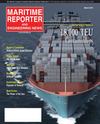
Page 48: of Maritime Reporter Magazine (March 2011)
Ship Repair & Conversion
Read this page in Pdf, Flash or Html5 edition of March 2011 Maritime Reporter Magazine
48 Maritime Reporter & Engineering News
FEATURE SOFTWARE SOLUTIONS communication (i.e. phone, SMS, email, etc.) and paper-based documentation. As well as helping to connect buyers with new suppliers and vise versa, our prod- uct streamlines the traditional bunker procurement process, making it faster, easier and greatly reducing the potential for errors throughout the process.
In your estimation, what has been the biggest driving force for the utilization of
IT solutions onboard ships?
Carbone, Ship Decision Across most industries, we are experiencing unprece- dented levels of innovation in terms of applying new technologies to business challenges. Operating a ship has so many complex operational, safety, logis- tics, and regulatory elements that it is a logical step to see Ship Owners adopt technologies to support these complex functions.
Büssow, GL In the past the main driver has been, from my perspective, regulations, e.g. a different class survey- ing procedure for machinery items, if you deploy a planned maintenance system.
This is changing step-by-step: As in other industries shipping companies see soft- ware solutions as a way to improve their performance and competitiveness in striving to increase quality, speed and ef- ficiency of operations. This is also sup- ported by a younger management generation coming into responsibility today, which is naturally much more technology prone.
Hughey, ABS NS Companies are reaching out to IT solutions for man- aging information related to perform- ance, safety and environmental compliance. Having systems that pro- vide this capability is a must for today’s ship operators.
Galatas, Marine CFO In my opin- ion the regulatory environment is the biggest driving force. Companies can no longer rely upon open ended systems to manage things like crew training, crew certifications, vessel certifications, inci- dents and maintenance. Management must have up to date information that gives them the comfort that all of these items are in compliance and are easily re- ported to stakeholders and regulatory bodies. In fact, we recently had a client who was awarded a job, in part, because of the safety auditing functions within
MarineCFO. It is the ultimate compli- ment to our product when we can be a differentiator for our client’s businesses.
Sheldon, Veson Traditional ship-to- shore communications often prevent shipping operations from running effi- ciently. In an environment where current information is vital to profitability, much data sits idle due to stunted communica- tion. Companies that employ IT solu- tions are able to capitalize on a constant stream of up-to-date activity reports.
How are you investing today in your product(s)?
Carbone, Ship Decision I mentioned earlier that Stelvio's full-time, in-house development team is taking advantage of the most up-to-date Web development tools in order to build easy-to-use soft- ware that gives users a positive experi- ence. We have a few exciting developments underway that will be an- nounced in the months to come, some of which are ship-based.
SpecTec
Giampiero
Soncini
I am still confronted on a daily basis with people who simply do not want to use software for their daily activi- ties, while they use it every day at home! I feel like saying to them:
Wake up! We are in 2011, not 1911!
Veson Nautical
Jamie
Sheldon
It is for this reason that we devel- oped Veslink Offline Forms, a sys- tem that enables the transmission of material voyage data from ship to shore but does not require software installation aboard each vessel.
By Niels Lorenzen, Canfornav Inc.
As an Operator at Canfornav, I spend a great deal of time monitoring voyages and intervening to prevent problems.
Our company uses web-based technology to manage our day-to-day business. Because the system is web-based, our Operations and Chartering departments can log into it anywhere, any time.
To run our business we must exchange hundreds of emails every day with our business partners around the world. The ShipDecision message center allows us to manage these emails with optimum efficiency. Each of our operators can place his or her vessels on a “Watched
List”. For example, I am alerted as soon as information is received regarding my ships. Before, we each had to sort through hundreds of operations emails to see what was happening with the vessel we were managing.
Watched messages can also be transferred automatically to our smart phones, so we can respond to issues no mat- ter where we are. On the weekend we really appreciate this.
When we are alerted that a dispute has happened, we can immediately log into the system, access the information we need, and take corrective actions. Here’s an example.
On the Labor Day weekend we had the M/V Ruddy load- ing a cargo of urea in Venezuela.
The operator received a message from the Master on his
Blackberry. At the safety meeting prior to commence- ment of loading, the shippers presented the Master with their usual safety memorandum to sign. It indicated the cargo quantity to be loaded as 22,500 MT. The operator for that vessel logged into ShipDecision. He went to the
Cargo Menu, and was able to review the Charter Party confirming the quantity booked was 25,000 MT/10% more or less owners option. Under the Charter Party there was no option for the Charterer to load a lesser quantity at an increased freight rate.
Because our operator could access this information im- mediately, from home, he was able to take corrective ac- tion. The Master was advised to sign the memorandum “For receipt only, without prejudice to the terms and con- ditions of the Charter Party.” He was also instructed to issue a letter of protest and deadfreight letter on com- pletion of loading. The Charterers were immediately ad- vised of the situation and put on notice.
The example I just gave highlights how immediate ac- cess to the right information helped us manage this situ- ation with minimum delay, while securing our interest.
Because ShipDecision was designed to mirror the way we work in the Maritime industry, the tools inside the system are really practical.
I mentioned the Cargo Menu. It has vastly improved
Canfornav’s ability to share information between Char- tering and Operations. All fixtures are inserted into
ShipDecision, including a copy of the “recap”, the base
Charter Party, and finally the original Charter Party. Op- erations has instant, on-line access to this information.
No more looking for files or searching documents in fil- ing cabinets. When we access our Contracts of Af- freightment in the system, we have immediate access to relevant details. We can see at a glance what liftings have been completed, what is in progress, as well as the planned liftings. There is a lot more to the system than what I have described in this brief case example, but the point I want to make is…having immediate access to ac- curate information, when and where we need it, has be- come invaluable to our business.
CASE STUD
Y
Ship Decision