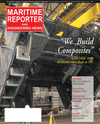
Page 26: of Maritime Reporter Magazine (January 2012)
US Navy Report
Read this page in Pdf, Flash or Html5 edition of January 2012 Maritime Reporter Magazine
26Maritime Reporter & Engineering News NAVY REPORT FEATURE Composite materials are used tomake cars, planes and boats, and have been used to build minesweepers and small surface combat- ants. Now, the largest composite struc- ture ever built?the DDG 1000 destroyer deckhouse?has been fabricated in Mis- sissippi and is being shipped to Maine forassembly aboard the future USSZumwalt (DDG 1000). In this dramatic example of a ?shared build,? General Dynamics Bath Iron Works is the lead yard, but the super- structure and hangar are being built at Huntington Ingalls Industries (formerly Northrop Grumman Ship Systems) Com-posite Center of Excellence at Gulfport,Mississippi. The composite deckhouse, which sits upon a steel base fabricated at HII?s Pascagoula yard, will be placed on a barge and transported to Bath by sea, a transit of more than 2,000 nm. The deck- house is being built at HII to take advan- tage of the Gulfport facility?s unique capabilities with composites.?We?re a fabrication yard,? says Donny Dorsey, director of operations at Hunt- ington Ingalls Industries Composite Cen- ter of Excellence in Gulfport, Miss. ?We don?t build ships. We build composites.? Dorsey says the facility builds large ship structures using fiberglass and car- bon fiber, as well as core materials such as balsa wood. According to Jay Jenkins, the HII sitedirector at Gulfport, the company is using the Vacuum Assisted Resin Transfer Molding (VARTM) process for the DDG 1000 deckhouse involving carbon fiber fabric, balsa wood, synthetic foam and a resin system. ?We place layers of carbon fiber cloth over the balsa core, then seal with a plas- tic vacuum bag connected to the resin system. When we evacuate all the air and pull a vacuum on the bag, it draws resin in,? says Jenkins. ?When the material is saturated the resin undergoes a chemical transformation and cures while inside thevacuum bag.? Jenkins says this process can be usedfor various sized objects. ?We can do big decks, including 150x50 foot flat panels.We can use curved molds, or create ver- tical structures. We can build a hull up to 300 feet with composites.? He says composite structures with thesame strength are half as heavy as steel and a quarter to a third as heavy as alu- minum. Less topside weight improves stability and has speed and fuel efficiency benefits. Plus, it doesn?t fatigue and won?t crack or corrode, and you don?t have to paint it. ?Lifecycle costs are dra- matically less,? Jenkins says. ?The biggest benefit is weight,? Dorsey says. ?Composites also allow a lot of op- tions for shapes, and gives you the ability to place systems in the structure, such asantennas, as you fabricate it. You can?t do that with steel or aluminum.? In fact, a main feature of the DDG 1000 deckhouse is that the antennas?or aper- tures?are embedded directly in thestructure itself.The deck house is covered with radar absorbing material. Altogether, with the many ways the DDG 1000 design re- duces signatures, this 14,000-plus tonship has the radar cross section of a smallfishing boat. VERSATILE CAPABILITY ?We can make large units from com- posites. We build them inverted, so we?re working hands down, which is best for the craftsman,? Jenkins says. ?The deck- house will be about 900 tons. Thehangar will be almost 200 tons and is60 feet from side shell to side shell. The hangar is the largest unsupported space ever built for a ship. When com-plete, we turn them over and get them ready to be shipped to Maine.? When major sections of a ship are built at two different yards, it?s important that the modules are fabricated to exacting specifications to ensure a proper fit. ?Working with composites allows us to be very precise and accurate,? he says. ?We build to a tolerance of 3 mm or less ( 1/8th in.). Steel ships have precision to about a half inch. Our accuracy control people are very busy measuring with lasers.? The Gulfport facility has built mine hunters for the U.S. Navy as well as com- posite masts. Jenkins says the Gulfport facility is uniquely capable and qualified to build large modular structures, such as deck- houses for combatants.?We are also building the forward and after masts for theUSS San Antonio-class (LPD 17) of amphibious ships. These are essentially radomes, where the antennasDDG 1000 composite deckhouse nearing completion. by Edward Lundquist ?We Build Composites? (Photo: Huntington Ingalls IndustriesMR Jan.12 # 4 (26-33):MR Template 1/17/2012 10:50 AM Page 26