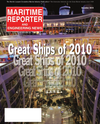
Page 27: of Maritime Reporter Magazine (December 2010)
Great Ships of 2010
Read this page in Pdf, Flash or Html5 edition of December 2010 Maritime Reporter Magazine
December 2010 www.marinelink.com 27 mained virtually non-existent. The scrub- ber automation system was able to main- tain stable parameters and 100% SOx reduction throughout all transients.
The system includes a bleed-off treat- ment unit that removes the accumulated impurities from the water used in the scrubbing process. The clean effluent from this unit is then discharged over- board. It was clearly necessary to carry out extensive water quality tests, and more than 70 samples were taken from the scrubbing water, effluent, and the technical water. Furthermore, these tests were carried out using fuel with various content levels of sulfur, ranging from 1.5% to 3.4%. Regardless of the fuel sul- fur content, the reduction level of hydro- carbons C10-C40 and the PAH (Polycyclic Aromatic Hydrocarbons), was found to be almost 100%.
Thus, considering the effectiveness of both the emissions abatement treatment, and the cleansing of the discharge water, the tests demonstrated that the Wärtsilä
SOx scrubber enables not only compli- ance with the IMOs MARPOL limits, but compliance by a very safe margin.As to the sludge generated in the scrubber process, it was found to be similar to other engine room sludge and can, there- fore, be fed to the same tank. Based upon the test results, water reception facilities in Finland and Sweden have confirmed that sludge from the scrubber bleed-off treatment unit can be safely handled, and disposed of in ports in the same way as other ship engine room sludge. The other important goals of the tests were also successfully met. Noise levels were measured at different frequencies and found to be acceptable; dedicated testing of the exhaust gas plume was carried out and during all operating conditions, the plume was very good. Above all, the sys- tem performed very well.
Wärtsilä recently released a commer- cial version of this scrubber technology to the shipping market. Known as the
Wärtsilä Exhaust Gas Scrubber the unit is designed to completely eliminate sul- fur emissions and reduces particulate matter up to 60%. The engine feeds the exhaust gas to the SOx scrubber. The system is based on a closed-loop fresh water scrubber to which sodium hydrox- ide (NaOH) is added as a means of neu- tralizing the SOx emissions. Seawater is used for cooling. The small bleed-off ex- tracted from the loop is cleaned, and thus all quality and monitoring requirements stipulated by the IMO are fulfilled. The cleaned effluents can be safely dis- charged overboard with no harmful im- pact to the environment whatsoever.
Naturally, if zero discharge operation is necessary, the effluent can be led to a holding tank for later discharge. The scrubber unit consumes technical fresh water that evaporates into the atmosphere with the exhaust gas. This evaporation is minimized through the use of the scrub- bing water cooler.
A major benefit is the fact that prior to the introduction of this scrubber technol- ogy, the only option was to use low-sul- fur fuel. The price premium for such fuel is expected to rise as new sulfur limits are enforced, not only in SECA parts of the world but for global operation out- side SECA. With effect from 2012, the global sulfur limit will be lowered to 3.5%, and from 2020 it will be further re- duced to 0.5%. In Emission Control
Areas, the limit is currently 1%, and this will be drastically reduced to a maxi- mum of 0.1% in 2015. In EU ports, as from 1 January 2010, ships scheduled to be at berth for more than two hours are not allowed to use fuel containing more than 0.1% sulfur. This restriction applies for both diesel engines and oil-fired boil- ers. The Wärtsilä scrubber offers a very viable alternative to the use of such fuel.
The Wärtsilä Exhaust Gas Scrubber en- ables cheaper heavy fuel oil (HFO) to be burned in all these areas as a low cost al- ternative to buying the increasingly ex- pensive low sulfur fuel. The Return On
Investment (ROI) is in the range of one to three years, and for larger installations, even less.
Figure 2:
IMO Sulphur limits for years 2008-2020 (% mass).