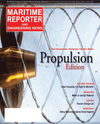
Page 48: of Maritime Reporter Magazine (September 2011)
Marine Propulsion Annual
Read this page in Pdf, Flash or Html5 edition of September 2011 Maritime Reporter Magazine
Upon completion of the jacking mode,the system is secured in the elevated mode for operation. The jacking system is stopped, the brakes are set, and the leg locking system is engaged. The cabling is brought on board using an industrystandard J-tube installed in one of thelegs. Since the water has been removed from inside the legs, the J-tube and cable splice remain fully man-accessible. All opera- tional systems are thoroughly checked out before the turbine blades are un-teth-ered and released.The jacking system and echo soundingequipment are removed and put back on the boat to be returned and used on thenext installation. In the event the legs set- tle further into the soil over time, the jacking system can be reinstalled and theplatform leveled. E FN SSEM The Titan?s patented lifting jacks are designed to be removed and reused on other platforms. Therefore, only one or two sets of jacks (leased to the developer) are required for installation of the windfarm. After completion of the wind farm, it will only be necessary to retain one setof lifting jacks for long term maintenanceof the site.DMENSNS The Titan platform is structurally de- signed to carry significant loads under extreme conditions. The structural integrity of the platform is carried through the plates of the steelhull with load bearing members placedinside at spaced intervals. The legs are designed with cross members spaced in-side the leg from top to bottom. These cross members resist deformation of theleg so the lifting jacks always remain in position for the lifting pinions. The height of the legs is determined by the water depth of the site. DC SDE ASSEMB Final assembly of the Titan is per- formed in a boat yard closest to the loca-tion of the wind farm. This work includes integration of all sub-system components, assembly of the platform,and test and verification. The Titan is fully certified prior to installation of the wind turbine, which also occurs on thedock.All of this assembly work provides jobs for the local community. Wind turbines up to 10 MW can be ac- commodated in the current Titan design. The turbine is assembled on the hull andfully erected before the system is floated.Thus, all construction is performed usingland-based lifting equipment. ENNMENA MPAC The Titan presents the lowest environ- mental impact of any offshore founda- tion.No seabed preparation is required. Nomooring lines are used that could intro-duce an unwanted haard to whales or other migratory sea life. There are no piles, so decommissioning leaves no steel embedded in or lying about on the seafloor. There will be no underwater cutting or demolition. There is no need for concrete on the sea floor, so no cleanup will be re- quired.CS ADANAES When the Titan was submitted to the UK Carbon Trust as a contender for ound , the economics showed it to be very favorable. The cost per megawatt based on a 5 MW turbine in 5-5 meters of water falls well within the range of the Carbon Trust?s goal for innovative and af- fordable solutions (0.8 M USD/MW). There are several comparative cost drivers that should be examined that demonstrate a solid business case for the Titan. These include lower installation costs, shorter project timelines, reducedliability insurance, elimination of prepa-ration and stabiliing materials, fewer de- commissioning expenses, the ability to make repairs, and competitive fabrication costs. Installation of the Titan and wind turbine can be completed without theneed for expensive specialied vessels. A standard service vessel may be employed to tow, carry supplies, parts, and person- nel back and forth. The elimination of all specialied construction vessels repre- sents a significant cost savings to the project. The Titan?s ability to take on bal- 48Maritime Reporter & Engineering News FEATURE OFFSHORE WIND