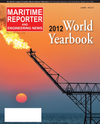
Page 10: of Maritime Reporter Magazine (June 2012)
Annual World Yearbook
Read this page in Pdf, Flash or Html5 edition of June 2012 Maritime Reporter Magazine
10Maritime Reporter & Engineering News On May 29, 2012, SINOPACIFIC Shipbuilding Group held an introductory meeting and social gathering in Athens, pro- moting what it dubs its new series of ?Ultimate Fuel-Saving? bulk carriers, the CROWN 63, CROWN MHI 82 and CROWN 121 designs which aim at the segmented markets for 60,000, 80,000 and 120,000 DWT bulk carriers respec- tively. At a service speed of 14.3-knots, the fuel consumption ofCROWN 63 Ultramax bulk carrier is reduced to 25.8 tons/day, reduced by 13% compared to the CROWN 58 (58,000DWT) bulk carrier, achieved using a combination of hull form design and propulsion system innovation (larger di- ameter & lower rotate speed propeller and the electrically controlled main engine).The CROWN 63 has already been built and delivered (the first in March 2012 + three sisterships to Greenship Singa- pore), and has won BV?s first global EEDI (Energy Efficiency Design Index) designation. Based on the attained EEDI stage 2 value of the ship, it has achieved a reduction factor of up to 20% making it eligible to a serious reduction in Initial Reg- istration Fees as well as Annual Tonnage Tax rebates until December 31, 2019.? The CROWN MHI 82 (82,000DWT) is a bulk carrier jointly developed by SINOPACIFIC and Mitsubishi Heavy Industries, Ltd. (MHI), a collaboration which was announced earlier this year. The tank test of the CROWN MHI 82 will be performed in the mid-2012. The overall joint design project is expected to be completed in the second half of 2012. The CROWN 121 (121,000DWT) Mini-Cape bulk carrier is an upgraded CROWN 118 (118,000DWT) bulk carrier in- dependently developed by SINOPACIFIC. With V-bow and MAN G-type main engine, the fuel consumption of CROWN 121 is reduced to 38 tons/day from a former 49.1 tons/day, a drop of 23% while DWT is at the same time increased. VESSELSDamen Delivers ... AgainDamen Shipyards announced that it launched the first of its newly designed StanPontoon (SPo) 12032. The SPo 12032 isthe longest pontoon ever built by Damenand part of a series of 34 pontoons cur- rently being built. In addition, Damen Pon- toons & Barges has started building a second new design: the Damen CraneBarge (CBa) 6324, a transshipment barge for handling dry bulk and container opera-tions. The 120 m x 32.2 m Stan Pontoonwas launched at Jiangsu Ganghua Shipyard, one of Damen?s Chinese partner yards. With a deck strength of 20 t/sq. m., its heavy duty deck is suitable for heavy RoRo opera-tions. The pontoon?s ballast system includes Econosto valves and Azcue pumps. Further- more, the SPo 12032 is equipped with two DMT-winches, a Van der Leun electrical sys- tem (incl. a Caterpillar generating set), anInternational Paint system and it is classifiedunder Lloyd?s Register. New Damen Crane Barge Damen?s newly designed crane barge is called the CBa 6324. It?s a shallow draft transshipment barge (optionally self-pro- pelled) able to on- and offload ship-to-ship and ship-to-quay and vice versa. The CBa6324 (i.e. 63m x 23,5m) is outfitted with aLiebherr CBG 350 crane with a grab loadcapacity of 35 t @ 12-36m and a hook loadcapacity of 45 ton @ 12-36m. The averagethroughput will be around 20,000 tons a day. There?s accommodation for 12 crew, incl. a pantry, a change room, an office and of course cabins. Several of these newtransshipment barges are currently being built, with the first ready for delivery in No- vember 2012 (The Netherlands).Prelude FLNG Started at Drydocks World ? Dubai Drydocks World said that Shell?s Prelude Floating Liquefied Natural Gas (FLNG) facility ? the world?s first ? was initiated with a Steel Cutting cere- mony of its Turret, the world?s largest ? at more than 90 m in height and 30 m in diameter and weighing 11,500 tons. The Turret will be built as six mod- ules at the Dubai shipyard and shipped to Samsung Heavy Industry's yard in Korea, where these will be integrated into the FLNG facility, once it is built. Drydocks World had earlier been awarded the Turret building contract by SBM Offshore as part of its contract with Technip for the engineering, procurement and construction (EPC) of the FLNG Turret Mooring System. Once con- structed the FLNG facility will be towed to location where it will be perma- nently moored in 250m-deep water through the turret, providing weathervaning capabilities, and a 4x4 mooring system. The FLNG facility and its mooring system have been designed to withstand extreme weather con- ditions including a Category 5 cyclone. Bulk Carrier Trio Debuts in Greece ?Ultimate Fuel Savers? MR June12 # 2 (9-16):MR Template 6/12/2012 8:41 AM Page 10