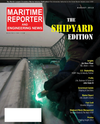
Page 92: of Maritime Reporter Magazine (August 2012)
The Shipyard Edition
Read this page in Pdf, Flash or Html5 edition of August 2012 Maritime Reporter Magazine
92Maritime Reporter & Engineering News When the U.S. Geological Survey (USGS) approached Great Lakes Ship- yard in Cleveland last June, the govern- ment research agency had a tall order: Build two new, 70-ft. aluminum vessels for delivery before September 2011. For the USGS, the $8.2m contract meant the agency would replace two of its oldest research vessels in its Great Lakes fleet, floating laboratories equipped with state-of-the-art instrumen-tation designed to improve the under- standing of deep-water ecosystems and fish species in Lake Erie and Lake On- tario. One boat is moored at USGS Lake Erie Biological Station in Sandusky, Ohio; the other at the USGS Lake On- tario Biological Station in Oswego, N.Y. For Great Lakes Shipyard, a division of the Great Lakes Towing Company lo- cated on Cuyahoga River?s Old River Channel just off of Lake Erie, the order posed the ship designer and fabricator?s biggest challenge in recent history ? de-signing and fabricating not one, but two aluminum ships; something the company had never done. Aluminum SpecsUSGS approached Great Lakes with basic preliminary designs, specifying tobuild the vessels out of 5083 aluminum alloy after performing a feasibility study, said Christopher C. Peifer, Great Lakes assistant vice president of engineering andthe company?s safety officer. ?The three biggest factors that drove them to choos- ing aluminum were draft, speed, andweight,? he explains. ?Lake Erie is the shallowest of all the Great Lakes and min- imizing the vessel's draft is crucial for ac- cess to certain regions. The speed allows the owner to reduce transit time between sampling locations and the weight deter- mines where the vessel can be pulled out of the water for the winter months.? According to Peifer, all these factors are closely related to each other and madethe determining factor on the USGS? choice of material. ?The aluminum was a big change for us. We had worked with it a bit on smaller jobs, but we had not built an entire boat from it,? Peifer said. ?But we were up to the challenge of learning the ropes whilewe worked on such a tight turnaround.? Design ConsiderationsThe USGS order required the shipyard to design and build two ships in just over a year, a taxing time-frame for those ex- perienced in building aluminum boats In order to build these vessels, Peifer and other on-site engineers received 3D preliminary drawings from the USGS and then turned these drawings into 2D layouts in which all materials and sizesof plate are indicated on the drawings. Each part in the layout is assigned a piecenumber and is sent to the materialprovider, who then cuts the pieces and sends them back to the shipyard with a set of assembly drawings. ?We used those assembly drawings, to tack the pieces together and weld it outfrom bow to stern,? said shipyard general manager, Joseph J. Craine. ?Actually we do more than just weld it out. We do all of the ancillary work, as well, including electrical, piping, insulation and more.It?s a turnkey process.? Reshaping a Welding Department Taking on the project required the ship- Keeping Production Moving on a Challenging Aluminum Ship Project Material Specifications and Quick Turnaround Requirements Drive Great Lakes Shipyard Welding Efficiency Gains MR#8 (90-97) Real:MR Template 8/13/2012 9:02 AM Page 92