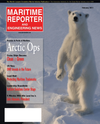
Page 9: of Maritime Reporter Magazine (February 2011)
Cruise & Passenger Vessel Annual
Read this page in Pdf, Flash or Html5 edition of February 2011 Maritime Reporter Magazine
demand in shipbuilding has declined; Globalization; and
Environmental Awareness. • The demand in shipbuilding has declined: Although demand in the shipbuilding industry declined sharply dur- ing the past year, the demand for Alfa Laval’s specialized products, parts and services for ships will continue in the future. Separators used to clean fuel before it enters the vessel’s engines and heat exchangers that produce fresh- water are two of many examples. Our S and P separators to create a dual approach to fuel and lubrication oil treat- ment; the Eliminator for lube oil filtration is a full-flow back flushing system that bolts directly to the engine – eliminating cartridge filter disposal. Our onboard and land-based desalination units convert seawater into fresh- water for the supply of high quality freshwater for domes- tic and process utilization. PureVent cleans the gas vented from engine crankcases to remove oil mist and other par- ticles. Our ballast water treatment system offers chemi- cal-free treatment that protects against the threat of invasive species, while staying true to the essentials of life on board: safety, efficiency, simplicity and ease of use. The system is available in an Ex version for potentially explo- sive environments. Our solutions are designed to meet and exceed rules and regulations. • Globalization: Globalization has progressively intensi- fied over the past century. With locations all over the world, Alfa Laval is ready to serve wherever – and when- ever the customer requires – 24 hours a day, 7 days a week, 365 days a year. • Environmental awareness: Demand for Alfa Laval’s products is governed by an increasing need for energy-ef- ficient solutions for various types of processes. Demands for efficiency have resulted in a technology shift, where our core competencies of heat transfer, separation and fluid handling provide the solution. Our equipment and sepa- ration systems not only take up less space, they also re- duce energy consumption and emissions, enabling a payback period that is often well under one year.
What do you count as the top challenges to expanding
Alfa Laval’s market penetration?
The marine industry is global by nature, so those chal- lenges that some companies face are opportunities for us.
We serve ports worldwide – with field and customer serv- ice available 24 hours a day, seven days a week to support our customers when and where they need it. We like to call it “glocal” – global and local service.
Discuss a few case studies which you think best exemplify your company's range and success.
Well, a few cases come to mind that give a snapshot of not only our commitment to optimizing the customers process, but also our commitment to promote a sustainable envi- ronment. Recently we received a PureBallast order for a demanding naval application. This particular order involves two PureBallast systems for the Royal Aus- tralian Navy – confirming that PureBallast is fully ca- pable of meeting the strict requirements of naval applications. The two Australian systems are the first
PureBallast installations for naval use, and are fitted aboard the Australian LHD (Landing Helicopter Dock) vessels built by Spanish shipyard Navantia Ferrol. Vessels of this type, which allow flexible deployment of smaller land vehicles and helicopters, are of strategic interest as
Australia and other nations shift their military focus from territorial defense to international response and peace- keeping operations. Each has a treatment system flow of 250 cu. m./hr. We worked together with a prominent barge company in the US to design, test and outfit their full fleet with fuel and lube oil purification, crankcase gas cleaning, and heat transfer solutions for full optimization of their processes and costs. These solutions also eliminated the high cost of maintenance – and greatly reduced the related man-hours. In combination with the company’s focus on the concept of imparting zero harm, they also wanted to achieve a solution that posed fewer risks to the environ- ment. By eliminating cartridge filter disposal, reducing engine emissions by removing oil and particles from crankcase gas, and optimizing the engine room – the barge company achieved their goal for optimal cost and process efficiencies while supporting a sustainable environment.
AlfaLaval PureBallast2 system.