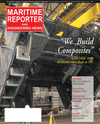
Page 28: of Maritime Reporter Magazine (January 2012)
US Navy Report
Read this page in Pdf, Flash or Html5 edition of January 2012 Maritime Reporter Magazine
28Maritime Reporter & Engineering News NAVY REPORT FEATURE cial kind of wood. It is imported from Ecuador, and comes in different densi- ties?12, 15 and 20 lbs. per cubic foot.?We use the denser wood where we need greater stress resistance,? Jenkins says. ?We can make large units from com- posites. We build them inverted, so we?re working hands down, which is best for the craftsman,? Jenkins says. ?The deck- house will be about 900 tons. The hangar will be almost 200 tons and is 60 feetfrom side shell to side shell. It?s the largest unsupported space ever built for a ship. When complete, we turn them over and get them ready to be shipped toMaine.? ?Working with composites allows us to be very precise and accurate,? he says. ?We build to a tolerance of 3 mm or less ( 1/8th in.). Steel ships have precision to about a half inch. We do a lot of work with our accuracy control people meas- uring with lasers.? Because the carbon fiber is black, it?s not possible to see imperfections such asbubbles or a place where the cloth didn?t bond, Jenkins says every item fabricated at the plant is inspected with ultrasound. LARGE SCALEThe HII Gulfport facility is an environ- mentally controlled facility. ?To build composites you need to control tempera- ture and humidity,? says Dorsey. ?But?s also a great work force benefit, because it can be hot and humid in Alabama, es- pecially in the summer.? It?s like any other composites facility, Dorsey says, but to a large scale. For ex- ample, the center boasts the world?s largest computer numerically controlled (CNC) saw. HII found that qualified workers for composite structures were not easy tocome by. All employees receive three weeks of classroom training, and they?re tested before they are allowed out onto the shop floor. The company also established a U.S. Department of Labor Certified Compos- ite Apprentice Program. ?You can find people with the right skill sets, but if you?re doing something that hasn?t been done before you can?t just go hire them,? Dorsey says. ?You have to train them.? When the company had difficulty find- ing people with experience fabricating ship sections, they realized they had an untapped market. Since much of the work with composite structures involves the wood core, HII started recruiting peo- ple with carpentry experience. Since the housing market was depressed in the Gulf Coast region, people who were skilled with working with wood were available. The first two DDG 1000 deckhouse and hangar assemblies are in production, with the third?DDG 1002?now under con- tract.The future of the facility is unclear. Originally planned as a class of 32 ships,then 24, then 7, the Navy finally decided to build just three Zumwalt-class de- stroyers.. ?The business case for this fa- cility is seven,? says Dorsey. "The Gulfport facility is a national asset in terms of composite capability and ca-pacity,? says Karrie Trauth, Ingalls Ship- building's DDG 1000 program manager. Our shipbuilders continue to prove this on a daily basis with the significant work they are performing in composites for U.S. Navy shipbuilding programs.? (Photo: Huntington Ingalls IndustriesMR Jan.12 # 4 (26-33):MR Template 1/9/2012 4:15 PM Page 28