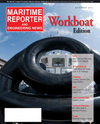
Page 85: of Maritime Reporter Magazine (November 2011)
Feature: Workboat Annual
Read this page in Pdf, Flash or Html5 edition of November 2011 Maritime Reporter Magazine
type of gasket to be used. Spiral-wound, reinforced sheet and corrugated metal gaskets are all available with various sealing elements and differ functionally in terms of required gasket stress to effect a seal and the maximum pressure the gas- ket is able to seal. Made by winding alternating strips ofmetal and softer, more compressible filler materials, spiral-wound gaskets were de- veloped to provide improved perform- ance in high-pressure applications. The metal windings are made of various grades of carbon steel, stainless steel,nickel and titanium. The filler elements are usually graphite, ceramic or PTFEmaterials, and are based on the tempera- ture and chemical resistance require-ments of the application. Graphite/stainless steel spiral-wound gaskets are suitable for marine exhaust systems, provided the available bolting and flange configuration can produce suf- ficient gasket stress. Minimum recom- mended stress for these gaskets is 10,000 psi, the highest of the three types underconsideration. Also suitable for marine exhaust sys- tems are reinforced graphite and ceramicsheet gaskets. The reinforcement ele- ments in these gaskets usually consist of various configurations of stainless steel foils, as well as tang and wire mesh in-serts. Both sheet and corrugated metal gaskets require less bolt load than spiral- wound gaskets since there are no metal windings to be compressed. Minimumrecommended stress for reinforced sheetgaskets is 5,000 psi. Corrugated metal gaskets combine a metal core with a compressible sealingelement. A variety of metals is available for the core, and either graphite, PTFE orceramic-based materials may be used forthe sealing elements. Corrugated metal gaskets conform to flange irregularities even under low bolt loads, and can be used when the space between the flangeswill not accommodate a spiral-wound gasket. Minimum recommended stress for this type of gasket is 3,600 psi. Gasket Type Minimum Stress RecommendationSpiral-wound 10,000 psi Reinforced sheet 5,000 psi Corrugated metal3,600 psi INSTALLATION It is important to note that previously compressed gaskets, as evidenced by an imprint of the flange, should not bereused. Having been compressed, they will not recovery sufficiently, resulting in premature loss of bolt load. In additionthe flange bolts should be well lubricatedand flat washers hardened. Liquid or metal-based anti-stick and lubricatingcompounds should never be used on the gasket. During installation the gasket should be compressed uniformly by first hand tight- ening the bolts, then going side to side onthe flange, applying load to the bolts witha torque wrench (Figure 3). It is recom-mended that the bolts be tightened in one-third increments with the final pass at the target torque value made consecutively from bolt to bolt. A final check and re- torquing can be made 12 to 24 hours afterinstallation. CONCLUSIONUnder certain circumstances, OEM-supplied graphite gaskets may be suitable in exhaust systems for new engines with limited vibration. However normal wear and tear over time can result in failure and leaking joints, the fumes and noisefrom which can adversely impact the safety and comfort of crew members and others. These leaks can be avoided by taking into account the state of the equip-ment and the operating conditions of thesystem when selecting the sealing solu-tion. Limited temperature resistance andresiliency will effectively eliminate graphite from being used in systems thatexceed its capabilities Graphite oxidizes at different rates, depending on its purity and the use of doping agents to inhibitoxidation. Testing demonstrated the sus- ceptibility of graphite to oxidation at arelatively low temperature. These test re- sults combined with actual failures of graphite gaskets in service indicate the need to consider alternative sealing ma- terials such as ceramics to withstand theextreme temperatures in marine exhaust systems.ABOUT THE AUTHOR Wayne Evans is Product Development Engineer & Sherwin Damdar, SeniorProduct Engineer, Garlock Sealing Tech- nologies 3030 E. Pershing St.Appleton, WI 54911 [email protected] Phone: (920) 738-5432Fax: (920) 738-5435Visit Booth #530 at the 2011 International WorkBoat Show November 2011www.marinelink.com 85The installation of reinforced ceramic sheet gasketing in the exhaust systemof the 225-ft. (68.6m) yacht Attessaafter spiral-wound graphite gasketsoxidized and caused leaks. MR Nov.11 # 11 (82-88):MR Template 11/7/2011 10:58 AM Page 85