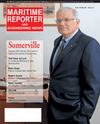
Page 38: of Maritime Reporter Magazine (October 2012)
Marine Design & Construction
Read this page in Pdf, Flash or Html5 edition of October 2012 Maritime Reporter Magazine
38Maritime Reporter & Engineering News The international marine indus-try faces unprecedented chal- lenges today. Energy costs are rising, as are concerns about re-duced pollutant emissions, water ballast treatment and other environmental im- pacts. A tight credit market and cash- strapped operators mean that engineersmust deliver designs with a high degree of fidelity and reliability while reducing the development cycle. Extreme weather, hazardous cargoes and other challenging operating conditions present the need tocontinually innovate, implement new ma- terials and deliver analyses confidently. How can naval architects overcome these challenges? One answer lies inleveraging the power of engineering sim- ulation in an integrated environment with broad capabilities.For more than 40 years, ANSYS? robust capabilities allow engineers to conduct design analyses and optimization studiesthat reflect the most demanding environ- ments ? ultimately helping naval archi- tects to design new hulls, appendages, sails, propellers, platforms, and otherequipment.By using finite element (FE) technol- ogy, engineers can quickly arrive at groundbreaking innovations without in- vesting time and money in physical pro- totypes. Engineers can subject theirdesigns to extreme temperatures, waves, wind loading, cargo weights and other real-world conditions to assess their re- sponse. Not only can engineers verify and introduce their ideas faster, but they can predict how their designs will per- form under actual operating conditions.Engineering resources are amplified, as design teams these days rely on advanced numerical modeling to automate andstreamline the design process.Marine and offshore engineers face special challenges as their designs mustwithstand a range of operational, tran-sient, accidental and dynamic loads.Improved Support for Large Simulations Geometrically modeling the complexi- ties of an offshore structure is a numeri- cally large and compound task. So naval architects often rely on high-performancecomputing (HPC) environments to con- duct these simulations.Improved performance for large mod- els is a primary focus for ANSYS to re- duce product development cycle times and lost productivity. The technology is designed to deliver maximum speed and efficiency across multiple computing processors. ANSYS customers have leveraged HPC environments and en- hanced technologies to achieve signifi- cant reductions in their simulationruntimes, particularly when running dis-tributed tasks across multiple processors. Fluid?structure interaction problems thatrely on computational fluid dynamics(CFD) studies are now easier to set up, solve and post-process with ANSYS CFX and ANSYS Fluent. In ANSYS Workbench, popular CFD solution meth- ods share a common workflow, where in- teraction with other products is enabledthrough controlled workflows. This re- duces the learning curve for engineers who want to use both CFD technology and structural engineering solutions.Customized Capabilities While many technology enhancements benefit all ANSYS users, improving solvers targeted specifically at marine ap- plications, including industry-leading so-lutions ANSYS Aqwa and ANSYS Asas, has been a top priority. Both Aqwa and Asas have benefited from major changes in the last few years, with the intention to add even more ca- pabilities in the future. Recent enhance-ments include more user-friendly modeling, the ability to import geome-tries from third-party CAD packages,trouble-free design parameterization, ef-ficient load definition and the option to choose multiple wave theories. In addition, ANSYS DesignXplorer of- fers improved capabilities for conducting optimization studies. A new direct opti- mization system can gather information via data links to other systems or compo-nents that contain design-point data. This new system supports earlier decision- making, decreasing overall development cycle and eliminating a lengthy trial-and- error period. Engineers can easily visual-ize the tradeoffs among design variables and make choices that support the desired output. Figure 1 demonstrates a numberof design variables considered in the de- sign of a jacket structure. Design assessment in Workbench now includes code-checking capabilities withBeamcheck and Fatjack. Design Assess- TECHNICAL FEATURE OFFSHORE Finite Element SolutionsFor the Global Offshore Market By Spiro J. Pahos (Courtesy of Subsea 7) Figure 1: ANSYS DesignXplorer helps engineers to weigh a number of design variables before arriving at an optimal solution.Figure 2: Post-processing piles in Workbench (left) and in the traditional ANSYS interface (right)Figure 3: Stress intensity results of the decompression chamber MR#10 (34-41):MR Template 10/4/2012 11:00 AM Page 38