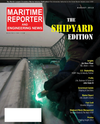
Page 85: of Maritime Reporter Magazine (August 2012)
The Shipyard Edition
Read this page in Pdf, Flash or Html5 edition of August 2012 Maritime Reporter Magazine
August 2012www.marinelink.com 85By Scott Reeve, President, Composite Advantage Berthing a fast attack or fleet ballistic missile (Tri- dent) submarine requires skilled vessel handling, knowledge and practice. The larger Trident subs are 560 ft. long with a beam of 42 ft. and displace almost17,000 tons. When maneuvering them into port a deep draft camel is a crucial aide to optimizingberthing and mooring procedures. The camel creates and maintains separation between a sub and a water- front facility. Deflecting or compressing with vessel movement, the camel prevents damage to the hull, div- ing planes, screws, fairings, special skin treatments and appurtenances by absorbing the sub?s energy. Over the years factors like operational requirements, environmental conditions and pier and fender system designs have led to the use of more than 17 different types of deep draft camels built from a variety of ma- terials at Navy waterfront facilities. When the Navy decided to standardize these camels to increase effi- ciency, it also wanted a design and material that would help lower operational costs and resist the ravages of saltwater affecting wood and steel camels. The Navy tapped Composite Advantage LLC of Dayton, Ohio and Whitman, Requardt & Associates LLP of Balti- more, Md., for a design-build project to develop and fabricate a composite universal camel able to accom- modate all classes of submarines at any port in the world. Gregg Blaszak, a principle of Coastline Com- posites Inc., Lancaster, Pa., said, ?A universal or one- size-fits-all deep draft camel offers greater flexibility in berthing submarines, helps reduce inventory, allows support between Navy installations and provides a cost savings by improving operational efficiency.? Coastline Composites is a consulting group specializ-ing in composite products and applications. Follow- ing the Navy?s selection of Composite Advantage, the firm acted as an owner?s representative for the Navy to review the portions of the project relating to the com- posite materials.?To effectively marry composites with steel and concrete, you need composite design and manufac- turing expertise,? said Blaszak. ?CA was very cost competitive but they also had the necessary design and fabrication skills to handle the unique properties of composites.? CA teamed with WR&A to develop the concept for the camel?s internal structure. ?We knew they had previous experience designing waterfront in- frastructure for the Navy and felt they would be a good fit with us for the project,? says Andy Loff, vice-pres- ident of CA. The Navy?s criteria for the new camel included the ability to absorb the massive amount of energy generated by a berthing submarine, freeboard, as well as list and trim angles and overall flotation sta- bility. The flotation criteria posed a challenge. ?We were dealing with a unique shape and the cri- teria were somewhat at odds with each other in that if we designed to meet one requirement, issues surfaced with the other criteria,? says Matthew Lambros, struc- tural engineer for WR&A. ?This was largely due to the fact that a number of properties affecting the camel such as volumes and densities can vary and must be considered to establish precise flotation calculations.? The first design step was to determine the amount of kinetic energy the camel would need to absorb from a submarine to avoid over or under-designing the structure. WR&A used the kinetic energy standard for the Navy?s largest sub in less-than-ideal environmen- tal conditions so that the camel could be used with any combination of sub class and port in the world. Arch rubber fenders had to be selected that could effectively absorb the energy without transferring too large of a reaction force on the supporting structure. Compo-nents and connection details were designed based onthe magnitude and path of resulting forces. Once pre-liminary geometry was established along with weights of the building material, drawings and specifications were generated for CA.?Unlike working with existing shapes and steel pa- rameters, the advantage of using composite material is that you can design much more specifically for the project,? says Lambros. ?We were able to determine what we needed in terms of structural strength andstiffness allowing CA to mold the product to those physical and mechanical properties. The use of com- posites made the design-build process much more pro- ductive because of the ability to work in such close coordination with CA fabrication personnel. Testing revealed an unexpected challenge. The large structure equipped with rubber fenders weighed in at 70,000 lbs. with an additional 35,000lbs of ballast required to meet flotation require- ments established by the Navy. ?We had to look at how the camel could be lifted during maintenance or installation in a manner that was structurally efficient, yet maintained safety measures and easy handling forbase personnel,? says Loff. CA and WR&A developed specialized lifting methodology able to accommodate the unique char- acteristics of the composite material and loads. Steelbars were integrated in the composite panels along the top edges of the camel. Pockets were formed around the bars at four locations so that lifting slings couldbe attached instead of traditional lifting hooks or padeyes at discreet points. Specialty lifting bars distrib- ute the camel?s extreme self-weight along the length of the steel rod instead of focusing forces at single dis-creet points.Flotation and structural strength were alsoaided by the use of TYCOR, a fiber-reinforced foam core inside the composite panels creating a ?sand-wich? cross section. The patented material reduces the weight of the panels and its unique architecture en-hances strength. ?The core, incorporated with fiber- glass fabric and infused with resin, contributes to flotation which eliminated the need to add extra flota- tion foam,? Loff says. Following fabrication, composite sub-assemblies were assembled on-site at SUBASE New London in Groton, Conn., in October 2010 and the camel was in- stalled in the water in November 2010 for a flotation test. ?When we designed the camel we developed the ballast to consist of a combination of concrete massand steel plates,? says Lambros. ?The steel plates are movable inside the camel so that if the camel flotation trim is a few degrees off, then the ballast can be ad- justed by moving the plates. Each plate weighs just 50 lbs. so they can easily be moved by a one person.? Following completion of the flotation test, the camels were delivered to the Navy for installation on their newest submarine pier. The set of universal composite camels has been suc- cessfully used by berthing submarines at New Lon- don for over a year. ?Feedback from Navy facilities engineers and port operations is very favorable,? says Loff. ?Elimination of recurring maintenance is a major operational benefit and multiple bases are now looking at the composite camels for future use.? Ac- cording to Loff the Navy also is looking at using the technology for CVN aircraft carrier camels as well asship separators to provide standoff distance between the ship and the pier or ship-to-ship. The standoff dis- tance for the separators is adjustable.The composite ship separators offer applications at commercial ports for sea-going vessels that include cruise ships and cargo ships. The composite technol- ogy and construction CA developed for vehicle bridges also is suited for waterfront infrastructure such as piers, wharves, walkways and brows. CASE STUDYPORT TECHBerthing a Submarine Project to design, develop and fabricate a composite universal camel for all classes of submarinesMR#8 (82-89):MR Template 8/13/2012 1:50 PM Page 85