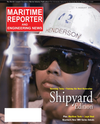
Page 43: of Maritime Reporter Magazine (August 2011)
Top 20 Shipyards of the World
Read this page in Pdf, Flash or Html5 edition of August 2011 Maritime Reporter Magazine
By Edward Lundquist Apprentice training programs are vitalto ensuring a qualified workforce for the future, according to shipyard industry ex- perts.The BAE Systems apprenticeship pro- gram is a four-year program, conducted in partnership with Tidewater Commu- nity College (TCC). ?We have a robust program at our Nor- folk yard, which we?re looking to ex- pand,? said Joe Chopek, maritime communications manager for BAE Sys- tems Ship Repair in Norfolk.The apprentices are part-time students.During the day, they work the first shift in their prospective trade. They receive a Career Studies Certificate Maritime Technologies and are certified as a jour- ney mechanics (first class) in their trade at the end of the four years.The graduation rate is high, saidChopek, and so is retention of those whohave participated in the program. ?Since 2008 we have graduated 53 ap- prentices of which 47 are current em-ployees,? he said. ?Of note, 24 have been promoted to leadership positions sincegraduation.? ?We have seven senior people on our staff at Norfolk who have graduated from our apprentice program in the 70s,? he said. ?For some of them, working in our shipyard is the first and only jobs they?ve ever had.? Retaining qualified talent is vital, he said, especially in the boom-and-bust cy- cles of the shipbuilding and repair indus- try. ?The talent pool in the skilled trades is shrinking. Their skill level is high enough that they can and will go else- where. You don?t get them back. That asset is lost.? Some lower skilled jobs inside the yard, like fire watches, are subcontracted, and temporary workers can be brought aboard for a surge. You want to keep your core workforce intact,? Chopek said. Chopek said his company has an older workforce. The average age is 50 in Nor- folk, and 48 for the BAE Systems yard in Mobile, Ala. This is a problem through- out the industry. It?s not just a matter of replacing people one-for-one when they reach the end of their career. ?As these people approach retirement age, how do you replace someone with 30 years ofskill in a trade??Recruiting workers is one thing, but qualifying them is another. ?People can't just get hired to go towork in a shipyard. They have to be trained so they can be productive and are not a danger to themselves or others in what can be a dangerous work environ- ment,? Chopek said. ?A physical exam is required due to the demanding physical requirements of the job,? he said. ?Also, apprentice candi- dates are required to complete a physi- cal qualification test that simulates physical demands presented daily on the job (ladders, stairs, lifting, confined space entry/exit, etc) ? this may be applied to entry-level hires at all locations in the fu- ture as we continue to recruit and trainour future workforce.? Chopek said BAE Systems employees attend a full day of orientation of whichapproximately 4 hours is specific to safety and the hazards of working in ship repair. ?For apprentices, they are in ori- entation for the first one to two weeks as they are exposed to and begin training in basic tool usage, procedure training andtrade orientation. In addition, all em-August 2011www.marinelink.com 43Apprenticeship Training Programs Shipyards make long-term commitment to start employees on the right track LEFTLauryn-Mae Pang is an appren- tice crane mechanic at PearlHarbor Naval Shipyard. (Photo by Kathryn Vanes) ABOVE, RIGHTNewport News shipbuilding Ap- prentices Benjamin Price, Don- ald Rickerson III. (Image: HII)MR Aug. 11 # 6 (42-49):MR Template 8/3/2011 10:55 AM Page 43