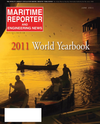
Page 22: of Maritime Reporter Magazine (June 2011)
Feature: Annual World Yearbook
Read this page in Pdf, Flash or Html5 edition of June 2011 Maritime Reporter Magazine
22Maritime Reporter & Engineering News Todays vessel owners and operators continue to adopt the latest equipmentonboard their ships. Battery and drive technology for hybrid propulsion, ad-vanced navigation and bridge systems, dynamic positioning systems, diesel elec-tric propulsion, new HVAC technology, electronic fuel injection and valve con- trol systems, shore power connections systems and ballast water management systems are just a few of the new, emerg- ing technologies that lower energy con- sumption, comply with new regulatory measures, reduce emissions or increasecrew and passenger comfort and safety. However, the addition of these technolo- gies creates a new challenge: What does it take to keep the equipment in service? This question is critical to each vessel, and disoperation may force a ship to re-main idle until addressed. Consequently, servicing and maintaining the new tech- nology becomes of paramount impor- tance to the onboard crewmembers who are not as familiar with the new equip- ment. The challenge is even greater for port captains and superintendents whoare required to manage entire fleets invarying worldwide locations where each vessels on-board systems differ. For ex- ample, our customers have asked us if we can support their marine needs when avessel is operating in hard-to-access lo- cations such as the West coast of Africa. Such requests present a unique challengeto all suppliers. To best serve our cus- tomers, we, too, need new technologies, tools and processes to support their crews and our equipment as they travel around the world. Higher bandwidth, low cost satellite technologies enable many of these new service tools, such as remote monitoring.Remote monitoring allows a vendor to dial-in? to a system remotely to provide diagnostics. A proper remote monitoring system only allows an operator to access on-board systems if the crew first grants access. Once the vendor has access, a land-based expert can review the ships issue and provide trouble-shooting ad- vice to the crew. The owner benefits from the vendors ability to access the vessel regardless of its current location. Additionally, real-time advice is faster, more practical and far less expensive than sending a service technician to the ves- sels location. This will keep a ship on charter instead of heading back to port.A similar benefit may result by deploy- ing built-in diagnostic and condition- based monitoring software. Both systems observe the usage, operational and per- formance data and product health. While the built-in diagnostics only look at the product, condition-based monitoringsoftware can monitor multiple products or systems, as well as ancillary-relatedprocesses. Before a problem arises, the software alerts the crew so preventative action can be taken before a problem oc- curs. For example, the system will alert the crew if a temperature threshold or a predetermined number of operatinghours has been exceeded. Some vessels may have multiple products and applica- tions that use different condition-based monitoring systems. Diesel generators, for example, may be on one system while the propulsion equipment may be on an-other. Additionally, the vessel could have other programs such as a fuel consump-tion monitoring system. Having many programs often requires various com- puter platforms to host the programs, inaddition to multiple access points on thevessels systems. An event could cause alerts from each of these programs,which may hinder the crew from isolat- ing the root cause of the problem. One solution to consolidate the multiple pro-grams is to use an on-board data concen-trator. This concentrator becomes the sole platform to host multiple programsand provides the crew with just one view. It also gives access to a land-based ven- dor or ship superintendent. To assist land-based personnel, fleet- based data concentrators are also avail- able. A fleet-based concentrator ag- gregates data from multiple vessels. This allows real-time comparison of usage, performance and condition data acrossthe fleet. A superintendent can then share best practices between crew. For exam- ple, he can compare fuel consumptionacross a fleet, or multiple vessels, with comparable operation profile, voyage plan, etc. to help him determine whatmakes one vessel more efficient than oth- ers. As a result, the operator can uncover these differences, enabling him to imple- ment corrective actions and best practices across the fleet. Condition-based moni-toring and data collection also helps op-erators by extending time between dry-dockings. By analyzing various per- formance data, the owner can potentially fine tune his vessel profile and equipment performance to extend time between dry dockings. Classification society concerns can be assured with real-time data, frombottom paint performance to enginecylinder health. These tools are not the only ones thatdepend on advancements in satellite communication. Because the cost to transmit large files has decreased, online access to existing information can now be made available to crews. Vendors can, and do, offer dedicated, password-re- stricted websites that hold vessel-specific information for crews. Typical stored in- formation includes technical drawings, a list of parts, instruction manuals or back-up copies of software programs. Vendors can also keep databases that track issues, changes and solutions for a vessel and fleet. A ship owner can eas- ily transition this valuable data service history from crew to crew. This informa- tion sharing benefits new crews who can use it to explain to a service engineer how a recurring problem manifests itself. A port captain can then use this informationto highlight fixes or track ongoing prob- lems to others in the fleet as vessels travel between service areas. For example, a vessel may have an intermittent issue that takes a generator off-line. The database will highlight the problem to a vendor and allow the operator to document the issue and occurrences. Quick access todrawings, back-up programs or details on previous issues with corresponding reso- lutions will help the crew resolve issues quickly and accurately. In addition to these new tools, vendors can broaden existing processes to address some of the challenges of new technolo- gies. These methods are standard best practices that have proven to increase vessel availability. One involves the use of service personnel during commission-ing, sea-trials or classification acceptance tests. During this time, the service tech-nician becomes familiar with the vessel and the crew begins to forge a relation- ship with the service technician. Once the commissioning or trials are done, theservice employee now has thorough knowledge of the ship he is servicing, and he has also cultivated a strong rela- tionship with crewmembers, who are now assured of his expertise. More im- portantly, the service technician can as- sist the crew in becoming more familiar with new equipment and provide practi- cal usage and service training. If a crew is operating its first diesel electric propul- sion vessel, the service engineer can, for example, show the crew how the power management system operates, as well ashow to access parameters on the propul- sion drive. These activities can also be part of an overall training plan, which typically in- cludes land-based education performedin a classroom setting at an operator fa- cility, shipyard or vendor facility. Such training involves the use of operation and programming guides, as well as hands-onteaching, to facilitate discussion points so the crew understands vessel operations. The crew can be trained on how a diesel electric system operates, how to start a generator or how to set up a switchboard. COLUMNOPERATIONS Keep Your Vessel in Operation About the AuthorsDavid Grucza is BusinessManager for Siemens MarineSolutions USA. Contact [email protected].(Continued on bottom of page 24)