With the use of vari- able waveforms, arc blow was virtually eliminated result- ing in lower defect incidence rates. In a follow-on project,
BMT focused on improving the efficiency of joining lon- gitudinal stiffeners to large panels using twin-wire and twin-wire tandem SAW techniques. High speed fillet weld- ing procedures were developed to deposit 4 to 10mm sin- gle pass fillets at travel speeds of up to 230 to 165 cm/min.
These results demonstrated repeatable productivity im- provements of up to 500% compared to the conventional shipyard practice, without an increase in distortion. Look- ing to the future there is currently a lot of interest in auto- mated laser welding systems. This is technology that BMT
Fleet Technology has been involved with in its work with
Oil & Gas pipelines, however, it is transferable into the ma- rine market. In terms of speed and efficiency, it is far su- perior to traditional methods with outputs measured in meters per minute rather than the inches per minute nor- mally seen. Combined with an automated inspection sys- tem, shipyards could expect to rely on higher quality, more consistent welds that are produced faster. But the system still needs to be refined. One of the major issues that we are addressing is maintaining the speed and productivity in a range of environments. In the Oil & Gas pipeline sce- nario, exactly the same circumferential weld is completed over and over. Whereas in a shipyard there is a larger va- riety of weld types and sizes to join different shapes and sizes of material. Any increase in set-up time can easily negate the benefits of welding faster so a flexible cost-ef- fective solution is required. Optical tracking systems have been used successfully, but can often add the complexity of robotics that require large initial capital expenditure. Some of the European yards have looked at this option already but it hasn’t been widely adopted. The opportunity to im- prove both welding quality and productivity should be grasped in order to reap the full range of rewards in both new-build and ship repair scenarios. The benefits are clear to see in pure commercial terms but the change in mind-set and culture required to take a more holistic view might not be as clear cut or as palatable. The technology and skills needed to maximize the outputs from the welding value chain are all in place, it is now a case of deploying them.