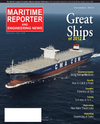
Page 49: of Maritime Reporter Magazine (December 2012)
Great Ships of 2012
Read this page in Pdf, Flash or Html5 edition of December 2012 Maritime Reporter Magazine
December 2012www.marinelink.com 49ity control department with all of the lengths, breadths,and cross-dimensions of the project. Overall, he says using the current system ?helped us move closer to being competitive with the bigger yards.? Kintner adds that it has also helped reduce the amount of overtime that is required to stay on schedule.Currently, Senseco is building three tugboats and a 100,000-barrel barge for Reinauer, and a 420-foot by 120-foot drydock for Caddell Drydock and Repair Co.of Staten Island. Seattle-based US Fab, the new construction division of Vigor Industrial, began using 3D product models from Genoa Design in early 2012. Kevin Hein, US Fab?s Director of Engineering, notes that the drawings are se- quenced to reflect the intermediate work products and the order in which the work progresses through the ves- sel, such as the installation of a hanger bracket, a hanger, and then a pipe?if it can be installed early. Sometimes the sequencing is counterintuitive, such as waiting until later in the process to install the foundation that goesaround a pipe. All the hotwork is normally done to- gether, at an earlier stage, he explains). ?In the more conventional approach, all of the pipe in the system is shown on the deck on a specific level,? he notes, ?and they tell you to go install it.? Echoing Bush, he says that the work has traditionally relied on knowledgeable craftsmen, and that this is different at US Fab because the workforce is younger and less experienced than in the average shipyard. The sequencing of tasks allows for welding in the downhand position, Hein adds, as opposed to having to weld overhead, resulting in three to five times greater efficiencies. The early definition of materials and their location also enables electrical subcontractors to installthe hangers for the wireways before the steel has left the shop. Hein notes there has been a reduction in rework since US Fab began using this system, and he cites interfer- ence checking as an additional benefit. During the de- sign process, he explains, objects can be moved and left in the wrong spot and temporary installations can be cre-ated and then unintentionally left in the drawing, some- times creating thousands of lines of interference.?Genoa uses software tools to the greatest extent they can,? he says, ?which automates the process of checking to see if a piece of pipe is interfering with another pieceof pipe or 3D object. They?ve designed a process that minimizes interference, and then they use automation to wade through the remaining interference. This use of automation complementsthe use of talented and ex- perienced designers whocan then focus on otherareas rather than some ofthe monotonous tasks.? US Fab is currently working with Genoa on a 362-foot ferry (83-footbeam) for the Washington State Department of Trans- portation (Washington State Ferry system) that israted to carry 144 cars and 1,500 passengers. The way Genoa Design?s president, Leonard Pecore, describes their process, naval architects and marine en- gineering systems design technologists build the vessel in 3D (?the product model?) on the computer. This con- tains geometric information, build strategy, tooling in- formation, and vendor information. The company?s key differentiator, he adds, is the application of Toyota?s lean manufacturing principles to shipbuilding, internally as well as externally in the methodology that is passed along to clients. Efficiencies, he says, are evidenced in cost savings, higher quality, workflow, and reduction of waste. Analyzing the most efficient sequence for putting the ship together is key. They may use one less letter, for example, when numbering a part. ?It saves two sec- onds each time the part is cut,? Pecore says, ?but if there are 5,000 of those parts, that?s 10,000 seconds (2.75 hours).? From their St. John?s office, Genoa creates product models of tankers, tugs, ferries, barges, tow- boats, offshore supply vessels, icebreakers, and military vessels. Ozkan Steel distributes bulb flats and steel profiles to north american shipyards from Houston TX. Ozkan Steel is producer of bulb flats, equal angles, unequal angles and flat bars for shipbuilding industry. For inquiries please contact us:Address: 2616 South Loop W Suite 593 Houston TX, 77054 Tel: 713-569-4035 E: [email protected] (Continued from 47) A Boon to ShipbuildingMR#12 (42-49):MR Template 12/4/2012 2:37 PM Page 49